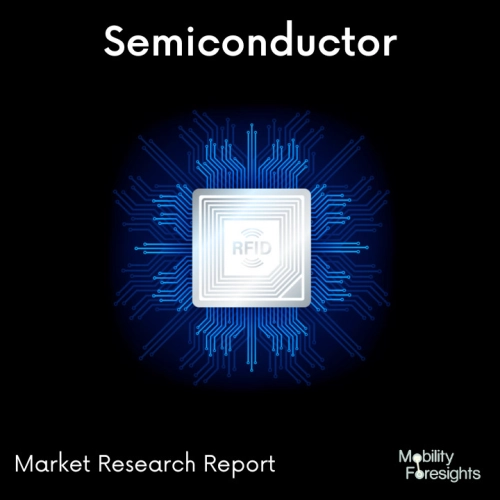
- Get in Touch with Us
Last Updated: Apr 25, 2025 | Study Period: 2023-2030
To obtain the desired qualities, polyimides are typically applied as a liquid and then thermally cured as a thin film or coating. To prevent cracks in the polyimide layer and colour changes, precise temperature consistency is crucial.
Low oxygen levels are achieved during this process to help produce brilliant material and good adherence, which is critical for the pattern recognition systems used in assembly. It is less expensive and simpler to handle non-photosensitive polyimide. Liquid by-products of thermal curing often do not settle on the process chamber walls since they are produced during the process.
The Global Polyimide curing equipment market accounted for $XX Billion in 2022 and is anticipated to reach $XX Billion by 2030, registering a CAGR of XX% from 2023 to 2030.
A polyimide curing oven called PCO2-14TM is a sanitary process oven made for baking and curing polyimide. The Despatch PCO2-14TM electrically powered oven was created to satisfy the precise process needs for inert atmosphere hard baking of polyimide coatings.
A pressure relief system, oxygen control system, and process monitoring system are just a few of the special features offered by this high-performance, clean process oven (ISO Class 5/Class 100 recirculated airflow) that enables it to meet the exact oxygen level and atmospheric requirements needed for polyimide curing.
The appropriate surface qualities are finally achieved during the "hard bake" polyimide cure process, which also removes any remaining solvent. The oven must be equipped with tools to help prevent and gather solvent condensation in order to remove solvents.
Despatch created the PCO2-14TM with a pressure relief system that features a detachable "cold trap," a convenient condensate trap that aids in preventing polyimide buildup in the oven's exhaust.
To help avoid oxidation of the polyimides being cured, the PCO2-14TM is an inert environment oven that allows the oxygen level to be kept at 20 ppm or below. The oven has an O2 monitor that is connected to the purge valve and activates the nitrogen purge once the oxygen level exceeds the set point for the O2 monitor.
When the nitrogen purge is finished, a controller that controls a modulating valve during the curing process keeps the O2 level at a predetermined value. Utilising less nitrogen while curing products consistently and repeatedly is the goal of this procedure.
Sl no | Topic |
1 | Market Segmentation |
2 | Scope of the report |
3 | Abbreviations |
4 | Research Methodology |
5 | Executive Summary |
6 | Introduction |
7 | Insights from Industry stakeholders |
8 | Cost breakdown of Product by sub-components and average profit margin |
9 | Disruptive innovation in the Industry |
10 | Technology trends in the Industry |
11 | Consumer trends in the industry |
12 | Recent Production Milestones |
13 | Component Manufacturing in US, EU and China |
14 | COVID-19 impact on overall market |
15 | COVID-19 impact on Production of components |
16 | COVID-19 impact on Point of sale |
17 | Market Segmentation, Dynamics and Forecast by Geography, 2023-2030 |
18 | Market Segmentation, Dynamics and Forecast by Product Type, 2023-2030 |
19 | Market Segmentation, Dynamics and Forecast by Application, 2023-2030 |
20 | Market Segmentation, Dynamics and Forecast by End use, 2023-2030 |
21 | Product installation rate by OEM, 2023 |
22 | Incline/Decline in Average B-2-B selling price in past 5 years |
23 | Competition from substitute products |
24 | Gross margin and average profitability of suppliers |
25 | New product development in past 12 months |
26 | M&A in past 12 months |
27 | Growth strategy of leading players |
28 | Market share of vendors, 2023 |
29 | Company Profiles |
30 | Unmet needs and opportunity for new suppliers |
31 | Conclusion |
32 | Appendix |