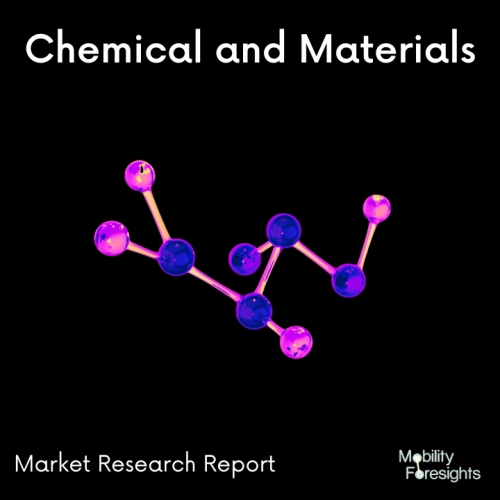
- Get in Touch with Us
Last Updated: Apr 25, 2025 | Study Period: 2024-2030
Reaction Injection Molding is a low pressure, low temperature process used to mold many types of plastic parts. This process is typically used for the medical, industrial and automotive industries. Reaction Injection Molding (RIM) is often utilized for the molding of strong, lightweight parts that are easily painted. The rigid materials used by Design Octaves come with a ULV rating for flammability.
The Reaction Injection Molding molding material utilized by Design Octaves is a two-component system which consists of polyol and isocyanate liquids that are mixed at a high pressure and then metered into the closed tool at a low pressure. The material then expands to fill the tool and is ejected in about minutes.
The reaction injection molding (RIM) process utilizes low-viscosity liquid polymers. These polymers expand and thicken through a variety of chemical reactions. After the polymers have been injected into the heated mold they eventually harden.
Through the RIM design process raw materials and molding techniques can be selected, and customized, to deliver the desired weight, strength, density and hardness characteristics that you are looking for. The result is polyurethane parts with much lighter weight, and more intricate designs than those created by ordinary injection molding.
The Global Reaction Injection Molding market accounted for $XX Billion in 2023 and is anticipated to reach $XX Billion by 2030, registering a CAGR of XX% from 2024 to 2030.
Covestro and Arcesso Dynamics launch breakthrough in solid-surface manufacturing.
Covestro, a polymer manufacturer, and Arcesso Dynamics, a manufacturer of custom polyurethane parts, launch Arfinio, a breakthrough manufacturing solution, at K plastics trade fair in Düsseldorf, Germany. The solution is based on reaction injection moulding (RIM) on aliphatic polyurethanes.
Previously considered impossible, this technology enables manufacturers to benefit from new combinations of design freedom, functional performance, and sustainability in multiple solid-surface and injection-moulded applications.
Arfinio material is made by injection moulding of a combination of high-performance liquid polymers and unique minerals. This produces truly seamless shapes without requiring sheets.
In this way, the technology combines the key benefits of aliphatic chemistry, injection moulding, and solid surfaces: mechanical resistance, light-stability, and repairability, as well as low product weight, quick production, and improved design freedom.
Sl no | Topic |
1 | Market Segmentation |
2 | Scope of the report |
3 | Abbreviations |
4 | Research Methodology |
5 | Executive Summary |
6 | Introduction |
7 | Insights from Industry stakeholders |
8 | Cost breakdown of Product by sub-components and average profit margin |
9 | Disruptive innovation in the Industry |
10 | Technology trends in the Industry |
11 | Consumer trends in the industry |
12 | Recent Production Milestones |
13 | Component Manufacturing in US, EU and China |
14 | COVID-19 impact on overall market |
15 | COVID-19 impact on Production of components |
16 | COVID-19 impact on Point of sale |
17 | Market Segmentation, Dynamics and Forecast by Geography, 2024-2030 |
18 | Market Segmentation, Dynamics and Forecast by Product Type, 2024-2030 |
19 | Market Segmentation, Dynamics and Forecast by Application, 2024-2030 |
20 | Market Segmentation, Dynamics and Forecast by End use, 2024-2030 |
21 | Product installation rate by OEM, 2023 |
22 | Incline/Decline in Average B-2-B selling price in past 5 years |
23 | Competition from substitute products |
24 | Gross margin and average profitability of suppliers |
25 | New product development in past 12 months |
26 | M&A in past 12 months |
27 | Growth strategy of leading players |
28 | Market share of vendors, 2023 |
29 | Company Profiles |
30 | Unmet needs and opportunity for new suppliers |
31 | Conclusion |
32 | Appendix |