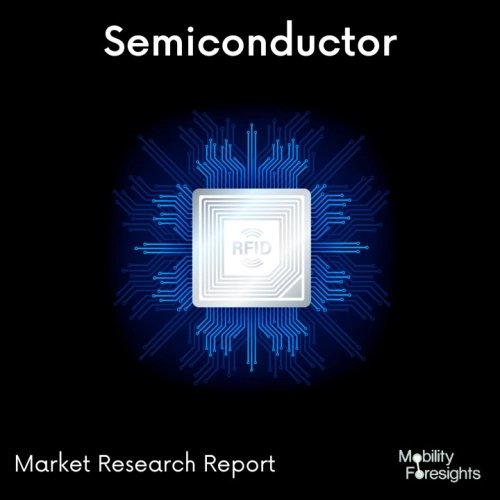
- Get in Touch with Us
Last Updated: Apr 25, 2025 | Study Period:
Engineering professionals may produce tiny, complicated pieces using micromachining. These components can then be employed in studies to scale down large-scale processes.
Microfluidics and Organ on a Chip are two examples of applications for micromachining.
Mechanical micromachining, often known as micromachining, is a manufacturing process that involves the subtractive production of objects or features having at least some of their dimensions in the micrometre range (1-999 m) using mechanical microtools with geometrically defined cutting edges.
Photolithography, laser, micro-EDM, and micromechanical machining (micro-cutting and micro-milling), which are the main topics of this study, are the most crucial techniques utilised for Page 3 micromachining.
A spring-mass-damp system, as seen, can approximate a micromachined accelerometer to first-order precision. It comprises a proof mass m suspended by an effective spring constant k-tuned compliant suspension system.
The movement or vibration of the body is what the accelerometer measures. It is capable of detecting even microscopic vibrations.
It picks up the vibration and transforms it into a piezoelectric action. When pressure and tension create energy, a piezoelectric effect happens.
An accelerometer is a tool that gauges a structure's vibration or acceleration of motion. The piezoelectric material is "squeezed" by the mass due to the force of vibration or a change in velocity (acceleration), which results in an electrical charge that is proportionate to the force applied to it.
The movement or vibration of the body is what the accelerometer measures. It is capable of detecting even microscopic vibrations.
It picks up the vibration and transforms it into a piezoelectric action. When pressure and tension create energy, a piezoelectric effect happens.
The Global micromachined accelerometers market accounted for $XX Billion in 2022 and is anticipated to reach $XX Billion by 2030, registering a CAGR of XX% from 2024 to 2030.
development of a micromachined accelerometer for measuring particle acceleration.
Design and simulation of a wideband, low-noise microfabricated accelerometer,Using a novel microfabrication technique that enables decoupled control of the device's properties,Experimentally proven bandwidth of 5.2 kHz, open-loop dynamic range of 145 dB, and noise level of 0.5 g/Hz are among the accelerometer's performance data.
describing the development of a micromachiend accelerometer with a focus on its design, construction, and experimental outcomes.
This accelerometer is meant to be utilised in the detection of acoustic signals, with the major requirements being low noise, broad bandwidth, and excellent linearity.
Analytical modelling and discussion of the device design requirements are presented. Detailed information on microfabrication is supplied in order to develop prototypes.
The suggested manufacturing method enables accurate and independent control of the capacitive gap as well as the device's structural elements.
Device prototypes were created and described. When operating at atmospheric pressure, measurements of the device's performance show that the noise floor has a resonance frequency of 5.2 kHz, sensitivity of 0.9 pF/g, and an open-loop dynamic range of more than 145 dB.
The tool satisfies the specifications for measuring sonar waves in the frequency range of 50 Hz to 5 kHz with minimal background noise.
Sl no | Topic |
1 | Market Segmentation |
2 | Scope of the report |
3 | Abbreviations |
4 | Research Methodology |
5 | Executive Summary |
6 | Introduction |
7 | Insights from Industry stakeholders |
8 | Cost breakdown of Product by sub-components and average profit margin |
9 | Disruptive innovation in the Industry |
10 | Technology trends in the Industry |
11 | Consumer trends in the industry |
12 | Recent Production Milestones |
13 | Component Manufacturing in US, EU and China |
14 | COVID-19 impact on overall market |
15 | COVID-19 impact on Production of components |
16 | COVID-19 impact on Point of sale |
17 | Market Segmentation, Dynamics and Forecast by Geography, 2024-2030 |
18 | Market Segmentation, Dynamics and Forecast by Product Type, 2024-2030 |
19 | Market Segmentation, Dynamics and Forecast by Application, 2024-2030 |
20 | Market Segmentation, Dynamics and Forecast by End use, 2024-2030 |
21 | Product installation rate by OEM, 2023 |
22 | Incline/Decline in Average B-2-B selling price in past 5 years |
23 | Competition from substitute products |
24 | Gross margin and average profitability of suppliers |
25 | New product development in past 12 months |
26 | M&A in past 12 months |
27 | Growth strategy of leading players |
28 | Market share of vendors, 2023 |
29 | Company Profiles |
30 | Unmet needs and opportunity for new suppliers |
31 | Conclusion |
32 | Appendix |