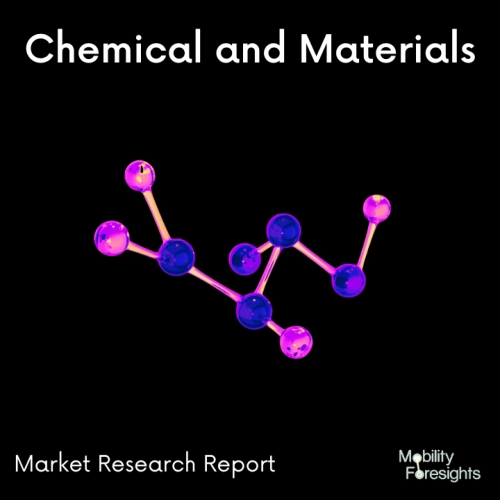
- Get in Touch with Us
Last Updated: Apr 25, 2025 | Study Period: 2024-2030
The exceptional combination of high-temperature resistance, corrosion resistance, and mechanical strength that NiCr alloys provide makes them ideal for usage in a variety of industrial applications.
The aerospace, energy, automotive, electronics, and other industries are just a few of the segments that make up the NiCr alloy market. NiCr alloys are utilized in the manufacture of gas turbine engines, exhaust systems, and other high-temperature components in the aerospace sector.
NiCr alloys are utilized in the energy sector to create power generation machineries like steam turbines and boilers. NiCr alloys are utilized in exhaust systems and catalytic converters in the automotive sector. NiCr alloys are utilized in the electronics sector to create heating components for a variety of appliances, including toasters and hair dryers.
The NiCr alloy market is impacted by a number of variables, including end-user demand, industrial expansion, regulations, and technical breakthroughs. The requirement for new materials with improved performance characteristics as well as increased applications in important industries are projected to drive the demand for NiCr alloys in the upcoming years.
The Global Nickel Chromium Alloy Market accounted for $XX Billion in 2022 and is anticipated to reach $XX Billion by 2030, registering a CAGR of XX% from 2024 to 2030.
The growing and extensive range of metal powders available for use in powder bed additive manufacturing (AM) now includes a new nickel alloy material from EOS, the world's top supplier of industrial 3D printing technologies for metals and polymers.
A nickel-chromium alloy known as EOS NickelAlloy IN939 is a novel material that offers a superb blend of strength in high-temperature environments, resistance to corrosion and oxidation, fatigue performance, and creep strength at temperatures up to 850 °C (1,560 °F).
Compared to comparable materials already on the market, EOS NickelAlloy IN939 has better tensile characteristics, validation, dependability, and crack resistance. EOSNickelAlloy IN939 parts can be hardened after manufacturing by utilizing heat treatments that precipitate hardening.
All of these features make EOS NickelAlloy IN939 ideal for processing on the EOS M 290 metal AM platform and make it ideal for use in manufacturing industrial gas turbines, including their vanes, blades, and heatshields, as well as microturbines, turbochargers, power industry parts and other energy industry applications exposed to high temperatures and harsh conditions.
Sl no | Topic |
1 | Market Segmentation |
2 | Scope of the report |
3 | Abbreviations |
4 | Research Methodology |
5 | Executive Summary |
6 | Introdauction |
7 | Insights from Industry stakeholders |
8 | Cost breakdown of Product by sub-components and average profit margin |
9 | Disruptive innovation in theIndustry |
10 | Technology trends in the Industry |
11 | Consumer trends in the industry |
12 | Recent Production Milestones |
13 | Component Manufacturing in US, EU and China |
14 | COVID-19 impact on overall market |
15 | COVID-19 impact on Production of components |
16 | COVID-19 impact on Point of sale |
17 | Market Segmentation, Dynamics and Forecast by Geography, 2024-2030 |
18 | Market Segmentation, Dynamics and Forecast by Product Type, 2024-2030 |
19 | Market Segmentation, Dynamics and Forecast by Application, 2024-2030 |
20 | Market Segmentation, Dynamics and Forecast by End use, 2024-2030 |
21 | Product installation rate by OEM, 2023 |
22 | Incline/Decline in Average B-2-B selling price in past 5 years |
23 | Competition from substitute products |
24 | Gross margin and average profitability of suppliers |
25 | New product development in past 12 months |
26 | M&A in past 12 months |
27 | Growth strategy of leading players |
28 | Market share of vendors, 2023 |
29 | Company Profiles |
30 | Unmet needs and opportunity for new suppliers |
31 | Conclusion |
32 | Appendix |