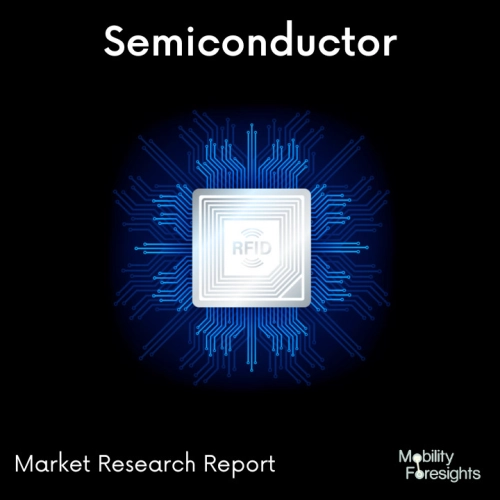
- Get in Touch with Us
Last Updated: Apr 25, 2025 | Study Period: 2024-2030
Impact drilling can be finished with a picosecond laser, guaranteeing the consistency of the hole. Picosecond lasers can drill precise holes in a variety of materials, including plastic films, semiconductors, metal films, and sapphires, in addition to circuit boards.
Targeting endogenous pigmentation and exogenous ink particles with very brief pulse durations is done with a picosecond laser (tattoos).
The Pico laser can be used to quickly remove tattoos, wrinkles, stretch marks, acne scars, pigmentation such as freckles, birthmarks, and melasma. A revolutionary type of laser known as a picosecond laser can produce pulses that last less than one nanosecond.
The Global Picosecond Laser Processing Machine market accounted for $XX Billion in 2023 and is anticipated to reach $XX Billion by 2030, registering a CAGR of XX% from 2024 to 2030.
Picosecond Laser Micromachining System by JPSA In keeping with JPSA's product philosophy of choosing the best available laser for the specific customer application, the JPSA picosecond laser platform, the IX-6168-PS, is intended to take many types of ultrafast lasers.
The workstation's slide-out servicing cart holds the laser, which is completely integrated with the system control software. Infra-red (IR), green, or UV lasers are available, along with a variety of power and pulse rate options.JPSA features a dual beam delivery option to increase tool flexibility.
A fixed-beam setup that generates a finely focused beam and makes use of the precision air-bearing stage for exact feature positioning can be employed for the highest level of precision machining.
Instead, a high-accuracy galvanometer setup with a step-and-scan capability may be selected for high-speed processing of complicated shapes. The IX-6168-PS can be quickly modified on location to meet specific requirements and is offered with both fixed beam and galvanometer scanning functionality.
By using an ultrafast laser, the pulse duration is shorter than the material's timeframe for thermal diffusion, resulting in a straight transition from solid to vapour that drastically eliminates the creation of debris and has a minimal thermal influence on the surrounding area.
This makes the technology perfect for materials that are often difficult to process and for applications where the quality of the finished product is crucial.
Sl no | Topic |
1 | Market Segmentation |
2 | Scope of the report |
3 | Abbreviations |
4 | Research Methodology |
5 | Executive Summary |
6 | Introduction |
7 | Insights from Industry stakeholders |
8 | Cost breakdown of Product by sub-components and average profit margin |
9 | Disruptive innovation in the Industry |
10 | Technology trends in the Industry |
11 | Consumer trends in the industry |
12 | Recent Production Milestones |
13 | Component Manufacturing in US, EU and China |
14 | COVID-19 impact on overall market |
15 | COVID-19 impact on Production of components |
16 | COVID-19 impact on Point of sale |
17 | Market Segmentation, Dynamics and Forecast by Geography, 2023-2030 |
18 | Market Segmentation, Dynamics and Forecast by Product Type, 2023-2030 |
19 | Market Segmentation, Dynamics and Forecast by Application, 2023-2030 |
20 | Market Segmentation, Dynamics and Forecast by End use, 2023-2030 |
21 | Product installation rate by OEM, 2023 |
22 | Incline/Decline in Average B-2-B selling price in past 5 years |
23 | Competition from substitute products |
24 | Gross margin and average profitability of suppliers |
25 | New product development in past 12 months |
26 | M&A in past 12 months |
27 | Growth strategy of leading players |
28 | Market share of vendors, 2023 |
29 | Company Profiles |
30 | Unmet needs and opportunity for new suppliers |
31 | Conclusion |
32 | Appendix |