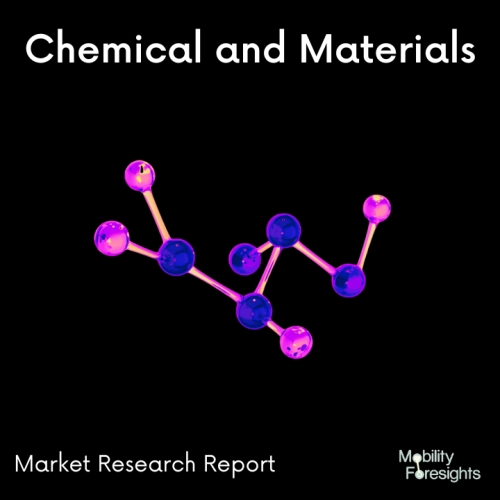
- Get in Touch with Us
Last Updated: Apr 25, 2025 | Study Period: 2024-2030
Metal anodizing is a surface treatment process widely used in various industries to enhance the durability, corrosion resistance, and aesthetics of metal components. It involves creating a controlled oxide layer on the surface of a metal, typically aluminium or titanium, through an electrochemical process.
Anodizing not only improves the physical properties of metals but also offers several advantages that make it a preferred choice in numerous applications.
Advantages of Metal Anodizing:
All in all, metal anodizing is a versatile surface treatment process that offers numerous advantages for enhancing the durability, corrosion resistance, and aesthetics of metal components. From improved corrosion resistance and wear resistance to aesthetic customization and electrical insulation, anodizing provides a range of benefits.
Moreover, the environmental friendliness, easy maintenance, and enhanced adhesion properties make anodizing a preferred choice in various industries, including architecture, automotive, electronics, and more. With its ability to transform metal surfaces into durable and visually appealing finishes, metal anodizing continues to play a vital role in modern manufacturing and design.
The Global Metal Anodizing market accounted for $XX Billion in 2023 and is anticipated to reach $XX Billion by 2030, registering a CAGR of XX% from 2024 to 2030.
Sherwin Williams has introduced Powdura 4000 Anodite powder coatings and a number of Powdura product selection tools, expanding its line of products for the architectural building materials sector.
Since decades, the paint and coatings company has collaborated with manufacturers of windows, doors, stairwells, handrails, wall panels, benches, lights and other high-traffic areas, utilising their extensive product line that satisfies all AAMA performance standards for coatings.
A 12-colour recommended collection of the new Powdura 4000 Anodite powder coatings is available. These colours are created to mimic the appearance of anodized metal surfaces while providing a smooth, ultra-matte, powder-coated finish.
This system includes a variety of appealing colours and exceptionally strong, TGIC-free technology built in for long-term weather protection. With a coating that is specifically designed to last, designers may get the ultimate anodized finish.
Powdura 4000 Anodite coatings are more colour-consistent between components, may be restored, and can be used on materials other than aluminium. Without a clear coat, they can also be applied in a single coat.
Powdura 4000 Anodite, which complies with AAMA 2604 requirements, is the most recent addition to the Powdura series of high-performance architectural powder coatings, which also includes Powdura 4000 and Powdura 5000 products that are AAMA 2604 and AAMA 2605 certified.
When specifying powder coatings on metal building goods, durability and weather resistance are non-negotiable requirements. Because of this, Powdura 5000 coatings are designed to offer a strong finish with exceptional UV protection, guaranteeing that your construction can withstand challenging weather conditions for years to come.
North America
The North American market, particularly the USA, will be one of the prime markets for (Metal Anodizing) due to the nature of industrial automation in the region, high consumer spending compared to other regions, and the growth of various industries, mainly AI, along with constant technological advancements. The GDP of the USA is one of the largest in the world, and it is home to various industries such as Pharmaceuticals, Aerospace, and Technology. The average consumer spending in the region was $72K in 2023, and this is set to increase over the forecast period. Industries are focused on industrial automation and increasing efficiency in the region. This will be facilitated by the growth in IoT and AI across the board. Due to tensions in geopolitics, much manufacturing is set to shift towards the USA and Mexico, away from China. This shift will include industries such as semiconductors and automotive.
