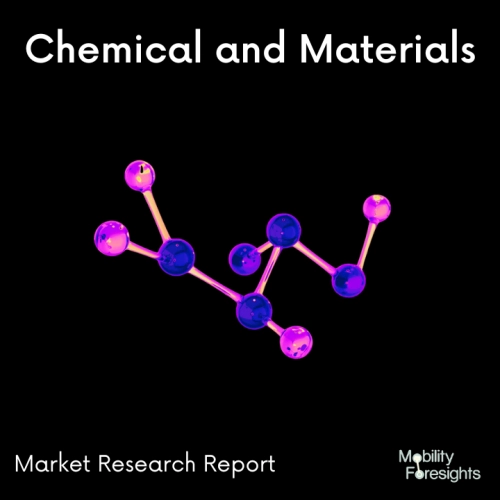
- Get in Touch with Us
Last Updated: Apr 25, 2025 | Study Period: 2024-2030
Many technical items, as well as those used in medicine and decoration, start off as raw materials with precious metal powders.
Creating silver composites for electrodes, catalysts, electrical contacts, or dental items is included in this. In addition to these, conductive paints and adhesives as well as precious metal powders are employed as the foundation material in preparations.
Small particles of about 1 to 100 m in diameter make precious metal powders. These particles differ from one another in terms of shape, size, and size distribution.
The shape of the silver particles can be spherical, crystalline, or dendritic, depending on the manufacturing process. Larger surface areas are often produced by smaller particle sizes.
There are many ways to make precious metal powders, including electrolysis, atomizing from the liquid state, chemical precipitation, and cementation with non-precious metals.
Silver powders, the by far most common precious metal powder utilised, have a variety of qualities that depend on the manufacturing process, as illustrated in. When a melt is atomized, a powder made of spherical particles with a high tap density is produced.
Randomly formed dendritic to crystalline particle shapes are produced by electrolytic deposition from a silver salt solution.
Particles produced by chemical reactions may be rather small but have a considerable specific surface area. Fine powders of the precious metal are mixed with organic solvents and paint base in a carrier to coat the surfaces. Such preparations can be applied using a paintbrush, a screen or tampon, spray, or immersion.
Conductive paints are liquid or paste-based precious metal compositions. In addition to the metal filler, they also include fine silver flakes as conductive pigments, an artificial resin-based paint component, and an organic solvent.
During air drying or ageing at slightly increased temperatures, the solvent evaporates. This makes it possible for the silver atoms to create conductive channels and join metallically.
The majority of mechanical bonding with minimal thermal impact uses conductive adhesives. High-polymer organic materials like epoxy resins and mixed polymers are typically employed as the adhesive's constituent parts.
They are constructed using electrical filler materials like silver powder in the form of flakes. Conductive adhesives based on silver are offered in single-component and two-component adhesive solutions. Both types are becoming harder without the use of pressure.
The Global Precious Metal Powder market accountedfor $XX Billion in 2023 and is anticipated to reach $XX Billion by 2030, registering a CAGR of XX% from 2024 to 2030.
The inertness and intrinsic value of precious metals are the key reasons why they are frequently used in a wide range of industries.
This latter factor is another justification for investing in time and resource-saving technology that cut down on metal losses and scrap.
When compared to conventional precious metals forming, powder metallurgy is an intriguing and potent alternative that can either improve performance (in terms of cost, time, and complexity) or reduce costs.
The employment of alternative sintering procedures that have been adapted from the smelting industries is made possible by the steadily growing availability of metal-based alloys with advanced properties that are delivered in powder form.
Using methods already developed for processing other ferrous and non-ferrous metals, powder metallurgy applied to precious metals processing enables the creation of both unusual shapes and as of yet unknown alloys.
Sl no | Topic |
1 | Market Segmentation |
2 | Scope of the report |
3 | Abbreviations |
4 | Research Methodology |
5 | Executive Summary |
6 | Introduction |
7 | Insights from Industry stakeholders |
8 | Cost breakdown of Product by sub-components and average profit margin |
9 | Disruptive innovation in the Industry |
10 | Technology trends in the Industry |
11 | Consumer trends in the industry |
12 | Recent Production Milestones |
13 | Component Manufacturing in US, EU and China |
14 | COVID-19 impact on overall market |
15 | COVID-19 impact on Production of components |
16 | COVID-19 impact on Point of sale |
17 | Market Segmentation, Dynamics and Forecast by Geography, 2024-2030 |
18 | Market Segmentation, Dynamics and Forecast by Product Type, 2024-2030 |
19 | Market Segmentation, Dynamics and Forecast by Application, 2024-2030 |
20 | Market Segmentation, Dynamics and Forecast by End use, 2024-2030 |
21 | Product installation rate by OEM, 2023 |
22 | Incline/Decline in Average B-2-B selling price in past 5 years |
23 | Competition from substitute products |
24 | Gross margin and average profitability of suppliers |
25 | New product development in past 12 months |
26 | M&A in past 12 months |
27 | Growth strategy of leading players |
28 | Market share of vendors, 2023 |
29 | Company Profiles |
30 | Unmet needs and opportunity for new suppliers |
31 | Conclusion |
32 | Appendix |