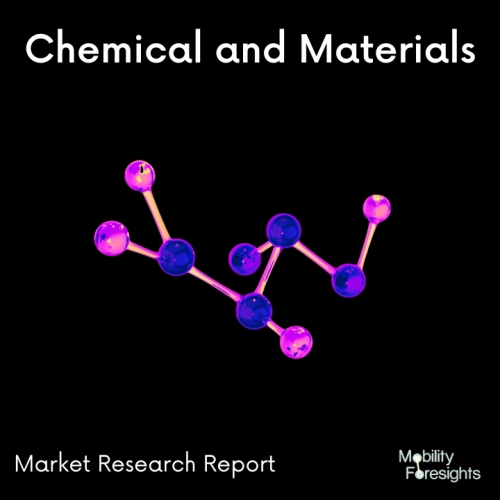
- Get in Touch with Us
Last Updated: Apr 25, 2025 | Study Period: 2024-2030
The negative leg of thermocouples of type N is made of the austenitic nickel-silicon alloy known as Nisil. It provides superior oxidation resistance and thermoelectric stability in air over 1000°C (1830°F) than type E, J, and K thermocouples. Gases containing sulphur cannot be subjected to Nisil alloy. Nisil is a non-magnetic alloy made of nickel, silicon, and traces of Mg.
TheGlobal Nisil alloy Marketaccounted for $XX Billion in 2023 and is anticipated to reach $XX Billion by 2030, registering a CAGR of XX% from 2024 to 2030.
Influence of nickel silicide's presence on hardness, elastic modulus and fracture toughness of gas-borides layer produced on Nisil-alloy. A two-zoned borides layer was created on Nisil alloy using a two-stage gas boriding process in a N2H2BCl3 atmosphere. 910 °C was used for the process. Two zones made up the microstructure, and their phase compositions varied. Just a combination of nickel borides (Ni2B, Ni3B) were present in the outer layer.
In addition to nickel borides, the inner zone also contains nickel silicide's (Ni2Si, Ni3Si). The purpose of the study was to evaluate the effects of nickel silicide's on the mechanical characteristics of the borides layer formed on an alloy based on nickel.
Under a 50 mN load, the nano indenter with a Bercovici diamond tip was used to determine the elastic modulus and hardness. Indentation elastic modulus (EI) and indentation hardness (HI) average values measured in the outer zone were (16.321.03 GPa) and (23216.15) GPa, respectively.
The inner zone's indentation hardness (6.8â12.54 GPa) and elastic modulus (111.79â153.99 GPa) were both decreased by the presence of nickel silicide's. Regarding the direction of crack propagation, a little anisotropy of the fracture toughness developed.
In a direction parallel (0°) to the top-surface, the higher fracture toughness was measured. Nickel borides, which were distinguished by a better fracture toughness than nickel silicide's, might be formed during the boriding process if the manufacture of nickel silicide's is required in order to boost the oxidation resistance. A Vickers micro indentation was used to test the boride layers' resistance to fracture under a stress of 0.981 N.
It was proven that the gas-borides layer became more brittle when nickel silicide's were present.
Sl no | Topic |
1 | Market Segmentation |
2 | Scope of the report |
3 | Abbreviations |
4 | Research Methodology |
5 | Executive Summary |
6 | Introduction |
7 | Insights from Industry stakeholders |
8 | Cost breakdown of Product by sub-components and average profit margin |
9 | Disruptive innovation in the Industry |
10 | Technology trends in the Industry |
11 | Consumer trends in the industry |
12 | Recent Production Milestones |
13 | Component Manufacturing in US, EU and China |
14 | COVID-19 impact on overall market |
15 | COVID-19 impact on Production of components |
16 | COVID-19 impact on Point of sale |
17 | Market Segmentation, Dynamics and Forecast by Geography, 2024-2030 |
18 | Market Segmentation, Dynamics and Forecast by Product Type, 2024-2030 |
19 | Market Segmentation, Dynamics and Forecast by Application, 2024-2030 |
20 | Market Segmentation, Dynamics and Forecast by End use, 2024-2030 |
21 | Product installation rate by OEM, 2023 |
22 | Incline/Decline in Average B-2-B selling price in past 5 years |
23 | Competition from substitute products |
24 | Gross margin and average profitability of suppliers |
25 | New product development in past 12 months |
26 | M&A in past 12 months |
27 | Growth strategy of leading players |
28 | Market share of vendors, 2023 |
29 | Company Profiles |
30 | Unmet needs and opportunity for new suppliers |
31 | Conclusion |
32 | Appendix |