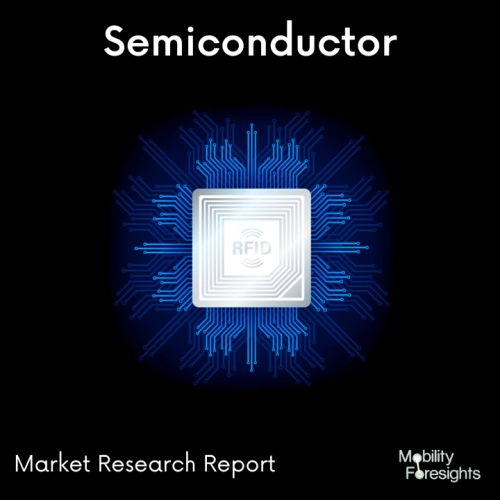
- Get in Touch with Us
Last Updated: Apr 25, 2025 | Study Period: 2024-2030
To detect the pressure of gases or liquids, a board mount pressure sensor is commonly installed on a printed circuit board (PCB).
PCB board level pressure sensors come in through-hole or surface mount products, gel-coated versions for severe applications, and numerous configurations including temperature outputs.
They are available in mV, amplified analogue, or digital outputs.
The Global PCB Mountable Pressure Sensors market accounted for $XX Billion in 2023 and is anticipated to reach $XX Billion by 2030, registering a CAGR of XX% from 2024 to 2030.
Ceramic-based, PCB-mounted pressure transducers with digital output make up the MS4515DO series. These transducers are temperature-compensated and offer a pressure range of 2 to 30 inches H20 (inH20). A total error band over the corrected range of less than 1.0%.
The most up-to-date CMOS sensor conditioning circuitry is used in the construction of these transducers to produce low-cost, high-performance digital output pressure (14bit) and temperature (11bit) transducers that are developed to adhere to the most exacting specifications from OEM clients.
The sensor uses a single source of 3.3 or 5.0Vdc and only needs one external part to function properly. The tough ceramic transducer can monitor absolute or differential pressure between 2 and 30 inches of water and is offered with side ports, top ports, and manifold installations. The 3/32" ID tubing firmly mates with the 1/8" barbed pressure ports.
Since TDK-InvenSense MEMS pressure sensors are mechanical components, package stress has an impact on them. By bending the PCB due to mounting positions, screw holes, or misalignment, the board stress is transferred to the package, which can change the pressure sensor's output or, in severe circumstances, potentially harm the MEMS structure.
For TDK-InvenSense pressure sensors, a normal PCB thickness of 1.57 mm, or 63 mils, is adequate; however, smaller PCBs, around 1 mm thick, are advised to lessen PCB stress. Use FR4 PCBs with TG at temperatures exceeding the application/process temperature. Flex PCBs may also be employed if the sensor is placed on the flat side of the PCB or if a stiffener is put below the sensor.
The MEMS capacitive technology underpinning the ICP-101xx pressure sensor series provides ultra-low noise at lowest power, enabling market-leading relative accuracy, sensor throughput, and temperature stability. The pressure sensor is able to gauge
8.5 cm, or less than the height of one stair step, is the smallest altitude difference that can be measured with an accuracy of 1 Pa in pressure changes.
The sensing element design by Honeywell International Inc. comprises of four piezoresistors on a silicon diaphragm that has been chemically etched. The diaphragm and the hidden resistors will be put under strain by a change in pressure. An electrical output is created as a result of the resistor values changing proportionally to the applied stress.
In a small package, the 24PC Series micro pressure sensors deliver dependable gauge pressure sensing capability. A specific piezoresistive micro-machined sensing element is used in the sensor's tested sensing technology. The low power, non-amplified, non-compensated Wheatstone bridge circuit architecture offers mV outputs that are naturally stable over sensing ranges of 0.5 psi to 250 psi.
Sl no | Topic |
1 | Market Segmentation |
2 | Scope of the report |
3 | Abbreviations |
4 | Research Methodology |
5 | Executive Summary |
6 | Introduction |
7 | Insights from Industry stakeholders |
8 | Cost breakdown of Product by sub-components and average profit margin |
9 | Disruptive innovation in the Industry |
10 | Technology trends in the Industry |
11 | Consumer trends in the industry |
12 | Recent Production Milestones |
13 | Component Manufacturing in US, EU and China |
14 | COVID-19 impact on overall market |
15 | COVID-19 impact on Production of components |
16 | COVID-19 impact on Point of sale |
17 | Market Segmentation, Dynamics and Forecast by Geography, 2024-2030 |
18 | Market Segmentation, Dynamics and Forecast by Product Type, 2024-2030 |
19 | Market Segmentation, Dynamics and Forecast by Application, 2024-2030 |
20 | Market Segmentation, Dynamics and Forecast by End use, 2024-2030 |
21 | Product installation rate by OEM, 2023 |
22 | Incline/Decline in Average B-2-B selling price in past 5 years |
23 | Competition from substitute products |
24 | Gross margin and average profitability of suppliers |
25 | New product development in past 12 months |
26 | M&A in past 12 months |
27 | Growth strategy of leading players |
28 | Market share of vendors, 2023 |
29 | Company Profiles |
30 | Unmet needs and opportunity for new suppliers |
31 | Conclusion |
32 | Appendix |