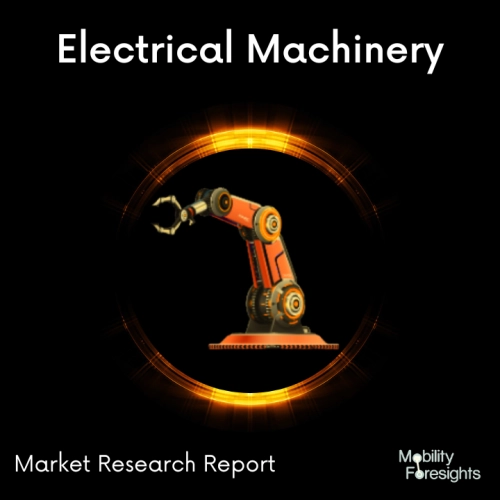
- Get in Touch with Us
Last Updated: Apr 25, 2025 | Study Period: 2023-2030
The quest for energy resources has been a driving force behind human progress for centuries, and oil and gas remain vital sources of power for the modern world. Unlocking these valuable resources requires the mastery of advanced drilling technologies, with drill bits playing a pivotal role in the extraction process.
Over the years, drill bit designs and technologies have evolved significantly to meet the increasing demands of the oil and gas industry.
Historical Evolution:
The art of drilling for oil and gas dates back to ancient times when hand-powered tools were used to extract liquid resources from the earth. However, it was not until the 19th century that technological advancements led to the development of the first mechanically-driven rotary drilling rigs. These early drilling methods involved the use of simple, fixed cutter bits that chipped away at rock formations.
The breakthrough moment for drill bit technology came with the introduction of roller cone bits in the late 19th century. These bits featured rotating cones with hardened teeth, revolutionising drilling operations by providing increased drilling efficiency and reliability. Subsequent innovations led to the creation of diamond bits, polycrystalline diamond compact (PDC) bits, and other advanced designs, each offering unique advantages in specific drilling environments.
Function and Components of Drill Bits:
Drill bits are the primary tools used to bore through the various rock formations encountered during oil and gas drilling. They are designed to create a wellbore, which allows for the extraction of hydrocarbons from underground reservoirs. The drilling process involves the rotation of the drill bit while applying downward force, enabling the cutting structures on the bit to grind, shear, or scrape away the rock formations.
Drill bits consist of several key components that work in harmony to facilitate efficient drilling. These include the bit body, cutting structure, and the bit's connection to the drilling string. The bit body, typically made of steel, provides the necessary strength and stability to withstand the extreme conditions encountered during drilling. The cutting structure, located at the bottom of the bit, is composed of different types of cutting elements, such as diamonds or tungsten carbide inserts, which vary depending on the specific drilling requirements.
Types of Drill Bits:
Advancements in Drill Bit Technology:
Since their humble beginnings, oil and gas drill bits have advanced dramatically yet gracefully, making it possible to extract hydrocarbon resources from the Earth's interior.
Drill bit technology's relentless quest of innovation has resulted in the creation of ever-more complex designs, enhancing drilling effectiveness, durability, and overall performance.
Drill bits will remain crucial tools in the oil and gas industry's quest to push the limits of exploration and production, paving the way for a future powered by sustainable energy.
The Global Oil and Gas Drill Bit market accounted for $XX Billion in 2022 and is anticipated to reach $XX Billion by 2030, registering a CAGR of XX% from 2023 to 2030.
In order to achieve improved performance and higher dependability in today's high-energy drilling systems, which are distinguished by extremely high weight-on-bit and drilling torque, Halliburton announced the launching of GeoTech HETM, a durable drill bit with novel features and materials.
Drilling practices and technology have advanced recently, allowing operators to considerably improve energy and drilling speed to cut expenses. Drill bits therefore encounter greater stresses that test conventional design theory and materials and greatly raise the possibility of damage to the bit body material and API connection.
High energy (HE) GeoTech pieces are designed to operate under these demanding circumstances. The steel and matrix platforms each have distinctive design geometries and features that are geared towards high-energy systems.
The new matrix body combines various components, and the new steel body is made of a sophisticated alloy. Both are designed to have greater strength and endurance under heavy axial and torsional loads.
Each bit is designed for a particular application using Halliburton's Design at the Customer Interface Process (DATCI), which uses a global network of technical specialists to interact directly with clients. This method expedites development and does away with the time-consuming and expensive trial and error method.
Sl no | Topic |
1 | Market Segmentation |
2 | Scope of the report |
3 | Abbreviations |
4 | Research Methodology |
5 | Executive Summary |
6 | Introduction |
7 | Insights from Industry stakeholders |
8 | Cost breakdown of Product by sub-components and average profit margin |
9 | Disruptive innovation in the Industry |
10 | Technology trends in the Industry |
11 | Consumer trends in the industry |
12 | Recent Production Milestones |
13 | Component Manufacturing in US, EU and China |
14 | COVID-19 impact on overall market |
15 | COVID-19 impact on Production of components |
16 | COVID-19 impact on Point of sale |
17 | Market Segmentation, Dynamics and Forecast by Geography, 2023-2030 |
18 | Market Segmentation, Dynamics and Forecast by Product Type, 2023-2030 |
19 | Market Segmentation, Dynamics and Forecast by Application, 2023-2030 |
20 | Market Segmentation, Dynamics and Forecast by End use, 2023-2030 |
21 | Product installation rate by OEM, 2023 |
22 | Incline/Decline in Average B-2-B selling price in past 5 years |
23 | Competition from substitute products |
24 | Gross margin and average profitability of suppliers |
25 | New product development in past 12 months |
26 | M&A in past 12 months |
27 | Growth strategy of leading players |
28 | Market share of vendors, 2023 |
29 | Company Profiles |
30 | Unmet needs and opportunity for new suppliers |
31 | Conclusion |
32 | Appendix |