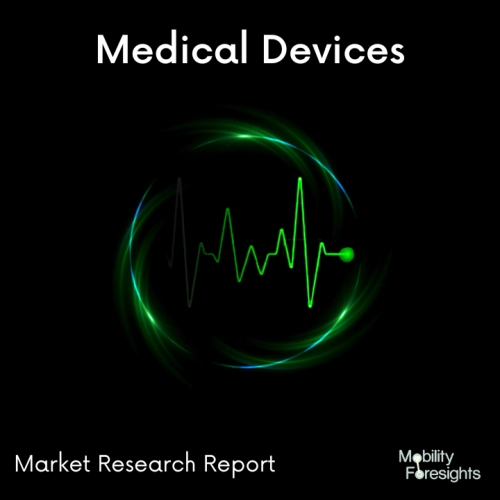
- Get in Touch with Us
Last Updated: Apr 25, 2025 | Study Period: 2024-2030
A form of shape memory alloy used in medical equipment is nitinol. The name "Nickel Titanium Naval Ordnance Laboratories" refers to the company that was responsible for discovering the alloy's special characteristics. As a result of being bent, twisted, or otherwise distorted, the nickel and titanium alloy known as nitinol can regain its previous shape.
Nitinol is ideally suited for application in medical devices because of this characteristic. It may be utilised to construct flexible components that, when subjected to heat or other stimuli, will take on their original shape. Self-expanding grafts, bins, filters, connection supporting frameworks, and other items are only a few examples of the many uses for nitinol.
The super-versatility and thermal shape memory of nitinol compounds are what make them most famous. Nitinol, a compound of titanium and nickel, is used to make medical equipment. Nitinol-based guidewires and stents have improved operative outcomes.
The Nitinol Medical Devices accounted for $XX Billion in 2023 and is anticipated to reach $XX Billion by 2030, registering a CAGR of XX% from 2024 to 2030.
The EasyFuse Dynamic Compression System, made of the nickel-titanium alloy metal Nitinol, was introduced by Stryker Corporation. Reduced surgical complexity and operating room waste are the material's goals, as well as its strength and form recovery. The maker of medical equipment and parts constructed of the shape-memory alloy nitinol, Endosmart Gesellschaft für Medizintechnik GmbH (Endosmart), with headquarters in Germany, was bought by Alleima.
The product line comprises surgical instruments, breast cancer tumour markers, and baskets and snares for removing kidney stones. To offer a better digital and self-serve client experience, Cook Medical recently announced the establishment of a new customer portal. The DIRECTSENSE Technology, a device for observing the impact of radiofrequency (RF) energy delivery during cardiac ablation procedures, is officially launched in the United States, according to Boston Scientific.
In Mexicali, Mexico, Matthey's Medical Device Components division launched a brand-new nitinol factory.It can produce twice as much nitinol sheet and tubing in this facility's 40,000 square feet of manufacturing space than it could in the business's former Californian location in San Jose. Only one low-cost country in the world produces nitinol sheet and tube, and that is the recently built plant in Mexicali.
According to them, the new facility will provide its clients with more capacity for product launches, reduced costs, improved quality assurance, and predictable deliveries with shorter lead times. This is a brand-new and intriguing chapter after 35 years of nitinol expertise. To help customers achieve their objectives, the staff works hard to build trusting, mutually beneficial relationships with them.
They can reduce costs and produce goods of the highest calibre with the help of new facilities. They put a priority on quality, on-time delivery, capacity management, and reasonable pricing, and this benefits all of their customers. Nitinol shape setting is experiencing enormous developments in the medical device business. When subjected to a specific temperature, nitinol demonstrates superelasticity with the capacity to recall and return to a specific shape after deformation.
These "room temperature" superelastic grades are more frequently seen in medical devices, with transformation temperatures for superelastic grades ranging from -20°C (-4°F) to 22°C [71.6°F]. Nitinol's use in the manufacturing of medical devices has increased significantly over the previous ten years, according to Custom Wire Technologies (CWT). With over 20 years of industry experience, CWT is a manufacturer of medical wire solutions that offers customers custom-made medical components made from a variety of approved materials, including as nitinol and stainless steel.
Nitinol was first utilised by CWT in a specially designed suture threader. Because of the alloy's shape memory capabilities, it was able to revert to its former shape after passing through the device's tiny hole, making it easier for medical practitioners to load the suture through the device. For amounts totaling more than 18 million feet of a single diameter, they have open orders with the raw material supplier. About 200,000 feet are used each week by one of their product lines.
The material has grown on them. Core wire grinding and catheter reinforcement coils both benefit greatly from their use. With CWT setting hundreds of coils per day and thousands of coils per week, form set nitinol catheter reinforcement coils are the most in demand in terms of production. They have a number of suture threader product lines that call for various shaft shapes. Tools made specifically for the shapes are produced in-house. Due to its flexibility and abrasiveness, nitinol can be difficult to work with, but the CWT team has amassed enormous skill in shape setting over the years.
