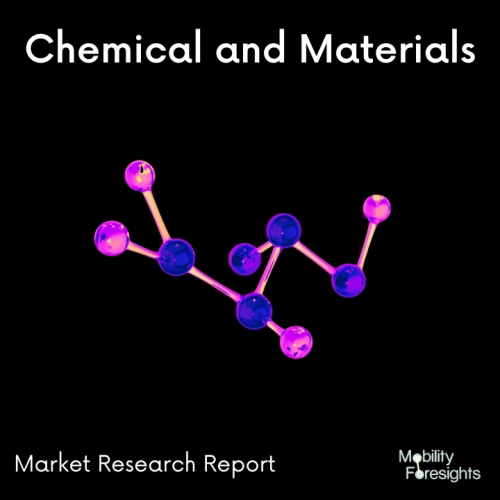
- Get in Touch with Us
Last Updated: Apr 25, 2025 | Study Period: 2024-2030
Phosphating is a process of applying a coating of phosphate to a metal substrate. This process is used to create a protective layer that increases the corrosion resistance of the metal and improves its aesthetics. The coating is also used to improve the adhesion of subsequent coatings such as paint or powder coatings.
The most common type of phosphating is zinc phosphating. In this process, a zinc phosphate coating is applied to the metal substrate using an acidic solution of zinc and phosphoric acid.
The solution is typically heated to a temperature of about 120°C for a period of time ranging from 10 minutes to several hours, depending on the desired result. This process results in a coating of zinc phosphate crystals on the surface of the metal that acts as a protective barrier against corrosion
In addition to zinc phosphating, other types of phosphating coatings are also available. Manganese and iron phosphating are commonly used in applications where a more robust and durable coating is required. These coatings are more resistant to wear and abrasion and provide better adhesion for subsequent coatings
In addition to providing protection against corrosion, phosphating coatings are also used to improve the aesthetics of the metal. The coating provides a uniform matte finish that can be used to enhance the appearance of a product.
Phosphating is a cost effective and efficient way to improve the performance and aesthetics of a metal substrate. The process can be used in a variety of applications and can be tailored to specific requirements.
The Global Phosphating coating market accounted for $XX Billion in 2023 and is anticipated to reach $XX Billion by 2030, registering a CAGR of XX% from 2024 to 2030.
In recent years, phosphating coating has become increasingly popular in the industrial coating sector. This coating is used to protect metal surfaces from corrosion, rust, and wear and tear. Phosphating coatings are also used to improve the surface adhesion of paints and primers to metal surfaces.
Phosphating coatings are made from phosphoric acid and zinc, and the process is typically done through an immersion process. This process is used to create a thin, protective coating that is easily applied and extremely durable. Phosphating coatings are also used to improve the appearance of metal surfaces, as well as to increase their resistance to abrasion and wear.
As the demand for phosphating coatings has increased, several companies have launched new products to meet the needs of the market. For example, AkzoNobel launched its new Phosguard range of phosphating coatings, designed to provide superior corrosion protection and improved adhesion. The company also offers a range of specialized phosphating coatings, such as its Phosguard E-coat, designed for use on electroplated metals.
Another company, Kynar, has launched a new line of phosphating coatings called Kynar Armor. These coatings are designed to provide superior protection from corrosion, as well as improved adhesion. They are also resistant to heat and chemicals, making them ideal for use in harsh environments.
Finally, PPG Industries has introduced its new line of phosphating coatings called PPG MaxGuard. These coatings are designed to provide superior corrosion protection, improved adhesion and superior durability. They are also resistant to UV rays and abrasion, making them ideal for use in environments where exposure to the elements is a concern.
In conclusion, phosphating coatings are becoming increasingly popular in the industrial coating sector. Several companies have launched new products to meet the needs of the market. These coatings are designed to provide superior protection against corrosion, as well as improved adhesion and durability. They are also resistant to heat and chemicals, making them ideal for use in harsh environments.
Sl no | Topic |
1 | Market Segmentation |
2 | Scope of the report |
3 | Abbreviations |
4 | Research Methodology |
5 | Executive Summary |
6 | Introduction |
7 | Insights from Industry stakeholders |
8 | Cost breakdown of Product by sub-components and average profit margin |
9 | Disruptive innovation in the Industry |
10 | Technology trends in the Industry |
11 | Consumer trends in the industry |
12 | Recent Production Milestones |
13 | Component Manufacturing in US, EU and China |
14 | COVID-19 impact on overall market |
15 | COVID-19 impact on Production of components |
16 | COVID-19 impact on Point of sale |
17 | Market Segmentation, Dynamics and Forecast by Geography, 2024-2030 |
18 | Market Segmentation, Dynamics and Forecast by Product Type, 2024-2030 |
19 | Market Segmentation, Dynamics and Forecast by Application, 2024-2030 |
20 | Market Segmentation, Dynamics and Forecast by End use, 2024-2030 |
21 | Product installation rate by OEM, 2023 |
22 | Incline/Decline in Average B-2-B selling price in past 5 years |
23 | Competition from substitute products |
24 | Gross margin and average profitability of suppliers |
25 | New product development in past 12 months |
26 | M&A in past 12 months |
27 | Growth strategy of leading players |
28 | Market share of vendors, 2023 |
29 | Company Profiles |
30 | Unmet needs and opportunity for new suppliers |
31 | Conclusion |
32 | Appendix |