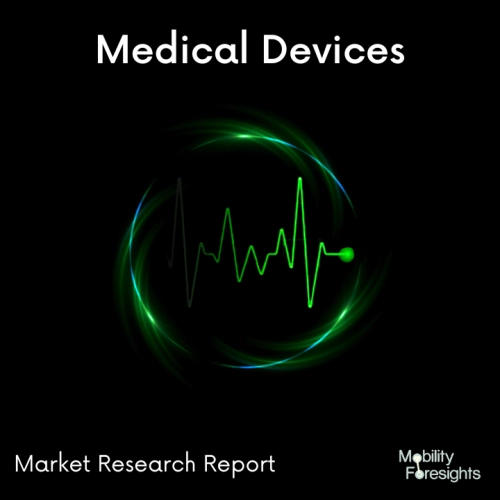
- Get in Touch with Us
Last Updated: Apr 25, 2025 | Study Period: 2024-2030
A motion controller's main function is to regulate the motion device's dynamics. The motor driver transforms the motion controller's command inputs into the power signals needed to move the motor. Any mechanical device that generates motion and is driven by a motor is referred to as a motion device.
Motion devices are mechanical positioning tools like linear actuators, rotational stages, and stages of linear translation. Even while a stage's or actuator's parameters are key selection factors, they might not be comprehensive or immediately applicable for all applications.
It is crucial to have a thorough understanding of the innate capacities of the parts that make up a stage for this reason. The most popular parts used in high precision positioning equipment are briefly discussed in this section along with their benefits and drawbacks.
The materials required to make the body, the mechanism that permits translation or rotation, and the drive mechanism are the three primary parts of a motion device.
The Global Medical device motion control system market accounted for $XX Billion in 2021 and is anticipated to reach $XX Billion by 2030, registering a CAGR of XX% from 2024 to 2030.
ACS Motion Control launches two new solutions for micromachining.Two new devices in the SPiiPlus family of EtherCAT-based motion controllers and motor drives have been made available by ACS Motion Control.
The CMxa and UDMxa are designed for high-precision industrial applications that need demanding velocity control and micron to nanometer resolution, such as laser micromachining, metrology, inspection, alignment, and other high-precision processes.
For existing CMba/hp and UDMba/hp users, these two new products are intended to be drop-in replacements, facilitating product migration. Both include new, optional safety features including SS1 and STO while reducing jitter and noise.
The CMxa is an EtherCAT master motion controller that has built-in motor drivers and makes use of potent servo control algorithms to optimise motion system performance.
Its universal motor and encoder technology gives system designers the ability to manage the majority of motor and stage types, greatly enhancing the flexibility of system design. The SPiiPlus ADK Suite, which includes numerous sophisticated servo tuning and application development tools, supports the CMxa.
The CMxa has 1, 2, or 3 built-in drives with up to 265Vac and 30A peak current output per axis, and it may be programmed to control up to 64 total axes. System designers have access to a wide range of distributed EtherCAT drives in addition to its integrated motor drivers.
For complex multi-axis machine designs, the CMxa's fixed servo sampling and update rate and high-speed distributed clock EtherCAT network provide the closely synchronised real-time control required.For brand-new machine designs and current CMba and CMhp users, the CMxa is strongly advised.
Sl no | Topic |
1 | Market Segmentation |
2 | Scope of the report |
3 | Abbreviations |
4 | Research Methodology |
5 | Executive Summary |
6 | Introduction |
7 | Insights from Industry stakeholders |
8 | Cost breakdown of Product by sub-components and average profit margin |
9 | Disruptive innovation in the Industry |
10 | Technology trends in the Industry |
11 | Consumer trends in the industry |
12 | Recent Production Milestones |
13 | Component Manufacturing in US, EU and China |
14 | COVID-19 impact on overall market |
15 | COVID-19 impact on Production of components |
16 | COVID-19 impact on Point of sale |
17 | Market Segmentation, Dynamics and Forecast by Geography, 2024-2030 |
18 | Market Segmentation, Dynamics and Forecast by Product Type, 2024-2030 |
19 | Market Segmentation, Dynamics and Forecast by Application, 2024-2030 |
20 | Market Segmentation, Dynamics and Forecast by End use, 2024-2030 |
21 | Product installation rate by OEM, 2023 |
22 | Incline/Decline in Average B-2-B selling price in past 5 years |
23 | Competition from substitute products |
24 | Gross margin and average profitability of suppliers |
25 | New product development in past 12 months |
26 | M&A in past 12 months |
27 | Growth strategy of leading players |
28 | Market share of vendors, 2023 |
29 | Company Profiles |
30 | Unmet needs and opportunity for new suppliers |
31 | Conclusion |
32 | Appendix |