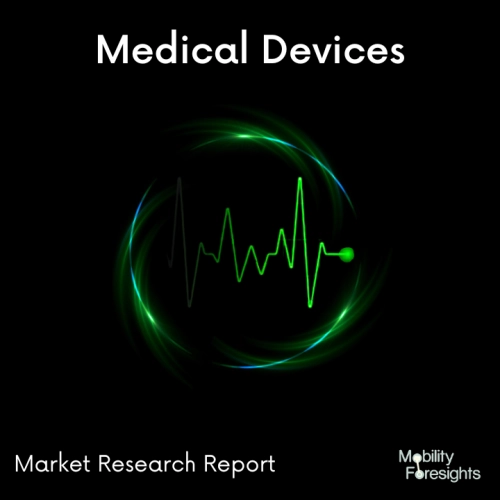
- Get in Touch with Us
Last Updated: Apr 25, 2025 | Study Period: 2023-2030
HDI PCBs are multilayer circuit boards with tightly routed layers. The boards are bonded together by lamination, and the layers are electrically connected using various sorts of circuits. The etching of the inner copper layers is the preliminary step in the lamination process.
Printed circuit boards with high-density interconnect, or HDI, have more wiring per unit space than conventional printed circuit boards. Microvias, blind and buried vias, built-up laminations, and high signal performance considerations are generally considered to be HDI PCBs.
The development of printed circuit boards has kept pace with the need for smaller and faster products as technology has changed.
The vias, pads, copper traces, and gaps on HDI boards are all smaller. Since HDIs have denser wiring, their PCBs are smaller, lighter, and have fewer layers. One HDI board can replace the functionality of several PCBs that were previously used in a device.
The Global Medical device ultra-HDI PCB market accounted for $XX Billion in 2021 and is anticipated to reach $XX Billion by 2030, registering a CAGR of XX% from 2022 to 2030.
HDI PCB Technology Improves Equipment Performance. Due to the small size of parts and semiconductor packages that offer exceptional qualities in cutting-edge new products, such as touchscreen phones, high-density interconnection (HDI) PCB uses contemporary technology to increase the functioning of circuit boards.
All the way back to the original printed circuit board (PCB), there is evidence.Since that time, PCB technology has developed continuously, moving from single-sided to double-sided to multilayer, flex, rigid-flex, and other configurations.
PCB design was influenced by component evolution as it sought to offer more effectiveness, capability, and connection density. The pattern has not changed; components continue to dictate how PCB design changes. One example of this are power LEDs.
The same is true for high-density packing elements like BGA and micro-BGA, also known as ball-grid arrays. PCB makers were compelled to create circuits that could handle such fine pitch components by PCB designers.
To print the design for high-density components, engineers, circuit board makers, raw material suppliers, and PCB manufacturers have created procedures and laminates. Interconnection is becoming more and more difficult as the pitch is being lowered. Because pads have less room, fewer vias and holes must be used.
Sl no | Topic |
1 | Market Segmentation |
2 | Scope of the report |
3 | Abbreviations |
4 | Research Methodology |
5 | Executive Summary |
6 | Introduction |
7 | Insights from Industry stakeholders |
8 | Cost breakdown of Product by sub-components and average profit margin |
9 | Disruptive innovation in the Industry |
10 | Technology trends in the Industry |
11 | Consumer trends in the industry |
12 | Recent Production Milestones |
13 | Component Manufacturing in US, EU and China |
14 | COVID-19 impact on overall market |
15 | COVID-19 impact on Production of components |
16 | COVID-19 impact on Point of sale |
17 | Market Segmentation, Dynamics and Forecast by Geography, 2023-2030 |
18 | Market Segmentation, Dynamics and Forecast by Product Type, 2023-2030 |
19 | Market Segmentation, Dynamics and Forecast by Application, 2023-2030 |
20 | Market Segmentation, Dynamics and Forecast by End use, 2023-2030 |
21 | Product installation rate by OEM, 2023 |
22 | Incline/Decline in Average B-2-B selling price in past 5 years |
23 | Competition from substitute products |
24 | Gross margin and average profitability of suppliers |
25 | New product development in past 12 months |
26 | M&A in past 12 months |
27 | Growth strategy of leading players |
28 | Market share of vendors, 2023 |
29 | Company Profiles |
30 | Unmet needs and opportunity for new suppliers |
31 | Conclusion |
32 | Appendix |