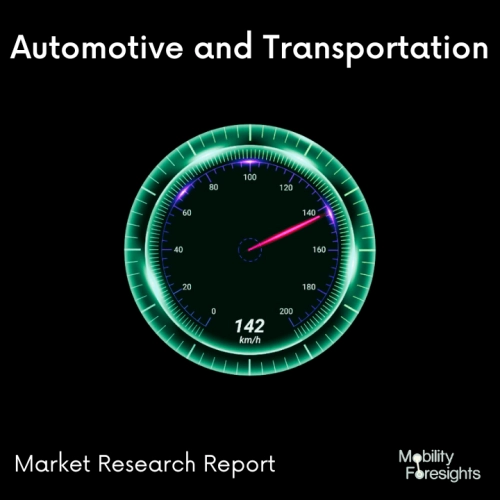
- Get in Touch with Us
Last Updated: Apr 25, 2025 | Study Period: 2024-2030
Electric vehicle plastic is the material that makes up an electric vehicle's parts. The majority of electric cars employ metallic batteries, however, their weight prohibits them from operating as intended.
Plastic is therefore used to keep the automobile operating smoothly. Plastic is utilized in the production and delivery of electric vehicle parts.
Electric car polymers are used in the bonnet portion, interior, exterior, and baggage compartment.
In addition to interior and exterior furnishings, power plant systems, transmission systems, and other things, plastic vehicles include Polypropylene (PP), Polyurethane (PUR), Acrylonitrile Butadiene Styrene (ABS), Polyvinyl Chloride (PVC), Polyoxymethylene (POM), Polystyrene (PS), Polycarbonate, Polyamide (PC), Acrylic (PMMA), and others (Polyethylene). (Polyethylene).
The Malaysia EV Plastics Market accounted for $XX Billion in 2023 and is anticipated to reach $XX Billion by 2030, registering a CAGR of XX% from 2024 to 2030.
In order to create laminated sandwich panels, EconCore has created new honeycomb cores using its patented technology, a combination of polyphenylene ether (PPE) and SABIC's NORYL GTX resin.
When compared to honeycomb constructions manufactured with conventional thermoplastics, the novel honeycomb core exhibits improved heat performance, better dimensional stability, and reduced water absorption.
The novel core material may be employed in demanding applications like some automotive, e-mobility, and solar components because of these qualities. Additionally, creating an all-thermoplastic sandwich panel with this innovative honeycomb core and thermoplastic composite layers can make recycling easier.
Using the company's unique method, EconCore honeycombs are created from a single continuous thermoplastic sheet. Without the need for additional procedures, the material is extruded and in-line shaped into the honeycomb structure in this special process.
To be more precise, a series of extrusion and thermoforming operations are used to convert the extruded film into a half-hexagonal web that is then immediately folded into a thermoplastic honeycomb structure.
Due to this continuous process' great efficiency, production expenses are kept to a minimum, which increases the product's economic competitiveness.
The technique also makes it possible to combine the creation of the honeycomb core with the skin lamination process, opening up the possibility of efficient, continuous production of laminated sandwich panels with additional value.
Sl no | Topic |
1 | Market Segmentation |
2 | Scope of the report |
3 | Abbreviations |
4 | Research Methodology |
5 | Executive Summary |
6 | Introduction |
7 | Insights from Industry stakeholders |
8 | Cost breakdown of Product by sub-components and average profit margin |
9 | Disruptive innovation in the Industry |
10 | Technology trends in the Industry |
11 | Consumer trends in the industry |
12 | Recent Production Milestones |
13 | Component Manufacturing in US, EU and China |
14 | COVID-19 impact on overall market |
15 | COVID-19 impact on Production of components |
16 | COVID-19 impact on Point of sale |
17 | Market Segmentation, Dynamics and Forecast by Geography, 2024-2030 |
18 | Market Segmentation, Dynamics and Forecast by Product Type, 2024-2030 |
19 | Market Segmentation, Dynamics and Forecast by Application, 2024-2030 |
20 | Market Segmentation, Dynamics and Forecast by End use,2024-2030 |
21 | Product installation rate by OEM, 2023 |
22 | Incline/Decline in Average B-2-B selling price in past 5 years |
23 | Competition from substitute products |
24 | Gross margin and average profitability of suppliers |
25 | New product development in past 12 months |
26 | M&A in past 12 months |
27 | Growth strategy of leading players |
28 | Market share of vendors, 2023 |
29 | Company Profiles |
30 | Unmet needs and opportunity for new suppliers |
31 | Conclusion |
32 | Appendix |