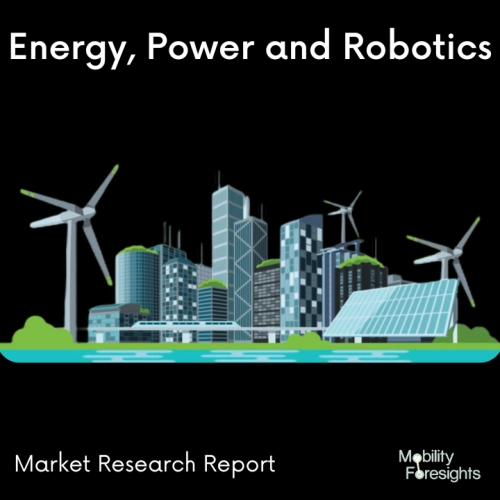
- Get in Touch with Us
Last Updated: Apr 25, 2025 | Study Period: 2024-2030
The global microreactor technology market is experiencing significant growth and innovation as it plays a pivotal role in the chemical and pharmaceutical industries. Microreactors, also known as micro-scale continuous flow reactors, are small-scale devices designed for chemical reactions. They have gained prominence due to their unique capabilities and advantages.
Microreactors are at the forefront of the trend towards miniaturization in chemical processing. Their small size and high surface area-to-volume ratio offer advantages in terms of efficiency and rapid reactions.
Microreactors are instrumental in pharmaceutical research and manufacturing. They enable precise control over reactions, leading to higher product quality and reduced production costs.
The market is expanding to include new players and startups focused on microreactor development and applications. This leads to increased innovation and competition.
the global microreactor technology market is on an upward trajectory, driven by the need for efficient and sustainable chemical processes, as well as emerging applications in pharmaceuticals and energy. The technology's versatility, safety benefits, and potential for innovation position it as a key player in various industries seeking to improve their processes and reduce environmental impact.
Microreactor technology involves conducting (bio)chemical reactions within extremely small devices, typically with dimensions measuring less than a millimeter. These microreactors leverage their high surface area-to-volume ratios to enhance mass and heat transport properties.
In function, microreactors resemble traditional large-scale reactors, as they use nuclear reactions to heat water and produce steam. This steam then drives a turbine generator to generate electricity. Microreactors offer the potential to synthesize materials more efficiently compared to conventional batch processing methods.
The key advantages of microreactors stem from their ability to optimize mass transfer, thermodynamics, and the significant surface area relative to their volume. Additionally, they offer engineering advantages in handling unstable intermediates during reactions.
Beyond generating electricity, microreactors can serve non-electric purposes such as district heating, water desalination, and hydrogen fuel production, providing a reliable and secure source of power for various commercial applications. Unlike large centralized power stations, their compact size allows for easy transportation and rapid on-site deployment.
Another notable feature of microreactors is their infrequent need for refueling, as the reactor core is designed to operate for three years or longer. These microreactors represent a small, environmentally friendly energy and heat source that can be conveniently transported by truck. They are fully manufactured in a factory and then swiftly delivered to the installation site, ensuring a high degree of safety and self-regulation based on fundamental physical principles.
Various materials, including polymers, silicon, metals, stainless steel, glass, and ceramics, are employed in the construction of microreactors.
The Global microreactor technology market accounted for $XX Billion in 2022 and is anticipated to reach $XX Billion by 2030, registering a CAGR of XX% from 2024 to 2030.
The continuous flow method known as microreactor technology is based on plug flow reactors. While providing quick dynamic responses and robustness, it uses a small amount of reagents. The technology enables precise temperature control and effective mixing techniques.
A microreactor is a device that conducts chemical reactions in a confinement with typical lateral dimensions below 1 mm; the most prevalent type of such confinement are microchannels. In the discipline of micro process engineering, microreactors are investigated along with other equipment that facilitates physical processes, such as micro heat exchangers.
In contrast to/in comparison to a batch reactor, the microreactor is often a continuous flow reactor. In comparison to standard scale reactors, microreactors have many benefits. These benefits include significant increases in energy efficiency, reaction speed and yield, safety, reliability, scalability, on-site/on-demand production, and a much finer level of process control.
In the chemical and pharmaceutical industries, there is rising demand for miniaturization. Continuous processingâs rising acceptance in the biotechnology and pharmaceutical sectors. A growing market for products of high quality and little harm to the environment.
