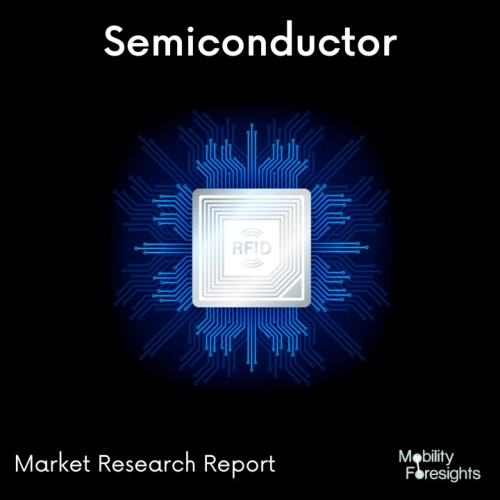
- Get in Touch with Us
Last Updated: Apr 25, 2025 | Study Period: 2024-2030
An optical comparator, also known as a profile projector, is a tool that uses the principles of optics to analyse produced parts. It is frequently referred to as merely a comparator in context. In a comparator, a part's magnified silhouette is displayed onto the screen, and its dimensions and geometry are measured in comparison to predetermined standards.
It is a valuable tool for the quality control inspection team in a small components machine shop or manufacturing line. There are various methods for measuring. The simplest method is where the observer may measure as if a clear ruler were set over the image thanks to graduations on the screen projected over the silhouette.
Another method involves moving the stage on which the part is mounted. A digital readout then shows how far the stage has to move to align each point on the silhouette with the reticle at the screen's center.
The most cutting-edge techniques also use software to analyze the image and produce measurements. The first two techniques are the most widely used; the third is more recent and less popular, although their uptake is continuing in the digital era.
The profile projector is frequently used to compare the measured contour model and for complex-shape stampings, gears, cams, and threads.
The profile projector is therefore frequently used in the production of precision machinery, especially in the fields of aviation, aerospace, watches, clocks, electronics, instruments, research institutes, and detection metering stations at all levels, among others.
On the built-in projection screen, the projector enlarges the specimen's profile for viewing. In order to match the screen's X-Y axis with a straight edge of the machined component for inspection or measurement, this screen often has a grid that can be rotated 360 degrees.
For more ease in calculating linear measures, this projection screen shows the specimen's profile and is magnified.
The Global Optical Comparator market accounted for $XX Billion in 2023 and is anticipated to reach $XX Billion by 2030, registering a CAGR of XX% from 2024 to 2030.
The MODEL 400 BENCH, created by Metrologic Instrument, uses the best components and cutting-edge technology. Performance, capacity, strength, and a longer useful life are all guaranteed as a result. features consist of exceptional performance, greater durability and unsurpassed power. It is applicable to the production of plastic Metal Production.
Analysis of Cracks and Failure Other information Mountable for a large stage Images with Adjustable Base Feet Erect Lenses for Projections on a Turret Swiveling screen with built-in protractor 360 degrees Several screen sizes are available Zooming Condenser Lens with Four Steps Specifications: Maximum Capacity for Load18 kilograms power supply110 VAC and 220 VAC are both 50/60 Hz.
Lenses Software: 5 X, 10 X (Standard), 20 X, 25 X, 50 X, 100 X, and 200 X Compatible with CAD Transfer and Metrologic 2D Similar Specimen Height limit: 100 mm Standard screen size is 400 mm; customization is available upon request.
Accuracy in surface illumination of 0.15% and contour illumination of 0.1% Linear Encoders Optional Digital Read-Out Optional Motorized Traverse Options for Resolution 0.001 mm, 0.005 mm, and 0.0005 mm.
Notre Dame Opens Engineering Innovation Hub. The University of Notre Dame has launched an experiential learning and advanced manufacturing facility that, according to the university, will enable increased cooperation, fabrication, robotics, and modelling. Notre Dame's industry Labs include the 10,000-square-foot Engineering Innovation Hub.
According to Notre Dame, the EIH will also function as a research fabrication and testing facility, as well as a resource for local manufacturing industry partners and startups.
It is located on the first floor of the Cushing-Fitzpatrick Halls of Engineering and is equipped with fabrication and machining equipment, sophisticated manufacturing stations, 3D printing stations, and computing resources.
This extraordinary facility will aid in the preparation of future engineers who are not only technical specialists, but also people who use creativity and innovation throughout their careers and to assist a world in need.
