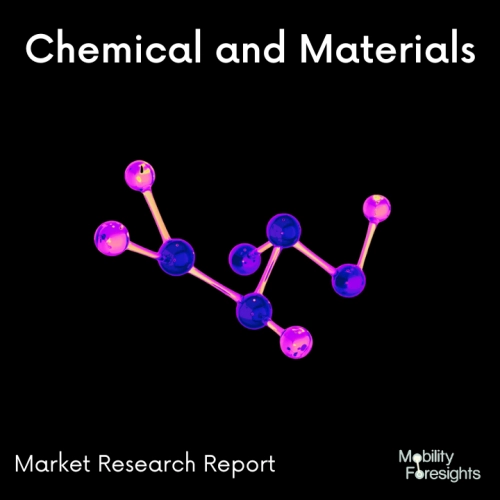
- Get in Touch with Us
Last Updated: Apr 25, 2025 | Study Period: 2024-2030
Carbon fiber can be used as a reinforcement in the production of orthopedic implants in the medical field. To create a composite with improved properties, carbon fibers are frequently combined with other materials like matrices, resin, or hardeners.
Composite materials called carbon-reinforced implants are made of carbon fiber sheets that are inlaid into a PEEK resin. The mechanical properties of these implants give them a lot of advantages over traditional metal orthopedic implants.
Arbon fiber is a polymer that can be used for a lot of different things and has gained a lot of recognition in the engineering field because of its special properties. Numerous industries, including aerospace, automotive, military, and medical, utilize carbon fiber.
When making a composite, the orientation of the fiber and the lamination sequence are very important. The properties are estimated using these formulas. The relationship between midplane strain, curvature, force, and moments is established. The composite is theoretically optimized.
The composites are also represented by Abaqus models. It is shown some of the numerical results that were obtained. The manner in which amputees can participate in sports has changed as a result of the incorporation of carbon fiber reinforced polymer (CFRP) composites into the structure of prosthetics.
The Flex Foot, developed by Phillips in 1985, was the first below-the-knee prosthesis entirely made of CFRP. It is depicted in Figure 1. Carbon fiber is a more wear-resistant and flexible material than traditional prosthetic materials. Carbon fiber's adaptability allows for individualized medical implants. Carbon fiber medical devices can be made for specific needs by the medical industry.
The Global medical carbon fiber implants market accounted for $XX Billion in 2023 and is anticipated to reach $XX Billion by 2030, registering a CAGR of XX% from 2024 to 2030.
The launch of ENDOLIGN composite, a new medical carbon fiber implants material for use in implantable load bearing medical device applications requiring blood, bone, or tissue contact for more than 30 days, has been announced by In vibio, a provider of biomaterial solutions for the medical device market.
The ENDOLIGN process and composite are the first non-metallic biomaterials for medical implants that combine the extensive biocompatibility and imaging compatibility of polymers with the high strength of metals.
The ENDOLIGN composite's biocompatibility testing demonstrates that it meets or exceeds ISO 10993 standards for long-term implantable medical devices.
By combining a PEEK-OPTIMA polymer matrix in the form of a pre-impregnated tape with high levels of continuous carbon fibers, ENDOLIGN is produced in accordance with ISO 9001 quality standards.
After that, you can shape this tape into rods or other shapes. When tested in molded unidirectional rod form, the continuous carbon fibers significantly improve the material's mechanical properties, increasing its stiffness from 3.5GPa to 150GPa and its flexural strength from approximately 150MPa for the PEEK-OPTIMA polymer.
Sl no | Topic |
1 | Market Segmentation |
2 | Scope of the report |
3 | Abbreviations |
4 | Research Methodology |
5 | Executive Summary |
6 | Introduction |
7 | Insights from Industry stakeholders |
8 | Cost breakdown of Product by sub-components and average profit margin |
9 | Disruptive innovation in the Industry |
10 | Technology trends in the Industry |
11 | Consumer trends in the industry |
12 | Recent Production Milestones |
13 | Component Manufacturing in US, EU and China |
14 | COVID-19 impact on overall market |
15 | COVID-19 impact on Production of components |
16 | COVID-19 impact on Point of sale |
17 | Market Segmentation, Dynamics and Forecast by Geography, 2024-2030 |
18 | Market Segmentation, Dynamics and Forecast by Product Type, 2024-2030 |
19 | Market Segmentation, Dynamics and Forecast by Application, 2024-2030 |
20 | Market Segmentation, Dynamics and Forecast by End use, 2024-2030 |
21 | Product installation rate by OEM, 2023 |
22 | Incline/Decline in Average B-2-B selling price in past 5 years |
23 | Competition from substitute products |
24 | Gross margin and average profitability of suppliers |
25 | New product development in past 12 months |
26 | M&A in past 12 months |
27 | Growth strategy of leading players |
28 | Market share of vendors, 2023 |
29 | Company Profiles |
30 | Unmet needs and opportunity for new suppliers |
31 | Conclusion |
32 | Appendix |