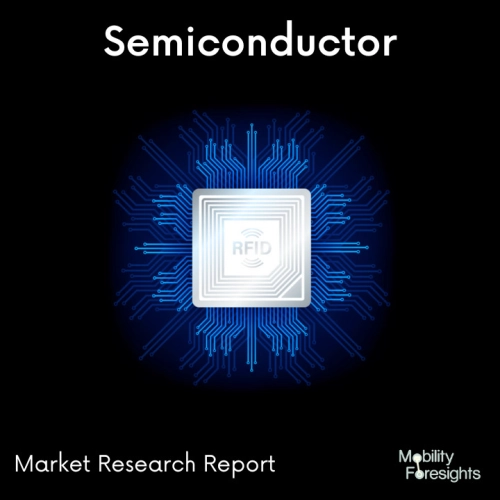
- Get in Touch with Us
Last Updated: Apr 25, 2025 | Study Period: 2023-2030
In general, the plasma ashing system comprises applying plasma to remove organic materials. For the plasma ashing process, the process gas is typically oxygen or a gas containing fluorine. If there is inorganic material, it will become a residue known as ash in the plasma asher.
Mostly volatile carbon oxides and water vapour are the byproducts of this process. The vacuum pump inside the plasma asher removes these byproducts from the system. Additionally, the polymers, residues, and masking material that generated during the plasma etch procedure are selectively removed by plasma ashing.
The Global Plasma ashing system market accounted for $XX Billion in 2022 and is anticipated to reach $XX Billion by 2030, registering a CAGR of XX% from 2023 to 2030.
The Quorum K1050X is a cutting-edge, solid-state RF plasma barrel reactor developed to satisfy the needs of research and development as well as small-scale manufacturing for a broad range of plasma ashing and plasma cleaning applications.
The K1050X RF Plasma Barrel Reactor is a powerful device designed to survive continuous useâ24 hours a day for some plasma ashing schedulesâand incorporates microprocessor control with automatic operation. It is also dependable and easy to use.
Wide variety of applications can benefit from barrel systems' ability to plasma etch or plasma ash isotropically (in all directions). The K1050X modifies specimen surfaces or removes specimen material in a gentle, regulated manner using a low pressure RF-induced gaseous discharge.
The plasma etching and ashing processes are dry (no wet chemicals are required) and occur at relatively low temperatures, which gives them a substantial advantage over competing approaches.
The use of a variety of process gases allows for a wide range of surface modification techniques. As the process gas, oxygen (or air) is used. As the molecules separate into chemically active atoms and molecules, the ensuing "combustion" products are conveniently transported away in the gas stream by the vacuum system.
In order to safely vent dangerous process gases, the K1050X must be situated so that it is close to the cylinders or source of process gas. For gas and vent connections, there should be sufficient access to the unit's back.
Sl no | Topic |
1 | Market Segmentation |
2 | Scope of the report |
3 | Abbreviations |
4 | Research Methodology |
5 | Executive Summary |
6 | Introduction |
7 | Insights from Industry stakeholders |
8 | Cost breakdown of Product by sub-components and average profit margin |
9 | Disruptive innovation in the Industry |
10 | Technology trends in the Industry |
11 | Consumer trends in the industry |
12 | Recent Production Milestones |
13 | Component Manufacturing in US, EU and China |
14 | COVID-19 impact on overall market |
15 | COVID-19 impact on Production of components |
16 | COVID-19 impact on Point of sale |
17 | Market Segmentation, Dynamics and Forecast by Geography, 2023-2030 |
18 | Market Segmentation, Dynamics and Forecast by Product Type, 2023-2030 |
19 | Market Segmentation, Dynamics and Forecast by Application, 2023-2030 |
20 | Market Segmentation, Dynamics and Forecast by End use, 2023-2030 |
21 | Product installation rate by OEM, 2023 |
22 | Incline/Decline in Average B-2-B selling price in past 5 years |
23 | Competition from substitute products |
24 | Gross margin and average profitability of suppliers |
25 | New product development in past 12 months |
26 | M&A in past 12 months |
27 | Growth strategy of leading players |
28 | Market share of vendors, 2023 |
29 | Company Profiles |
30 | Unmet needs and opportunity for new suppliers |
31 | Conclusion |
32 | Appendix |