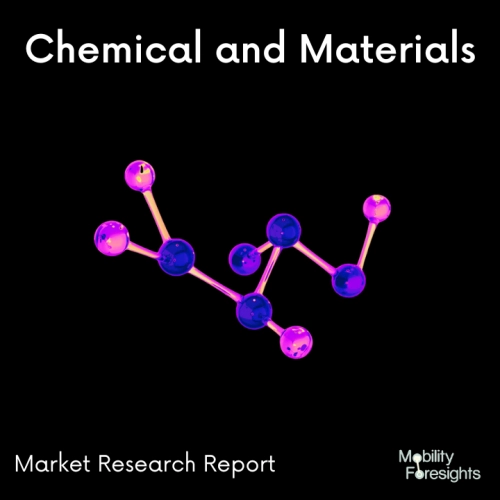
- Get in Touch with Us
Last Updated: Apr 25, 2025 | Study Period: 2024-2030
The two most popular commercial niobium alloys are ferroniobium and nickel-niobium. These are not suitable for use as engineering materials, but are used as handy sources of niobium for specialty steels and nickel-based superalloys instead. By using an iron-niobium or nickel-niobium alloy, issues caused by the niobium's high melting point are avoided.
Niobium is a highly sought-after material with uses in aircraft, electronics, nuclear power, and military. It is the lightest of the refractory metals, a group of metallic elements that display extraordinarily high melt temperatures and heat resistance.
This article examines the characteristics of niobium that make it unique from other refractory metals as well as its current uses and potential for usage in emerging technologies. Niobium alloys can have great radiation resistance in addition to having excellent mechanical strength and heat resistance.
This gives niobium, along with other refractory metals like tungsten and molybdenum, a wide range of applications in the nuclear sector. Niobium zirconium alloys are frequently utilized as structural components in nuclear reactors due to their exceptionally low neutron absorption cross-sections and strong resistance to liquid metals.
8 In high-temperature reactors, niobium is also used in instrumentation that is radiation-resistant at high temperatures. The development of next-generation nuclear fission reactors is also generating interest in niobium alloys.
Due to their exceptional ability to maintain mechanical strength at extremely high temperatures, recent research indicates that these materials might be ideal for use in the construction of structural components in Generation IV fission reactors.
The Global Niobium alloy Market accounted for $XX Billion in 2023 and is anticipated to reach $XX Billion by 2030, registering a CAGR of XX% from 2024 to 2030.
For alloy C103, a high-performance niobium alloy suitable for rocket, jet, and satellite propulsion applications, Sinta via, LLC, Hollywood, Florida, USA, has established patented material characteristics.
The M290 AM machine from EOS was used to create the refractory metal, which can be challenging to additively build. It is the twenty-ninth proprietary material Sint avia has created for use by its aerospace, defense, and space OEM clients.
niobium is widely recognized as an excellent material for space propulsion applications, specifically reaction control thrusters and attitude control thrusters, due to its extremely high melting point.
With this advancement, Sinta via is now able to provide its customers in the space industry with components that exhibit market-leading mechanical qualities. When paired with Sint avia's top-notch design and additive manufacturing
Sl no | Topic |
1 | Market Segmentation |
2 | Scope of the report |
3 | Abbreviations |
4 | Research Methodology |
5 | Executive Summary |
6 | Introdauction |
7 | Insights from Industry stakeholders |
8 | Cost breakdown of Product by sub-components and average profit margin |
9 | Disruptive innovation in theIndustry |
10 | Technology trends in the Industry |
11 | Consumer trends in the industry |
12 | Recent Production Milestones |
13 | Component Manufacturing in US, EU and China |
14 | COVID-19 impact on overall market |
15 | COVID-19 impact on Production of components |
16 | COVID-19 impact on Point of sale |
17 | Market Segmentation, Dynamics and Forecast by Geography, 2024-2030 |
18 | Market Segmentation, Dynamics and Forecast by Product Type, 2024-2030 |
19 | Market Segmentation, Dynamics and Forecast by Application, 2024-2030 |
20 | Market Segmentation, Dynamics and Forecast by End use, 2024-2030 |
21 | Product installation rate by OEM, 2023 |
22 | Incline/Decline in Average B-2-B selling price in past 5 years |
23 | Competition from substitute products |
24 | Gross margin and average profitability of suppliers |
25 | New product development in past 12 months |
26 | M&A in past 12 months |
27 | Growth strategy of leading players |
28 | Market share of vendors, 2023 |
29 | Company Profiles |
30 | Unmet needs and opportunity for new suppliers |
31 | Conclusion |
32 | Appendix |