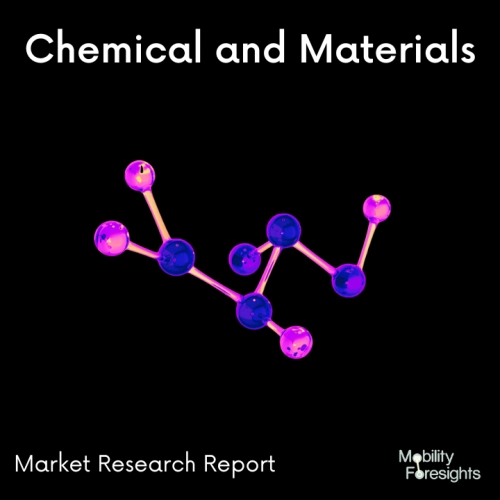
- Get in Touch with Us
Last Updated: Apr 26, 2025 | Study Period: 2024-2030
With a near-equiatomic composition of titanium and nickel (i.e., 49%â51%), Ni-Ti alloy, also known as Nitinol, is an alloy. Ni-Ti is a member of the group of alloys known as shape memory alloys, which may be permanently deformed at low temperatures and then recover their original shape when heated to a high temperature.
When compared to stainless steel alloys, nitinol alloys have higher strength and a lower elastic modulus. Nitinol wires behave in a manner that is extremely elastic, so after being loaded, they distort but immediately return to their former shape.
The Global Nickel Titanium Alloy Market accounted for $XX Billion in 2023 and is anticipated to reach $XX Billion by 2030, registering a CAGR of XX% from 2024 to 2030.
The unique flexibility of the Ti-Ni alloy is used in endodontics to create devices for root canal preparation. Numerous manufacturers have developed Ti-Ni alloy root canal instruments with a variety of designs and concepts since the first Ti-Ni alloy root canal instrument became commercially accessible in the early years. Although it is less than that of steel, the workability of Ti-Ni alloys is superior to that of other SMAs.
Workability is particularly favourable at temperatures above 700 °C, where the Ti-Ni alloy becomes more stretchy as a result of its decreased strength. It is advised to utilise a processing temperature of 700 °C because if too much titanium is present locally, such as through segregation, a liquid phase forms at temperatures over 950 °C and cracks may form during processing.
The need to prevent uncontrolled, local temperature increases brought on by processing heat is especially important given the hot rolling process's very quick working speed.
The martensite and austenite crystal structures in near-equiatomic Ti-Ni alloys are B2 for austenite and B19â² for martensite, respectively. Austenite may initially change to the R-phase, which then changes to martensite upon cooling, depending on the thermomechanical treatments applied.
Fully annealed specimens go directly from austenite to martensite, however adding a third element, raising the Ni concentration, ageing following solution treatment, annealing below the recrystallization temperature, thermal cycling, and annealing below the recrystallization temperature might result in the intermediate R-phase.
Sl no | Topic |
1 | Market Segmentation |
2 | Scope of the report |
3 | Abbreviations |
4 | Research Methodology |
5 | Executive Summary |
6 | Introduction |
7 | Insights from Industry stakeholders |
8 | Cost breakdown of Product by sub-components and average profit margin |
9 | Disruptive innovation in the Industry |
10 | Technology trends in the Industry |
11 | Consumer trends in the industry |
12 | Recent Production Milestones |
13 | Component Manufacturing in US, EU and China |
14 | COVID-19 impact on overall market |
15 | COVID-19 impact on Production of components |
16 | COVID-19 impact on Point of sale |
17 | Market Segmentation, Dynamics and Forecast by Geography, 2024-2030 |
18 | Market Segmentation, Dynamics and Forecast by Product Type, 2024-2030 |
19 | Market Segmentation, Dynamics and Forecast by Application, 2024-2030 |
20 | Market Segmentation, Dynamics and Forecast by End use, 2024-2030 |
21 | Product installation rate by OEM, 2023 |
22 | Incline/Decline in Average B-2-B selling price in past 5 years |
23 | Competition from substitute products |
24 | Gross margin and average profitability of suppliers |
25 | New product development in past 12 months |
26 | M&A in past 12 months |
27 | Growth strategy of leading players |
28 | Market share of vendors, 2023 |
29 | Company Profiles |
30 | Unmet needs and opportunity for new suppliers |
31 | Conclusion |
32 | Appendix |