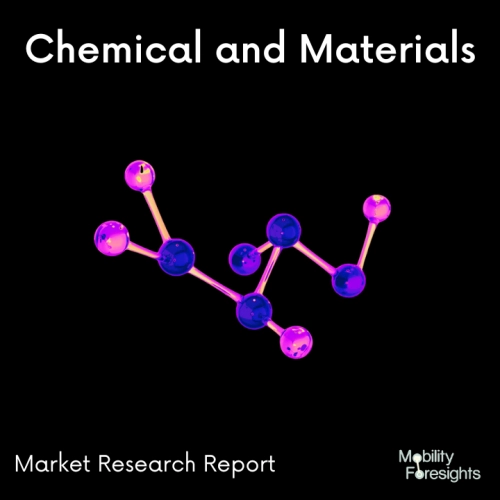
- Get in Touch with Us
Last Updated: Apr 26, 2025 | Study Period: 2024-2030
Nickel iron alloy is an alloy composed of iron and nickel. It is known for its high electrical resistivity, high strength, and good thermal and electrical conductivity.
Nickel iron alloy is also highly corrosion resistant and has good ductility and machinability. In addition, it is very resistant to stress corrosion cracking due to its nickel content.
It is commonly used in applications such as electrical and electronic components, aerospace components, and automotive components.
It is also used in the production of magnets and other magnetic materials due to its high magnetic permeability. Nickel iron alloy is often used in the production of electrical components such as transformers and motors due to its high electrical resistivity.
Nickel iron alloy is also used in the manufacture of various structural components due to its high strength and good ductility. It is commonly used in the production of aerospace components such as landing gear and fasteners due to its high strength and good corrosion resistance.
In addition, it is often used in the production of automotive components such as engine mounts and suspension components due to its good machinability.
Overall, nickel iron alloy is a versatile material with many applications due to its excellent properties. It is highly resistant to corrosion, has high strength and good machinability, and is highly electrical and thermally conductive. Therefore, it is an ideal choice for many applications in the automotive, aerospace, and electrical industries.
The Global Nickel Iron Alloy Market accounted for $XX Billion in 2023 and is anticipated to reach $XX Billion by 2030, registering a CAGR of XX% from 2024 to 2030.
With Sanicro® 825, Sandvik has introduced its first-ever nickel-iron-chromium alloy in bar and hollow bar, for enhanced performance in corrosive, high-temperature conditions. Sandvik is a developer and supplier of advanced stainless steel, special alloys, titanium, and other high-performance materials.
The company's expanding Sanicro® line of nickel alloys and austenitic stainless steels for harsh wet, corrosive, high-temperature, high-pressure, acidic, and marine conditions is expanded with Sanicro® 825 (UNS NO8825). Sanicro® 825 is a high-strength alloy with a minimum of nickel content.
It exhibits good corrosion resistance to organic, sulfuric, nitric, and phosphoric acids, seawater, caustic chloride alkalis, and ammoniac media. It also has superior resistance to stress corrosion cracking (SCC).
The new alloy is perfect for use in a variety of parts and installations, such as heat exchangers, evaporators, offshore pipe systems, seawater coolants, valves, and flanges. It is stable, simple to machine, and easy to weld. Oil & gas, chemical, petrochemical, pulp and paper, pickling equipment, nuclear fuel processing, and food processing are just a few of the industries it serves.
The creation of alloys may proceed more quickly thanks to recent developments in artificial intelligence. A group of researchers usually needs ten years to develop a new alloy.
To attain the desired qualities and be able to produce them economically, it takes a high level of skill and understanding of the interactions between the various alloying elements.
Artificial Intelligence (AI) has the ability to greatly reduce development time and assist even novice alloy developers in the field of new alloy development. Once an alloy is created, nickel is a metal that can truly express all of its potential.
Nickel is mostly used in stainless steel, an iron and chromium alloy to which nickel and other elements, including molybdenum, are added based on the desired qualities.
Heat-resistant alloys with elements like ruthenium and rhenium are based on nickel and are essential for jet engines. The functions and uses of nickel will grow as new alloys are developed for new purposes.
Sl no | Topic |
1 | Market Segmentation |
2 | Scope of the report |
3 | Abbreviations |
4 | Research Methodology |
5 | Executive Summary |
6 | Introduction |
7 | Insights from Industry stakeholders |
8 | Cost breakdown of Product by sub-components and average profit margin |
9 | Disruptive innovation in the Industry |
10 | Technology trends in the Industry |
11 | Consumer trends in the industry |
12 | Recent Production Milestones |
13 | Component Manufacturing in US, EU and China |
14 | COVID-19 impact on overall market |
15 | COVID-19 impact on Production of components |
16 | COVID-19 impact on Point of sale |
17 | Market Segmentation, Dynamics and Forecast by Geography, 2024-2030 |
18 | Market Segmentation, Dynamics and Forecast by Product Type, 2024-2030 |
19 | Market Segmentation, Dynamics and Forecast by Application, 2024-2030 |
20 | Market Segmentation, Dynamics and Forecast by End use, 2024-2030 |
21 | Product installation rate by OEM, 2023 |
22 | Incline/Decline in Average B-2-B selling price in past 5 years |
23 | Competition from substitute products |
24 | Gross margin and average profitability of suppliers |
25 | New product development in past 12 months |
26 | M&A in past 12 months |
27 | Growth strategy of leading players |
28 | Market share of vendors, 2023 |
29 | Company Profiles |
30 | Unmet needs and opportunity for new suppliers |
31 | Conclusion |
32 | Appendix |