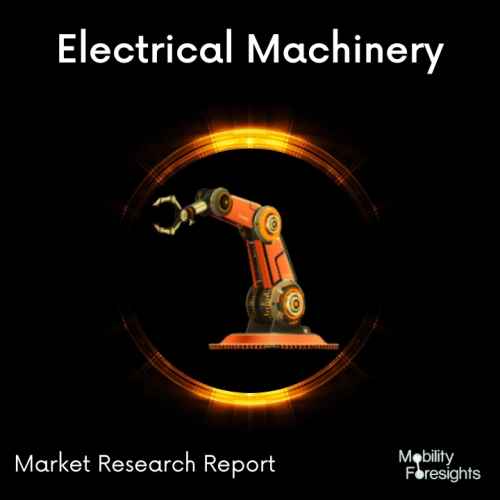
- Get in Touch with Us
Last Updated: Apr 25, 2025 | Study Period: 2024-2030
Machinery used in construction, agriculture, and forestry are examples of applications for mobile hydraulic systems. Due to the extremely high power density of hydraulic systems and their low space requirements, this type of power is particularly effective where high output power and minimal weight are required.
The flow of a liquid medium, typically oil, through your hydraulic system is properly directed by a hydraulic valve. The position of a spool determines the direction of the oil flow. A water driven framework can work - according to necessities - by utilising valves. When the preset pressure is reached, sequence valves direct the flow to another part of the hydraulic circuit.
When the maximum pressure in a particular area of the circuit has been reached, unloading valves direct the flow back to the tank. Advantages of a Hydraulic System Hydraulic systems are precise and simple to control.
Because there are fewer moving parts in hydraulic systems, they are simpler and easier to maintain.
Just pressure driven frameworks can convey steady force or power paying little mind to speed changes.It is simple to identify hydraulic system leaks.
The Mobile Hydraulic Valves accounted for $XX Billion in 2023 and is anticipated to reach $XX Billion by 2030, registering a CAGR of XX% from 2024 to 2030.
Eaton, a manufacturer of power management products, introduced its CLS sectional mobile valve a month ago.
The CLS has a highly modular design and one of the industry's smallest envelopes, as well as patented load sense bleed off, pre- and post-compensated load sense relief on each section.
The CLS sectional mobile valves are designed for mobile, off-highway equipment like excavators, refuse trucks, forestry, and agricultural machinery. They allow end users to prioritize work functions to increase productivity, machine efficiency, and safety.
According to Eaton global strategy and planning manager Nadine Powell, "The CLS sectional mobile valve was designed to streamline features â adding value without increasing size or sacrificing flexibility.
" With a number of available features that are unique to many load-sensing valves, such as priority flow sharing and local load sense relief on each section, customers can design the valve to meet the unique needs of their machine."
The pre- and post-compensated mobile valve is available with either mid-inlet or customer manifolds and up to ten working sections.
Models CLS100, CLS180, CLS250, or CLS350 of the valve are available to meet a variety of flow requirementsâ150 l/min, 220 l/min, 300 l/min, and 450 l/min, respectively. The working pressure at the inlet port of each valve is 350 bar, and the maximum pressure at the outlet port is 25 bar.
Depending on the machine duty cycle, Eaton introduced a new variable speed drive (VSD) pump solution that can save up to 70% of energy for machine building, manufacturing, oil and gas, and marine equipment.
The industrial pump solution, which can be used with open-loop or closed-loop motion control, allows for pump downsizing, quieter machine operation, and reduced or eliminated cooling requirements.
Choose one or more pumps from Eaton's PVM variable piston pumps, Hydrokraft variable piston pumps, or VMQ fixed vane pumps to complete the VSD solution.
The system can be controlled to meet the exact load requirements of the current duty cycle using Eaton VSDs with smart control, such as the PowerXL DG1 general purpose drive or the SPX 9000 high performance drive.
Eaton has worked to provide more energy-efficient solutions without sacrificing power or safety as energy costs continue to rise. "Energy consumption plays a significant role in overall machine operating costs."
Sl no | Topic |
1 | Market Segmentation |
2 | Scope of the report |
3 | Abbreviations |
4 | Research Methodology |
5 | Executive Summary |
6 | Introduction |
7 | Insights from Industry stakeholders |
8 | Cost breakdown of Product by sub-components and average profit margin |
9 | Disruptive innovation in the Industry |
10 | Technology trends in the Industry |
11 | Consumer trends in the industry |
12 | Recent Production Milestones |
13 | Component Manufacturing in US, EU and China |
14 | COVID-19 impact on overall market |
15 | COVID-19 impact on Production of components |
16 | COVID-19 impact on Point of sale |
17 | Market Segmentation, Dynamics and Forecast by Geography, 2024-2030 |
18 | Market Segmentation, Dynamics and Forecast by Product Type, 2024-2030 |
19 | Market Segmentation, Dynamics and Forecast by Application, 2024-2030 |
20 | Market Segmentation, Dynamics and Forecast by End use, 2024-2030 |
21 | Product installation rate by OEM, 2023 |
22 | Incline/Decline in Average B-2-B selling price in past 5 years |
23 | Competition from substitute products |
24 | Gross margin and average profitability of suppliers |
25 | New product development in past 12 months |
26 | M&A in past 12 months |
27 | Growth strategy of leading players |
28 | Market share of vendors, 2023 |
29 | Company Profiles |
30 | Unmet needs and opportunity for new suppliers |
31 | Conclusion |
32 | Appendix |