Europe
The European market, particularly Western Europe, is another prime market for (Metal Anodizing) due to the strong economic conditions in the region, bolstered by robust systems that support sustained growth. This includes research and development of new technologies, constant innovation, and developments across various industries that promote regional growth. Investments are being made to develop and improve existing infrastructure, enabling various industries to thrive. In Western Europe, the margins for (Metal Anodizing) are higher than in other parts of the world due to regional supply and demand dynamics. Average consumer spending in the region was lower than in the USA in 2023, but it is expected to increase over the forecast period.
Eastern Europe is anticipated to experience a higher growth rate compared to Western Europe, as significant shifts in manufacturing and development are taking place in countries like Poland and Hungary. However, the Russia-Ukraine war is currently disrupting growth in this region, with the lack of an immediate resolution negatively impacting growth and creating instability in neighboring areas. Despite these challenges, technological hubs are emerging in Eastern Europe, driven by lower labor costs and a strong supply of technological capabilities compared to Western Europe.
There is a significant boom in manufacturing within Europe, especially in the semiconductor industry, which is expected to influence other industries. Major improvements in the development of sectors such as renewable energy, industrial automation, automotive manufacturing, battery manufacturing and recycling, and AI are poised to promote the growth of (Metal Anodizing) in the region.
Asia
Asia will continue to be the global manufacturing hub for (Metal Anodizing Market) over the forecast period with China dominating the manufacturing. However, there will be a shift in manufacturing towards other Asian countries such as India and Vietnam. The technological developments will come from China, Japan, South Korea, and India for the region. There is a trend to improve the efficiency as well as the quality of goods and services to keep up with the standards that are present internationally as well as win the fight in terms of pricing in this region. The demand in this region will also be driven by infrastructural developments that will take place over the forecast period to improve the output for various industries in different countries.
There will be higher growth in the Middle East as investments fall into place to improve their standing in various industries away from petroleum. Plans such as Saudi Arabia Vision 2030, Qatar Vision 2030, and Abu Dhabi 2030 will cause developments across multiple industries in the region. There is a focus on improving the manufacturing sector as well as the knowledge-based services to cater to the needs of the region and the rest of the world. Due to the shifting nature of fossil fuels, the region will be ready with multiple other revenue sources by the time comes, though fossil fuels are not going away any time soon.
Africa
Africa is expected to see the largest growth in (Metal Anodizing Market) over the forecast period, as the region prepares to advance across multiple fronts. This growth aligns with the surge of investments targeting key sectors such as agriculture, mining, financial services, manufacturing, logistics, automotive, and healthcare. These investments are poised to stimulate overall regional growth, creating ripple effects across other industries as consumer spending increases, access to products improves, and product offerings expand. This development is supported by both established companies and startups in the region, with assistance from various charitable organizations. Additionally, the presence of a young workforce will address various existing regional challenges. There has been an improvement in political stability, which has attracted and will continue to attract more foreign investments. Initiatives like the African Continental Free Trade Area (AfCFTA) are set to facilitate the easier movement of goods and services within the region, further enhancing the economic landscape.
RoW
Latin America and the Oceania region will showcase growth over the forecast period in (Metal Anodizing Market). In Latin America, the focus in the forecast period will be to improve their manufacturing capabilities which is supported by foreign investments in the region. This will be across industries mainly automotive and medical devices. There will also be an increase in mining activities over the forecast period in this region. The area is ripe for industrial automation to enable improvements in manufacturing across different industries and efficiency improvements. This will lead to growth of other industries in the region.
