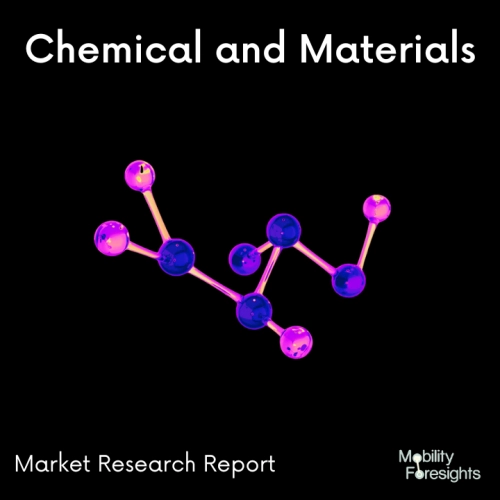
- Get in Touch with Us
Last Updated: Apr 25, 2025 | Study Period: 2023-2030
A passivating coating is a type of protective layer that is put to the surface of a material to prevent corrosion or other forms of chemical degradation The process of passive surface layer formation on a metal, known as passivation, results in a thin, imperceptible film that shields the metal from corrosion.
The metal is protected from corrosive elements like oxygen, water, and other chemicals by the passivating coating, which acts as a barrier between the metal and its surroundings.
Metals, ceramics, and polymers are just a few of the materials that can receive passivating coatings. They are commonly employed in industrial applications, such as in the fabrication of chemical processing equipment, aerospace components, and medical devices.
There are several different types of passivating coatings, including oxide coatings, nitride coatings, and polymer coatings. The material being protected, the type of corrosion being avoided, and the environment to which the item will be exposed will all influence the coating choice.
Global passivating coating market accounted for $XX Billion in 2022 and is anticipated to reach $XX Billion by 2030, registering a CAGR of XX% from 2023 to 2030.
They are happy to introduce Drizzling, an original method for using chrome-free passivation materials on all metals, from ALIT Technologies.
ALIT Technologies is proud to announce the release of the Drizzling dosing and application system. ALIT Technologies is a leading developer of equipment and solutions for metal surface treatment.
The treatment of metal surfaces promotes good long-term durability and offers defence against corrosion and oxidation. Various surface treatment procedures exist with this objective in mind.
Coating, which is merely the final (but not least) phase of a chemical process that involves numerous intermediate stages in which parts are degreased, pickled, and passivated, is undoubtedly one of the most significant and widely used. The Drizzling method can make a difference in this final stage.
Drizzling is the process of applying a passivating chemical product directly to the surface of metals using a complete dosing system that can automatically manage the mixing of demineralized water from a feed tank with the correct amount of the product.
The system can uniformly create and spread a fine and light mist of passivating solution that completely envelops the product, even in 7-meter vertical lines for aluminium profiles, thanks to the employment of specialised atomizing nozzles and compressed air.
Sl no | Topic |
1 | Market Segmentation |
2 | Scope of the report |
3 | Abbreviations |
4 | Research Methodology |
5 | Executive Summary |
6 | Introduction |
7 | Insights from Industry stakeholders |
8 | Cost breakdown of Product by sub-components and average profit margin |
9 | Disruptive innovation in the Industry |
10 | Technology trends in the Industry |
11 | Consumer trends in the industry |
12 | Recent Production Milestones |
13 | Component Manufacturing in US, EU and China |
14 | COVID-19 impact on overall market |
15 | COVID-19 impact on Production of components |
16 | COVID-19 impact on Point of sale |
17 | Market Segmentation, Dynamics and Forecast by Geography, 2023-2030 |
18 | Market Segmentation, Dynamics and Forecast by Product Type, 2023-2030 |
19 | Market Segmentation, Dynamics and Forecast by Application, 2023-2030 |
20 | Market Segmentation, Dynamics and Forecast by End use, 2023-2030 |
21 | Product installation rate by OEM, 2023 |
22 | Incline/Decline in Average B-2-B selling price in past 5 years |
23 | Competition from substitute products |
24 | Gross margin and average profitability of suppliers |
25 | New product development in past 12 months |
26 | M&A in past 12 months |
27 | Growth strategy of leading players |
28 | Market share of vendors, 2023 |
29 | Company Profiles |
30 | Unmet needs and opportunity for new suppliers |
31 | Conclusion |
32 | Appendix |