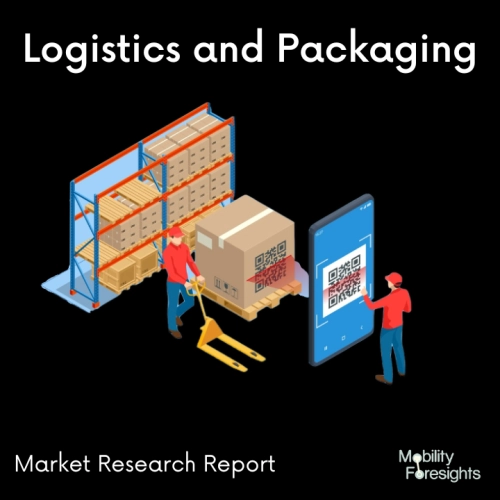
- Get in Touch with Us
Last Updated: Apr 25, 2025 | Study Period: 2023-2030
A recycled packaging material made to be recycled again is called moulded pulp. It is highly likely that the pulp fibre material you may have encountered served a variety of functions during its existence.
All of pulp's products can be recycled in any household or public recycling facility because of the material's composition. Many fibrous materials,such as recycled paper, cardboard, and natural plant fibres, are used to make pulp packing.
The colour, texture, and power of the pack are all influenced by these raw components. Moulded pulp is shaped into a specific shape so that it may securely retain a high-end product or fit inside a box flawlessly.
Many fibrous materials, including recycled paper, cardboard, and natural plant fibres, are used to make pulp packaging. The colour, texture, and power of the pack are all influenced by these raw components.
Recycled paper and pulp are often misunderstood to be of poor quality and fibrous. Nowadays, pulp offers a sturdy, long-lasting, and highly customizable option for high-end packaging. It can withstand wetness and has good cushioning qualities. It is also unaffected by high temperatures. Moreover, pulp is inexpensive.
Large production runs can be produced for relatively low costs, which may allow businesses to save the expense of developing new packaging. Its form and dimensions can be totally customised to fit the priceless goods within, which has the added advantage of enhancing product integrity.
100% recyclable raw materials are used to manufacture pulp. This renders it recyclable and biodegradable. The production of pulp packaging produces less effluent and toxic byproducts, which improves a brand's reputation in the sustainable era.
There are several steps involved in creating pulp packing. Initially, a pulp slurry is created by combining the raw materials (cardboard, newspaper, and natural fibres) with water.
The pulp slurry tank is entered using a mesh-forming instrument. The slurry is forced through the mesh tool by a vacuum until the appropriate thickness is reached. The damp components are taken out of the mesh tools and dried. The dried pieces are distorted and rough.
The parts are pressed by hot metal tools to polish the surfaces. At this point, embossed logos or artwork can also be used. The edges are finally trimmed, and any windows or holes are die cut (more info).
Moulded pulp packaging, as opposed to conventional folded cardboard boxes, features rounded corners and intricate three-dimensional shapes.
The Global Recycled Paper Pulp Protection Packaging market accountedfor $XX Billion in 2022 and is anticipated to reach $XX Billion by 2030, registering a CAGR of XX% from 2023 to 2030.
According to the company, both at the kerbside and in paper waste streams, its novel approach is completely recyclable and devoid of plastic. According to its purported biodegradability, the substance won't cause pollution if it gets into the environment.
Furthermore, no toxic chemicals, blowing agents, solvents, or fossil fuels are reported to be used in its creation. According to reports, the wood-based materials used in the pilot plant at Stora Enso's Fors Mill, which has been running for almost a year, are supplied from sustainably managed forests and foamed in both air and water.
To ensure that just the necessary amount of packaging is used, Stora Enso claims that the foam can be uniquely optimised for the shape and size of the product it is intended to cushion.
Papira is anticipated to take the place of polymeric packaging foams made from fossil fuels such expanded polystyrene, polyurethane, and polyethylene.
It is still being evaluated for certifications in terms of recycling and biodegradability, and a carbon footprint analysis is being done right now to find methods to make it more sustainable.
This increases the amount of fibre it can produce. They previously spoke with, senior vice president for formed fibre at Stora Enso, about the company's partnership with Pulpex in an effort to industrialise the production of packaging made from wood fibre pulp.
He suggested that the initiative is important for the environment because paper and cardboard are recycled at higher rates around the world than plastic.
Sl no | Topic |
1 | Market Segmentation |
2 | Scope of the report |
3 | Abbreviations |
4 | Research Methodology |
5 | Executive Summary |
6 | Introduction |
7 | Insights from Industry stakeholders |
8 | Cost breakdown of Product by sub-components and average profit margin |
9 | Disruptive innovation in the Industry |
10 | Technology trends in the Industry |
11 | Consumer trends in the industry |
12 | Recent Production Milestones |
13 | Component Manufacturing in US, EU and China |
14 | COVID-19 impact on overall market |
15 | COVID-19 impact on Production of components |
16 | COVID-19 impact on Point of sale |
17 | Market Segmentation, Dynamics and Forecast by Geography, 2023-2030 |
18 | Market Segmentation, Dynamics and Forecast by Product Type, 2023-2030 |
19 | Market Segmentation, Dynamics and Forecast by Application, 2023-2030 |
20 | Market Segmentation, Dynamics and Forecast by End use, 2023-2030 |
21 | Product installation rate by OEM, 2023 |
22 | Incline/Decline in Average B-2-B selling price in past 5 years |
23 | Competition from substitute products |
24 | Gross margin and average profitability of suppliers |
25 | New product development in past 12 months |
26 | M&A in past 12 months |
27 | Growth strategy of leading players |
28 | Market share of vendors, 2023 |
29 | Company Profiles |
30 | Unmet needs and opportunity for new suppliers |
31 | Conclusion |
32 | Appendix |