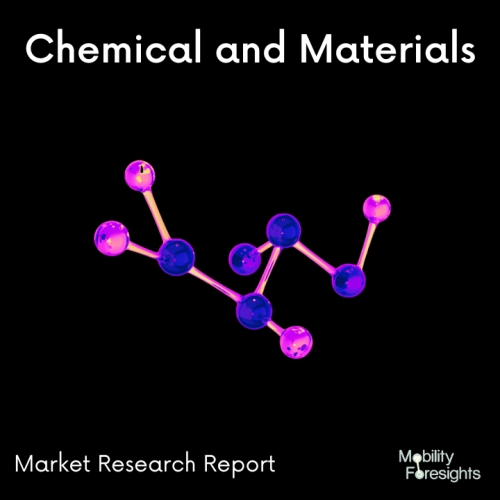
- Get in Touch with Us
Last Updated: Apr 25, 2025 | Study Period: 2024-2030
Pastes for passive components, such as inner electrode pastes and termination materials based on silver and silver-palladium, are known as thick film metallization products for passive components.
Each component paste must be carefully designed to provide enough green strength for plate transfer with machine dipping.
For different application forms, such as screen printing, dipping, or spraying, different theologies are required. Additionally, the goods must adhere to the EU directive on the restriction of hazardous substances (RoHs compliant).
All standard application machines, including plate and belt dip equipment, can employ these materials. There are other rheologies for screen printing and spray application.
To ensure optimal device performance with our metallization's, Heraeus has on-site process capabilities, including automatic machine dipping and Ni and Sn electrolytic barrel plating.
These electro-conductive pastes are utilized for the terminal electrodes of passive components for surface mounting, such as resistors, MLCCs, and inductors.
They are sintered to fit particular processes. For the fabrication of electronic boards, automation is essential. Heraeus Passive Component Pastes provide enough green strength for machine dipping and plate transfer.
Heraeus Passive Component Pastes are the best option whether you need screen printing, dipping, or spraying.
Pastes for passive components, such as inner electrode pastes and termination materials based on silver and silver-palladium, are known as thick film metallization products for passive components.
Each component paste must be carefully designed to provide enough green strength for plate transfer with machine dipping.
The Global Passive Component Pastes market accountedfor $XX Billion in 2023 and is anticipated to reach $XX Billion by 2030, registering a CAGR of XX% from 2024 to 2030.
The new SD1020 dielectric thick film paste from Heraeus Electronics, a top supplier of materials solutions for the semiconductor and electronic packaging industries, is a breakthrough in insulative technology for circuits and heaters on stainless steel used in automotive, industrial, and consumer product applications.
Known benefits of thick film heater technology, such as excellent reliability, quick cycle times, high power densities, and precise heating, are combined with design flexibility in the paste.
One of the main drawbacks with current paste technology has been its inability to address substrate problems, which leads to the printed circuit on the bowed substrate performing poorly.
Bowing results in strains within the fired film system that emerge as field failures that are unnoticed by outgoing quality checks, in addition to flatness and printing issues.
A variety of epoxy coating powders are available from CAPLINQ that were created for the electrical insulation of passive electronic components like resistors, varistors, and capacitors.
With products that range from outstanding thermal cycle materials for Class 1 rated Ceramic Capacitors to inexpensive epoxy coating powders for film wrap capacitors, CAPLINQ products helped to launch this market and are still pushing the boundaries of performance for the best materials available right now.
The majority of CAPLINQ's passive electronics products are UL-listed. For toroid's, magnetic cores, and powder cores, CAPLINQ offers a variety of epoxy coating powders.
The stability and inductance values of the toroid cores are maintained by these goods' low shrinkage and low moisture absorption coating powders. For Moly permalloy (MPP), Iron, Sen dust, and other alloy powder cores, these products are appropriate.
Sl no | Topic |
1 | Market Segmentation |
2 | Scope of the report |
3 | Abbreviations |
4 | Research Methodology |
5 | Executive Summary |
6 | Introduction |
7 | Insights from Industry stakeholders |
8 | Cost breakdown of Product by sub-components and average profit margin |
9 | Disruptive innovation in the Industry |
10 | Technology trends in the Industry |
11 | Consumer trends in the industry |
12 | Recent Production Milestones |
13 | Component Manufacturing in US, EU and China |
14 | COVID-19 impact on overall market |
15 | COVID-19 impact on Production of components |
16 | COVID-19 impact on Point of sale |
17 | Market Segmentation, Dynamics and Forecast by Geography, 2024-2030 |
18 | Market Segmentation, Dynamics and Forecast by Product Type, 2024-2030 |
19 | Market Segmentation, Dynamics and Forecast by Application, 2024-2030 |
20 | Market Segmentation, Dynamics and Forecast by End use, 2024-2030 |
21 | Product installation rate by OEM, 2023 |
22 | Incline/Decline in Average B-2-B selling price in past 5 years |
23 | Competition from substitute products |
24 | Gross margin and average profitability of suppliers |
25 | New product development in past 12 months |
26 | M&A in past 12 months |
27 | Growth strategy of leading players |
28 | Market share of vendors, 2023 |
29 | Company Profiles |
30 | Unmet needs and opportunity for new suppliers |
31 | Conclusion |
32 | Appendix |