Notre Dame's Engineering Innovation Hub (EIH) is a one-of-a-kind learning and innovation environment on the first floor of Cushing-Fitzpatrick Halls of Engineering, providing tools for collaboration, fabrication, automation, robotics, and modelling to students, faculty, and industry partners.
The EIH combines specialized collaborative space with cutting-edge technology and experience in areas such as advanced manufacturing, additive manufacturing (3D printing), metrology and computer resources, and fabrication and machining technologies.
The EIH is part of Notre Dame's increasing ecosystem of experiential learning spaces that fosters innovation and the exchange of best practices among students, faculty, and industry partners. The EIH is happy to provide a regional resource for developing creative product solutions for existing businesses as well as fresh start-ups.
North America
The North American market, particularly the USA, will be one of the prime markets for (Optical Comparator Market) due to the nature of industrial automation in the region, high consumer spending compared to other regions, and the growth of various industries, mainly AI, along with constant technological advancements. The GDP of the USA is one of the largest in the world, and it is home to various industries such as Pharmaceuticals, Aerospace, and Technology. The average consumer spending in the region was $72K in 2023, and this is set to increase over the forecast period. Industries are focused on industrial automation and increasing efficiency in the region. This will be facilitated by the growth in IoT and AI across the board. Due to tensions in geopolitics, much manufacturing is set to shift towards the USA and Mexico, away from China. This shift will include industries such as semiconductors and automotive.
Europe
The European market, particularly Western Europe, is another prime market for (Optical Comparator Market) due to the strong economic conditions in the region, bolstered by robust systems that support sustained growth. This includes research and development of new technologies, constant innovation, and developments across various industries that promote regional growth. Investments are being made to develop and improve existing infrastructure, enabling various industries to thrive. In Western Europe, the margins for (Optical Comparator Market) are higher than in other parts of the world due to regional supply and demand dynamics. Average consumer spending in the region was lower than in the USA in 2023, but it is expected to increase over the forecast period.
Eastern Europe is anticipated to experience a higher growth rate compared to Western Europe, as significant shifts in manufacturing and development are taking place in countries like Poland and Hungary. However, the Russia-Ukraine war is currently disrupting growth in this region, with the lack of an immediate resolution negatively impacting growth and creating instability in neighboring areas. Despite these challenges, technological hubs are emerging in Eastern Europe, driven by lower labor costs and a strong supply of technological capabilities compared to Western Europe.
There is a significant boom in manufacturing within Europe, especially in the semiconductor industry, which is expected to influence other industries. Major improvements in the development of sectors such as renewable energy, industrial automation, automotive manufacturing, battery manufacturing and recycling, and AI are poised to promote the growth of (Optical Comparator Market) in the region.
Asia
Asia will continue to be the global manufacturing hub for (Optical Comparator Market ) over the forecast period with China dominating the manufacturing. However, there will be a shift in manufacturing towards other Asian countries such as India and Vietnam. The technological developments will come from China, Japan, South Korea, and India for the region. There is a trend to improve the efficiency as well as the quality of goods and services to keep up with the standards that are present internationally as well as win the fight in terms of pricing in this region. The demand in this region will also be driven by infrastructural developments that will take place over the forecast period to improve the output for various industries in different countries.
There will be higher growth in the Middle East as investments fall into place to improve their standing in various industries away from petroleum. Plans such as Saudi Arabia Vision 2030, Qatar Vision 2030, and Abu Dhabi 2030 will cause developments across multiple industries in the region. There is a focus on improving the manufacturing sector as well as the knowledge-based services to cater to the needs of the region and the rest of the world. Due to the shifting nature of fossil fuels, the region will be ready with multiple other revenue sources by the time comes, though fossil fuels are not going away any time soon.
Africa
Africa is expected to see the largest growth in (Optical Comparator Market ) over the forecast period, as the region prepares to advance across multiple fronts. This growth aligns with the surge of investments targeting key sectors such as agriculture, mining, financial services, manufacturing, logistics, automotive, and healthcare. These investments are poised to stimulate overall regional growth, creating ripple effects across other industries as consumer spending increases, access to products improves, and product offerings expand. This development is supported by both established companies and startups in the region, with assistance from various charitable organizations. Additionally, the presence of a young workforce will address various existing regional challenges. There has been an improvement in political stability, which has attracted and will continue to attract more foreign investments. Initiatives like the African Continental Free Trade Area (AfCFTA) are set to facilitate the easier movement of goods and services within the region, further enhancing the economic landscape.
