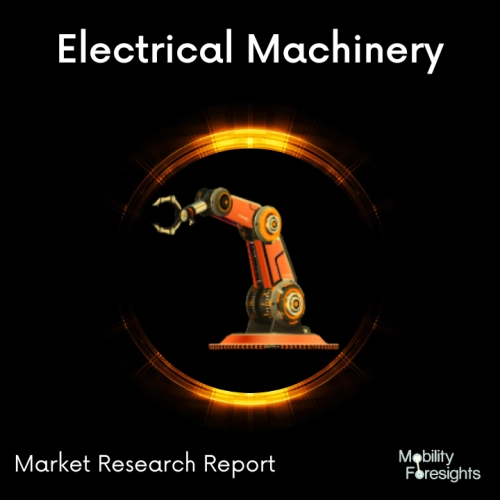
- Get in Touch with Us
Last Updated: Apr 25, 2025 | Study Period: 2024-2030
Piezo flexure actuators are utilized for force generation, fast movement, and precise positioning. Pushing against an external elastic material is the typical definition of force creation. Piezo flexure actuator with a basic motion amplifier and parallelogram flexure guidance mechanism.
Typically, flexures are constructed of titanium, steel, or aluminium. They can pay for cycles of maintenance-free service because there is no friction or wear. A stack of layers of specialised ceramic, only a few dozen micrometres thick, interspersed with electrodes, and sintered into a solid structure is the basis of piezoelectric flexure actuators.
The Global Piezo Flexure Actuators market accounted for $XX Billion in 2023 and is anticipated to reach $XX Billion by 2030, registering a CAGR of XX% from 2024 to 2030.
Development of a piezo flexure-based nano-actuator for directional sensing with atomic force microscopy at high frequencies and resolution. Nano-positioning systems are used in a variety of micro- and nanotechnology fields, including MEMS1, the manipulation of samples at the nanoscale, and lithography. The lateral movement of the probe is typically accomplished using piezo actuators mounted in a special scanner.
Modern systems regularly achieve positional accuracy of less than one angstrom, allowing the scanner to move the probe in all directions with regard to the sample.
Modern systems typically achieve sub-angstrom positioning precision, allowing the scanner to move the probe relative to the sample in all directions. 10â13 Measurements are frequently made dynamically in scanning probe microscopies to increase accuracy or access data that would not otherwise be accessible, including time-dependent variables.
The vibrating tip used in atomic force microscopy (AFM) to explore the topography and the mechanical characteristics of a given sample, frequently with atomic- or molecular-level resolution, serves as an illustration of this type of device.
Due to the scanner's inertia, inherent resonances, and heat dissipation of the piezo elements, operating a scanner at such high frequencies is anything but simple.
Sl no | Topic |
1 | Market Segmentation |
2 | Scope of the report |
3 | Abbreviations |
4 | Research Methodology |
5 | Executive Summary |
6 | Introduction |
7 | Insights from Industry stakeholders |
8 | Cost breakdown of Product by sub-components and average profit margin |
9 | Disruptive innovation in the Industry |
10 | Technology trends in the Industry |
11 | Consumer trends in the industry |
12 | Recent Production Milestones |
13 | Component Manufacturing in US, EU and China |
14 | COVID-19 impact on overall market |
15 | COVID-19 impact on Production of components |
16 | COVID-19 impact on Point of sale |
17 | Market Segmentation, Dynamics and Forecast by Geography, 2024-2030 |
18 | Market Segmentation, Dynamics and Forecast by Product Type, 2024-2030 |
19 | Market Segmentation, Dynamics and Forecast by Application, 2024-2030 |
20 | Market Segmentation, Dynamics and Forecast by End use, 2024-2030 |
21 | Product installation rate by OEM, 2023 |
22 | Incline/Decline in Average B-2-B selling price in past 5 years |
23 | Competition from substitute products |
24 | Gross margin and average profitability of suppliers |
25 | New product development in past 12 months |
26 | M&A in past 12 months |
27 | Growth strategy of leading players |
28 | Market share of vendors, 2023 |
29 | Company Profiles |
30 | Unmet needs and opportunity for new suppliers |
31 | Conclusion |
32 | Appendix |