The market is flooded with products that will keep stainless steel useful. Costs, production processes, or governmental permissions may all be factors in this. Not every producer has knowledge about nitinol.There may be new products on the market made of nitinol, but stainless steel will always be supported. All essential alloys will continue to be supported by CWT.The Medical Device Components division of Johnson Matthey launched a brand-new nitinol factory in Mexicali, Mexico.
It can produce twice as much nitinol sheet and tubing in this facility's 40,000 square feet of manufacturing space than it could in the business's former Californian location in San Jose. Only one low-cost country in the world produces nitinol sheet and tube, and that is the recently built plant in Mexicali. The new facility will provide its clients with greater device launch capability, reduced costs, improved quality assurance, and trustworthy deliveries with shorter lead times.
This is a brand-new and intriguing chapter after 35 years of nitinol expertise. To assist customers in achieving their objectives, the team works hard to build trusting relationships that are based on mutual respect. They'll be able to supply high-quality goods while reducing prices thanks to these new facilities. Every client will gain from their emphasis on quality, punctual delivery, capacity management, and affordable pricing.
Nitinol shape setting is experiencing enormous development in the medical device business. Nitinol's use in medicine has increased dramatically in recent years, mostly as a result of its "memory" qualities and ability to withstand far greater strain than stainless steel. Nitinol is both kink resistant and flexible enough to alter shape as needed, making it ideal for surgeons who must manoeuvre in highly constrictive spaces.
Nitinol is a member of an alloy family made up of nickel and titanium. It exhibits great biocompatibility while also being extremely corrosion resistant. When subjected to a specific temperature, nitinol demonstrates superelasticity with the capacity to recall and return to a specific shape after deformation.
These "room temperature" superelastic grades are more frequently seen in medical devices, with transformation temperatures for superelastic grades ranging from -20°C (-4°F) to 22°C [71.6°F]. Nitinol utilisation in the manufacturing of medical devices has increased, according to Custom Wire Technologies (CWT).
With over 20 years of industry experience, CWT is a manufacturer of medical wire solutions that offers customers custom-made medical components made from a variety of approved materials, including as nitinol and stainless steel. Nitinol was first utilised by CWT in a specially designed suture threader, where its shape memory properties meant that the alloy would revert to its original shape after passing through the instrument's tiny hole, making it easier for medical personnel to load the suture through the device.
CWT has seen a dramatic growth in the use of nitinol, according to Jim Boldig, director of sales and engineering. More than 18 million feet of a single diameter are covered by open orders established with their raw material supplier. They use about 200,000 feet each week for one of their product lines. For grinding core wires and catheter reinforcement coils, it performs remarkably well.
There are numerous products on the market that will maintain stainless steel's usefulness. Costs, manufacturing processes, or government regulations could all be factors in this. Many producers lack nitinol-related expertise.There will always be a need to support stainless, even if new devices come to market with nitinol.
Celularity Inc., a clinical-stage biotechnology business, and Arthrex Inc., a world pioneer in minimally invasive orthopaedic technology, announced they have formed an exclusive agreement to distribute and market Celularity's biomaterial products for orthopaedic surgery and sports medicine.
Both firms are developing novel cell treatments and biomaterial products derived from the postpartum human placenta to treat cancer, infectious, and degenerative illnesses.
Company | Product | Year | Description |
Stryker Corporation | EasyFuse Dynamic Compression System | 2022 | EasyFuse Dynamic Compression System. Created using nitinol, a nickel titanium alloy metal well known for its strength and shape recovery |
Alleima | memory alloy nitinol | 2022 | The product used for kidney stone retrieval baskets and snares, and breast cancer tumor markers. |
Sl no | Topic |
1 | Market Segmentation |
2 | Scope of the report |
3 | Abbreviations |
4 | Research Methodology |
5 | Executive Summary |
6 | Introduction |
7 | Insights from Industry stakeholders |
8 | Cost breakdown of Product by sub-components and average profit margin |
9 | Disruptive innovation in the Industry |
10 | Technology trends in the Industry |
11 | Consumer trends in the industry |
12 | Recent Production Milestones |
13 | Component Manufacturing in US, EU and China |
14 | COVID-19 impact on overall market |
15 | COVID-19 impact on Production of components |
16 | COVID-19 impact on Point of sale |
17 | Market Segmentation, Dynamics and Forecast by Geography, 2024-2030 |
18 | Market Segmentation, Dynamics and Forecast by Product Type, 2024-2030 |
19 | Market Segmentation, Dynamics and Forecast by Application, 2024-2030 |
20 | Market Segmentation, Dynamics and Forecast by End use, 2024-2030 |
21 | Product installation rate by OEM, 2023 |
22 | Incline/Decline in Average B-2-B selling price in past 5 years |
23 | Competition from substitute products |
24 | Gross margin and average profitability of suppliers |
25 | New product development in past 12 months |
26 | M&A in past 12 months |
27 | Growth strategy of leading players |
28 | Market share of vendors, 2023 |
29 | Company Profiles |
30 | Unmet needs and opportunity for new suppliers |
31 | Conclusion |
32 | Appendix |