Improvements in operational effectiveness and product quality brought about by microreactor technology. Microreactors are becoming more widely used in new fields.
The market for microreactor technology is progressively growing on a global scale as a result of key driving reasons such expanding demand for 3D printed microreactors because of their relative cost and high design potential, rising restrictions, and rising safety concerns in a number of industries.
The pharmaceutical industryâs adoption of MRT is being driven by technology improvements and a rising nanopharmaceuticals market. There are more chances in the Nano-pharmaceutics industry because pharmaceutical markets are developing in developed economies all over the world.
The expanding Nano Pharmaceutics Market is a key factor in the expansion of the Microreactor Technology Market within the pharmaceutical sector. Manufacturers of fine and specialized chemicals who want to reduce their production costs while addressing environmental issues have come to accept microreactor technology on a large scale.
The microreactorâs high level of compatibility with mass- and heat-transfer operations during mixing serves to raise awareness of the device within the context of the entire chemical industry. Microreactor technology is anticipated to gain significant popularity because it makes one-step reactions possible while removing the risk of alternate reactions, resulting in superior finished product quality and yields.
The demand for the microreactor technology is also being driven by the provision of clarity on key operating parameters and the facilitation of seamless process flexibility alongside increased productivity.
Key pharmaceutical companies are competing to produce new medications for the market and increase research and development throughput due to the extraordinarily high costs associated with developing new drugs.
Microreactor technology is being adopted primarily in the context of drug development procedures due to its capacity to shorten time-to-market, which continues to be one of the highly valued elements. For thermal processing and chemical synthesis, microreactors employ reusable medium.
The materials covered include metal composites, composites, and ceramics. Ceramics, which comprise alumina & silica gel, are the most widely used material type in the sector. Since they donât emit any dangerous substances into the environment when properly disposed of after each cycle, these materials are both affordable and safe to use.
A compact, standalone tool used for chemical or polymer synthesis is known as a disposable microreactor. These plastic reactors can be discarded after use and are normally built of that material. Due to their compact size and ease of use, they are frequently employed in laboratories.
ThalesNano and Linde Engineering sign partnership to develop and commercialize microreactor technology for green hydrogen production. The partnership will focus on developing and commercializing microreactor technology for the production of green hydrogen from water and sunlight.
Chemtrix and Evonik Industries collaborate to develop new microreactor technology for fine chemical production. The collaboration will focus on developing and commercializing microreactor technology for the production of fine chemicals in a more sustainable and cost-effective way.
Syrris and Nestlé partner to develop new microreactor technology for food and beverage production. The partnership will focus on developing and commercializing microreactor technology for the production of food and beverage ingredients in a more consistent and safe way.
Ehrfeld Mikrotechnik and BASF partner to develop new microreactor technology for materials production. The partnership will focus on developing and commercializing microreactor technology for the production of materials in a more precise and controlled way.
Sl no | Topic |
1 | Market Segmentation |
2 | Scope of the report |
3 | Research Methodology |
4 | Executive Summary |
5 | Average B2b Price, By Region |
6 | Potential Opportunities for Client |
7 | Introduction |
8 | Insights from Industry stakeholders |
9 | Disruptive innovation in the Industry |
10 | Technology trends in the Industry |
11 | Consumer trends in the industry |
12 | Recent Production Milestones |
13 | Key Drivers for Global Microreactor Technology Market |
14 | New product development in past 12 months |
15 | Market Segmentation, Dynamics and Forecast by Geography, 2024-2030 |
16 | Market Segmentation, Dynamics and Forecast by Product Type, 2024-2030 |
17 | Market Segmentation, Dynamics and Forecast by Application, 2024-2030 |
18 | Market Segmentation, Dynamics and Forecast by End use, 2024-2030 |
19 | Competitive Landscape |
20 | M&A in past 12 months |
21 | Growth strategy of leading players |
22 | Market share of vendors, 2023 |
23 | Company Profiles |
24 | Unmet needs and opportunity for new suppliers |
25 | Conclusion |
26 | M&A in past 12 months |
27 | Growth strategy of leading players |
28 | Market share of vendors, 2023 |
29 | Company Profiles |
30 | Unmet needs and opportunity for new suppliers |
31 | Conclusion |
32 | Appendix |