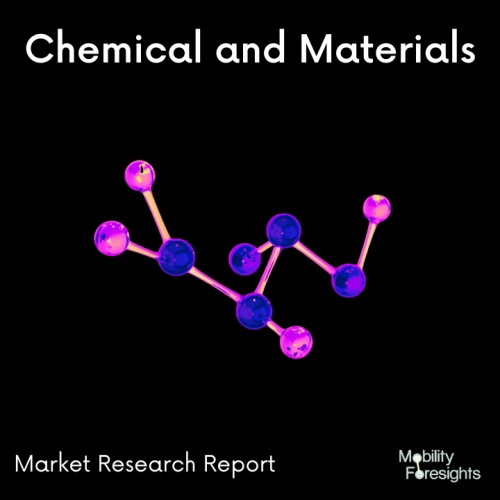
- Get in Touch with Us
Last Updated: Apr 25, 2025 | Study Period: 2024-2030
A copolymer is a polymer that is made up of two or more different monomers. The monomers can be the same or different, and they can be arranged in a variety of ways. Copolymers can have different properties than the monomers they are made from, and they can be used to create a wide range of materials.
Copolymers are often used to create materials that are stronger, tougher, or more flexible than the monomers they are made from. They can also be used to create materials that are resistant to heat, chemicals, or other environmental factors. Copolymers are used in a wide range of products, including plastics, rubbers, and fibers.
Some common examples of copolymers include:
Copolymers are an important class of materials that are used in a wide range of products. They can be designed to have a variety of properties, making them ideal for a variety of applications.
A photovoltaic copolymer is a type of polymer that can convert light into electricity. It is made up of two or more different types of monomers, which are the building blocks of polymers. The monomers are arranged in such a way that they create a material that is able to absorb light and generate an electric current.
Photovoltaic copolymers have a number of advantages over traditional photovoltaic materials, such as silicon. They are more flexible, which makes them easier to manufacture into different shapes and sizes. They are also more lightweight, which makes them ideal for use in solar panels that are installed on rooftops or in other areas where weight is a concern.
Photovoltaic copolymers are still in the early stages of development, but they have the potential to revolutionize the solar energy industry. They offer a number of advantages over traditional photovoltaic materials, and they are becoming more efficient and cost-effective all the time.
Here are some of the potential applications of photovoltaic copolymers:
Solar panels: Photovoltaic copolymers can be used to create solar panels that are more flexible and lightweight than traditional solar panels. This makes them ideal for use in a variety of applications, such as rooftop solar panels and portable solar panels.
Light-emitting diodes (LEDs): Photovoltaic copolymers can be used to create LEDs that are more efficient and cost-effective than traditional LEDs. This makes them ideal for use in a variety of applications, such as lighting, displays, and sensors.
Organic light-emitting diodes (OLEDs): Photovoltaic copolymers can be used to create OLEDs that are more efficient and cost-effective than traditional OLEDs. This makes them ideal for use in a variety of applications, such as displays, lighting, and sensors.
Displays: Photovoltaic copolymers can be used to create displays that are more flexible and lightweight than traditional displays. This makes them ideal for use in a variety of applications, such as smartphones, tablets, and laptops.
Sensors: Photovoltaic copolymers can be used to create sensors that are more sensitive and accurate than traditional sensors. This makes them ideal for use in a variety of applications, such as environmental monitoring, medical diagnostics, and industrial process control.
Batteries: Photovoltaic copolymers can be used to create batteries that are more efficient and cost-effective than traditional batteries. This makes them ideal for use in a variety of applications, such as electric vehicles, renewable energy storage, and portable electronics.
Photovoltaic copolymers are a promising new technology that has the potential to revolutionize a wide range of industries.
The Global Photovoltaic Copolymers Market accounted for $XX Billion in 2023 and is anticipated to reach $XX Billion by 2030, registering a CAGR of XX% from 2024 to 2030.
SABIC, a worldwide chemical industry leader, introduced today a breakthrough polycarbonate (PC)-based copolymer resin that is well-suited for photovoltaic (PV) connector bodies and fulfills tighter performance and regulatory criteria for upcoming 1.5Kv solar systems.
The new LNPTM EXL9334P copolymer resin has the highest comparative tracking index (CTI) level (UL PLC0) and is classified by the IEC as Material Group 1 (IEC MG 1).
It also has low-temperature ductility, good dimensional stability, strong heat resistance, durability, weather resistance, and flame retardance. This specialty resin outperforms competitors such as glass-reinforced nylon, polyphenylene ether (PPE), and ordinary PC in all critical qualities.
Customers may also benefit from the injection-molding thermoplastic's cost-effective design flexibility and processing efficiency. The appearance of 1.5 Kv PV systems is on the rise.
The move from 1.0 Kv to 1.5 Kv systems, on the other hand, is resulting in more demanding performance and safety regulations for all components. The major need is high CTI performance (UL PLC0 and IEC MG 1) in order to resist 1,500 system volts without failing. Other qualities are also important, such as ductility when exposed to extremely cold outside temperatures.
In comparison to competitor materials that fall short in dimensions and impact, the new LNP EXL9334P copolymer resin achieves exceptional performance in all critical qualities required for 1.5 Kv components.
Aside from a high CTI (UL PLC0 and IEC MG 1), the SABIC material has a low-temperature impact down to -40°C, good weatherability (UL 746C f1 designation), and strong dimensional stability. This new product also satisfies
.