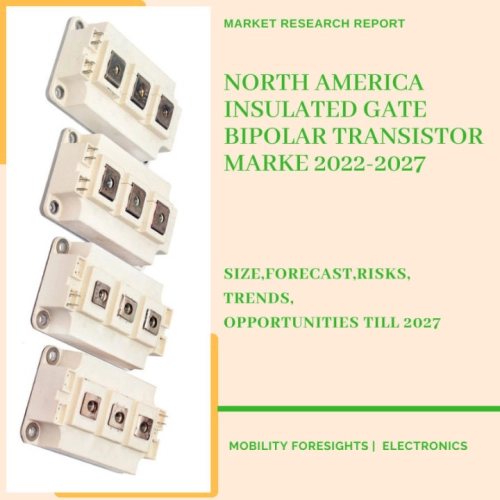
- Get in Touch with Us
Last Updated: Apr 25, 2025 | Study Period: 2022-2027
IGBTs are becoming more popular due to lower switching losses and increased reliability, as well as higher efficiency and better thermal capacity.
The growing attention and investment in R&D on IGBT chip and modules optimizations to conserve power, enhance chip compactness, thermal resistance, and efficiency would only further enhance the IGBT power semiconductor industry. IGBTs are available as single devices or as modules.
Motor controllers, converters, power supply units (UPS), electric and hybrid e - mobility (EV/HEV), control equipment, electronic goods, and diagnostic implants are all examples of IGBT uses.
S No | Overview of Development | Development Detailing | Region of Development | Possible Future Outcomes |
1 | Fuji Electric Announces New Launch of 7th Generation X Series IGBT Module HPnC | It has begun mass manufacturing of its HPnC for the railway market, which is equipped with a 7th-generation X Series IGBT module. | North America | This would enhance better Technological Controls |
2 | Bitrode launches IGBT lead-acid formation charger in North America | Charge SLI batteries (flooded and VRLA/AGM), motive power batteries, and industrial cells with the HD-CR/CD. | North America | This would enhance better Technological Controls |
3 | Mornsun expands North America distribution | It has expanded its distribution of IGBT modules in the market. | North America | This would enhance better Technological Controls |
4 | Hitachi trains pass DfT tests, Siemens to install IGBT for Indian Railways | Hitachi's new intercity trains have passed the UK Department for Transport's digital technology integration tests. | North America | This would enhance better Technological Controls |
The automotive industry is increasing toward electrification of powertrains in electric and hybrid cars (EV/HEV), driven by carbon pollution regulations, whereby switching sequence inefficiencies are greatly reduced, having a significant effect upon overall effectiveness.
Electric vehicle sales in Europe, North America, and China are opening up new opportunities for IGBTs to support infrastructure and manufacture electric vehicles. As a result, IGBT's market position has been enhanced. The key element impacting market growth is the dependability of IGBT modules in comparison to other technologies.
Hitachi Energy is a leading mobiliser of the microcontrollers in the market. The latest integration has been the Mono, double / phase-leg, chopping IGBT, and double diode modules from 1700 to 6500 volts.
Low losses, soft-switching efficiency, as well as a record-breaking Safe Working Region are all features of the high-power HiPak IGBT circuits (SOA).
The new 62Pak and LoPak fast changing medium-power IGBT components have the lowest leakage currents, operate at full 175°C with full squares SOA, and come in a full package for easy replacement.
ABB is part of the component manufacture trending companies in the current industry. The frequency of the outside connection interface determines the heat transfer from the endpoints to the busbar. This temperature is set to 105°C by default (the typical bus-bar thermal maximum).
This frequency is obviously influenced by bus-bar design characteristics including cross-section (self-heating), bus-bar refrigeration, and weather conditions. It is therefore strongly advised to test this hypothesis using measurements.
Sl no | Topic |
1 | Market Segmentation |
2 | Scope of the report |
3 | Abbreviations |
4 | Research Methodology |
5 | Executive Summary |
6 | Introduction |
7 | Insights from Industry stakeholders |
8 | Cost breakdown of Product by sub-components and average profit margin |
9 | Disruptive innovation in the Industry |
10 | Technology trends in the Industry |
11 | Consumer trends in the industry |
12 | Recent Production Milestones |
13 | Component Manufacturing in US, EU and China |
14 | COVID-19 impact on overall market |
15 | COVID-19 impact on Production of components |
16 | COVID-19 impact on Point of sale |
17 | Market Segmentation, Dynamics and Forecast by Geography, 2022-2027 |
18 | Market Segmentation, Dynamics and Forecast by Product Type, 2022-2027 |
19 | Market Segmentation, Dynamics and Forecast by Application, 2022-2027 |
20 | Market Segmentation, Dynamics and Forecast by End use, 2022-2027 |
21 | Product installation rate by OEM, 2022 |
22 | Incline/Decline in Average B-2-B selling price in past 5 years |
23 | Competition from substitute products |
24 | Gross margin and average profitability of suppliers |
25 | New product development in past 12 months |
26 | M&A in past 12 months |
27 | Growth strategy of leading players |
28 | Market share of vendors, 2022 |
29 | Company Profiles |
30 | Unmet needs and opportunity for new suppliers |
31 | Conclusion |
32 | Appendix |