RoW
Latin America and the Oceania region will showcase growth over the forecast period in (Optical Comparator Market). In Latin America, the focus in the forecast period will be to improve their manufacturing capabilities which is supported by foreign investments in the region. This will be across industries mainly automotive and medical devices. There will also be an increase in mining activities over the forecast period in this region. The area is ripe for industrial automation to enable improvements in manufacturing across different industries and efficiency improvements. This will lead to growth of other industries in the region.
Margin Comparison (Highest to lowest) | Region | Remarks |
1 | Europe | The supply chain demands and the purchasing power in the region enable suppliers to extradite a larger margin from this region than other regions. This is for both locally manufactured as well as imported goods and services in the region. |
2 | North America | Due to the high spending power in this region, the margins are higher compared to the rest of the world, but they are lower than Europe as there is higher competition in this region. All the suppliers of goods and services target USA as a main market thereby decreasing their margins compared to Europe |
3 | Asia | Lower purchasing power, coupled with higher accessibility of services in this regions doesnât enable suppliers to charge a high margin making it lower than Europe and North America. The quality of goods and services are also affected due to this aspect in the region |
4 | Africa and ROW | The margins are the lowest in this region, except for Australia and New Zealand as the countries in this region donât have much spending power and a large portion of the products and services from this area is exported to other parts of the world |
USAâ $210 billion is allocated to federal R&D with main focus on health research, clean energy, semiconductor manufacturing, sustainable textiles, clean energy, and advanced manufacturing. Investments by private players are mainly focused on technological development including 5G infrastructure and AI in the region.
Europeâ EIC is investing â¬1 billion to innovative companies in sectors like AI, biotechnology, and semiconductors. There is also a focus on developing the ecosystem in the continent as well as improving the infrastructure for developing industries such as electric vehicles and sustainable materials. Private players are targeting data centers, AI, battery plants, and high end technological R&D investments.
Asiaâ There are investments to tackle a range of scientific and technological advancements in this region mainly coming in from China, India, South Korea, and Japan. This will include artificial intelligence, 5G, cloud computing, pharmaceutical, local manufacturing, and financial technologies. Many countries are aiming to be digital hubs including Saudi Arabia.
Africaâ Investments in the region are focused on improving the technological capabilities in the region along with socio-economic development and growth. Private participants of investments in this region is venture capital dominated who are targeting the various growth elements of the region as social stability improves. The major industries are fintech, easier lending, and manufacturing.
Latin America â The focus in the region is for fintech, e-commerce, and mobility sectors. There are also investments in improving manufacturing in the region. Local investments is focused on improving the healthcare, and transportation infrastructure in the region. The region is attracting foreign investments to improve their ability to utilize the natural resources present in the region.
Rest of the Worldâ The investments in this region are focused on clean energy, green metals, and sustainable materials. Funds in Australia are focused on solar energy and battery technologies, along with high end futuristic areas such as quantum computing. The main countries of private investment in ROW will be Australia, Canada, and New Zealand.
Sl no | Topic |
1 | Market Segmentation |
2 | Scope of the report |
3 | Abbreviations |
4 | Research Methodology |
5 | Executive Summary |
6 | Introduction |
7 | Insights from Industry stakeholders |
8 | Cost breakdown of Product by sub-components and average profit margin |
9 | Disruptive innovation in the Industry |
10 | Technology trends in the Industry |
11 | Consumer trends in the industry |
12 | Recent Production Milestones |
13 | Component Manufacturing in US, EU and China |
14 | COVID-19 impact on overall market |
15 | COVID-19 impact on Production of components |
16 | COVID-19 impact on Point of sale |
17 | Market Segmentation, Dynamics and Forecast by Geography, 2024-2030 |
18 | Market Segmentation, Dynamics and Forecast by Product Type, 2024-2030 |
19 | Market Segmentation, Dynamics and Forecast by Application, 2024-2030 |
20 | Market Segmentation, Dynamics and Forecast by End use, 2024-2030 |
21 | Product installation rate by OEM, 2023 |
22 | Incline/Decline in Average B-2-B selling price in past 5 years |
23 | Competition from substitute products |
24 | Gross margin and average profitability of suppliers |
25 | New product development in past 12 months |
26 | M&A in past 12 months |
27 | Growth strategy of leading players |
28 | Market share of vendors, 2023 |
29 | Company Profiles |
30 | Unmet needs and opportunity for new suppliers |
31 | Conclusion |
32 | Appendix |