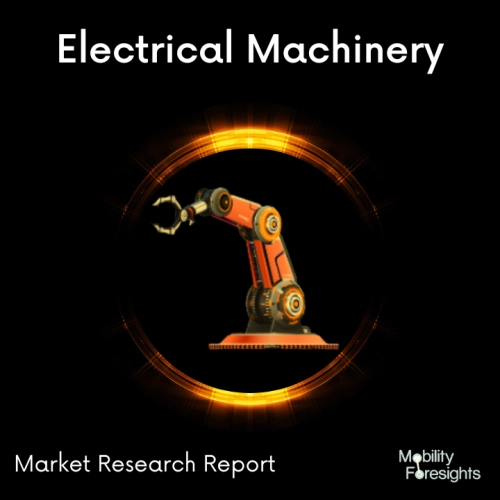
- Get in Touch with Us
Last Updated: Apr 25, 2025 | Study Period: 2023-2030
Because they represent one of the applications of magnetostriction, one of the earliest identified smart behaviours of materials, magnetostrictive actuators (MA) play a significant part in the perception of utility of smart materials and devices.
Little ferromagnetic particles make up a magnetostrictive substance. Due to their partially filled "3d" shells, these ferromagnets, which are often made of iron, nickel, or cobalt, have modest magnetic moments. Electromagnetic energy can be transformed into mechanical energy and vice versa using magnetostrictive materials.
It is possible to build sensors that measure a magnetic field or recognise a force using this effect. The material would experience a strain that could be measured as a result of the applied magnetic field or force.
The Global Magnetostrictive actuator market accounted for $XX Billion in 2022 and is anticipated to reach $XX Billion by 2030, registering a CAGR of XX% from 2023 to 2030.
A magnetostrictive actuator consists of a magnetostrictive component that lengthens when a magnetic field is applied, a translating component mechanically attached to the magnetostrictive component to translate the change in length into the desired action, and a selectively-energised coil surrounding the magnetostrictive component to apply a magnetic field to the magnetostrictive component and thereby selectively change the length of the magnetosphere
The cryogenic magnetostrictive materials are used in the creation of the creative actuators of this innovation. At cryogenic temperatures, the favoured magnetostrictive material experiences the largest strains.
These strains, which are close to 0.63%, are higher than those permitted by piezoelectric materials at the 20â60 K design working temperatures for the NGST. In order to stretch the magnetostrictive material and produce the desired movement, the innovation also uses electrical coils to supply the controllable strength magnetic field.
The capacity to precisely shape and position the optical surfaces of the NGST is mainly dependent on the current that flows to the actuator. A special actuator control system that operates at cryogenic conditions and is based on commercially available electronics is used to fulfil this requirement.
By reducing internal resistance by a factor of 15 to 30, this cryogenic operation gives the actuators a high efficiency current source with an accuracy of 10 ppm.
Sl no | Topic |
1 | Market Segmentation |
2 | Scope of the report |
3 | Abbreviations |
4 | Research Methodology |
5 | Executive Summary |
6 | Introduction |
7 | Insights from Industry stakeholders |
8 | Cost breakdown of Product by sub-components and average profit margin |
9 | Disruptive innovation in the Industry |
10 | Technology trends in the Industry |
11 | Consumer trends in the industry |
12 | Recent Production Milestones |
13 | Component Manufacturing in US, EU and China |
14 | COVID-19 impact on overall market |
15 | COVID-19 impact on Production of components |
16 | COVID-19 impact on Point of sale |
17 | Market Segmentation, Dynamics and Forecast by Geography, 2023-2030 |
18 | Market Segmentation, Dynamics and Forecast by Product Type, 2023-2030 |
19 | Market Segmentation, Dynamics and Forecast by Application, 2023-2030 |
20 | Market Segmentation, Dynamics and Forecast by End use, 2023-2030 |
21 | Product installation rate by OEM, 2023 |
22 | Incline/Decline in Average B-2-B selling price in past 5 years |
23 | Competition from substitute products |
24 | Gross margin and average profitability of suppliers |
25 | New product development in past 12 months |
26 | M&A in past 12 months |
27 | Growth strategy of leading players |
28 | Market share of vendors, 2023 |
29 | Company Profiles |
30 | Unmet needs and opportunity for new suppliers |
31 | Conclusion |
32 | Appendix |