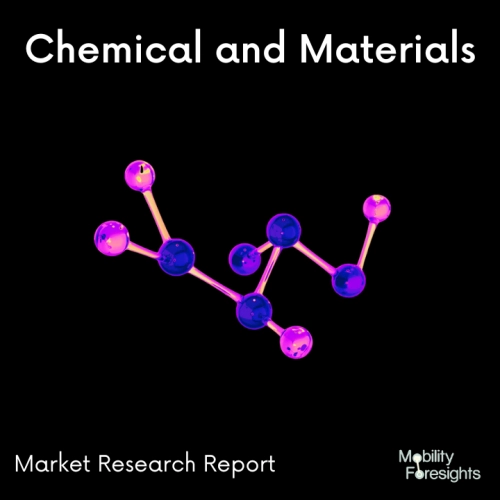
- Get in Touch with Us
Last Updated: Apr 25, 2025 | Study Period: 2024-2030
Pure sintering pastes, which are highly silver-filled pastes devoid of any resin in the matrix, are capable of achieving extremely high thermal conductivity, but they also have limitations and require specialised processing, such as high temperature and high pressure, to get rid of porosity or voiding.
Because AG has the best electrical conductivity, the second-best thermal conductivity, and the highest thermal stability, it has garnered interest as a pure silver sintering die attach paste.
Additionally, the pure metallic bond created at the interface offered significantly higher reliability than solder. No resin is present in the matrix; only pure sintering paste. These highly silver-filled pastes have a limited range of application and necessitate specialised processing, such as high temperature.
The Global Pure Sintering Paste market accounted for $XX Billion in 2021 and is anticipated to reach $XX Billion by 2030, registering a CAGR of XX% from 2024 to 2030.
SSP, a pure sintering material based on solvent-based sintering, was the first sintering material created by CAPLINQ ten years ago. Depending on the needs of the application, this can be used both with and without pressure.
High thermal semi-sintering die attach materials enable reliable package-level sintering and get around the problems that pure sintering pastes have with processability, thermal conductivity, and solder regulation.
For today's high power density devices, the LOCTITE ABLESTIK ABP 8068T portfolio of CAPLINQ offers high thermal, semi-sintering die attach pastes that simplify processing and provide best-in-class thermal and electrical performance with robust reliability. Additionally, they provide void-free bond lines and an open time of up to two hours, promoting high reliability and manufacturing flexibility.
Sl no | Topic |
1 | Market Segmentation |
2 | Scope of the report |
3 | Abbreviations |
4 | Research Methodology |
5 | Executive Summary |
6 | Introduction |
7 | Insights from Industry stakeholders |
8 | Cost breakdown of Product by sub-components and average profit margin |
9 | Disruptive innovation in the Industry |
10 | Technology trends in the Industry |
11 | Consumer trends in the industry |
12 | Recent Production Milestones |
13 | Component Manufacturing in US, EU and China |
14 | COVID-19 impact on overall market |
15 | COVID-19 impact on Production of components |
16 | COVID-19 impact on Point of sale |
17 | Market Segmentation, Dynamics and Forecast by Geography, 2024-2030 |
18 | Market Segmentation, Dynamics and Forecast by Product Type, 2024-2030 |
19 | Market Segmentation, Dynamics and Forecast by Application, 2024-2030 |
20 | Market Segmentation, Dynamics and Forecast by End use, 2024-2030 |
21 | Product installation rate by OEM, 2023 |
22 | Incline/Decline in Average B-2-B selling price in past 5 years |
23 | Competition from substitute products |
24 | Gross margin and average profitability of suppliers |
25 | New product development in past 12 months |
26 | M&A in past 12 months |
27 | Growth strategy of leading players |
28 | Market share of vendors, 2023 |
29 | Company Profiles |
30 | Unmet needs and opportunity for new suppliers |
31 | Conclusion |
32 | Appendix |