Margin Comparison (Highest to lowest) | Region | Remarks |
1 | Europe | The supply chain demands and the purchasing power in the region enable suppliers to extradite a larger margin from this region than other regions. This is for both locally manufactured as well as imported goods and services in the region. |
2 | North America | Due to the high spending power in this region, the margins are higher compared to the rest of the world, but they are lower than Europe as there is higher competition in this region. All the suppliers of goods and services target USA as a main market thereby decreasing their margins compared to Europe |
3 | Asia | Lower purchasing power, coupled with higher accessibility of services in this regions doesnât enable suppliers to charge a high margin making it lower than Europe and North America. The quality of goods and services are also affected due to this aspect in the region |
4 | Africa and ROW | The margins are the lowest in this region, except for Australia and New Zealand as the countries in this region donât have much spending power and a large portion of the products and services from this area is exported to other parts of the world |
USAâ $210 billion is allocated to federal R&D with main focus on health research, clean energy, semiconductor manufacturing, sustainable textiles, clean energy, and advanced manufacturing. Investments by private players are mainly focused on technological development including 5G infrastructure and AI in the region.
Europeâ EIC is investing â¬1 billion to innovative companies in sectors like AI, biotechnology, and semiconductors. There is also a focus on developing the ecosystem in the continent as well as improving the infrastructure for developing industries such as electric vehicles and sustainable materials. Private players are targeting data centers, AI, battery plants, and high end technological R&D investments.
Asiaâ There are investments to tackle a range of scientific and technological advancements in this region mainly coming in from China, India, South Korea, and Japan. This will include artificial intelligence, 5G, cloud computing, pharmaceutical, local manufacturing, and financial technologies. Many countries are aiming to be digital hubs including Saudi Arabia.
Africaâ Investments in the region are focused on improving the technological capabilities in the region along with socio-economic development and growth. Private participants of investments in this region is venture capital dominated who are targeting the various growth elements of the region as social stability improves. The major industries are fintech, easier lending, and manufacturing.
Latin America â The focus in the region is for fintech, e-commerce, and mobility sectors. There are also investments in improving manufacturing in the region. Local investments is focused on improving the healthcare, and transportation infrastructure in the region. The region is attracting foreign investments to improve their ability to utilize the natural resources present in the region.
Rest of the Worldâ The investments in this region are focused on clean energy, green metals, and sustainable materials. Funds in Australia are focused on solar energy and battery technologies, along with high end futuristic areas such as quantum computing. The main countries of private investment in ROW will be Australia, Canada, and New Zealand.
Sl no | Topic |
1 | Market Segmentation |
2 | Scope of the report |
3 | Abbreviations |
4 | Research Methodology |
5 | Executive Summary |
6 | Introduction |
7 | Insights from Industry stakeholders |
8 | Cost breakdown of Product by sub-components and average profit margin |
9 | Disruptive innovation in the Industry |
10 | Technology trends in the Industry |
11 | Consumer trends in the industry |
12 | Recent Production Milestones |
13 | Component Manufacturing in US, EU and China |
14 | COVID-19 impact on overall market |
15 | COVID-19 impact on Production of components |
16 | COVID-19 impact on Point of sale |
17 | Market Segmentation, Dynamics and Forecast by Geography, 2024-2030 |
18 | Market Segmentation, Dynamics and Forecast by Product Type, 2024-2030 |
19 | Market Segmentation, Dynamics and Forecast by Application, 2024-2030 |
20 | Market Segmentation, Dynamics and Forecast by End use, 2024-2030 |
21 | Product installation rate by OEM, 2023 |
22 | Incline/Decline in Average B-2-B selling price in past 5 years |
23 | Competition from substitute products |
24 | Gross margin and average profitability of suppliers |
25 | New product development in past 12 months |
26 | M&A in past 12 months |
27 | Growth strategy of leading players |
28 | Market share of vendors, 2023 |
29 | Company Profiles |
30 | Unmet needs and opportunity for new suppliers |
31 | Conclusion |
32 | Appendix |