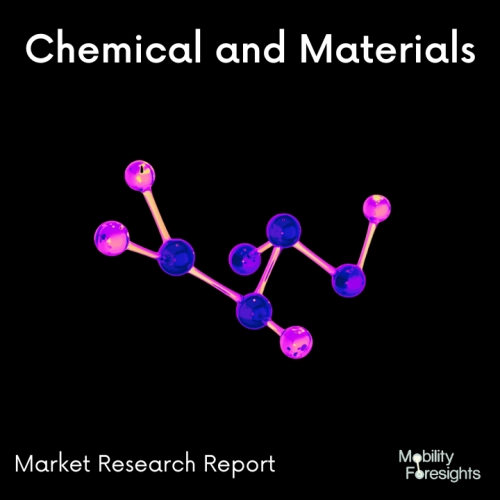
- Get in Touch with Us
Last Updated: Apr 25, 2025 | Study Period: 2024-2030
Vacuum distillation is a refining method that aids in the production of petroleum products from the heavier oils leftover following atmospheric distillation. The atmospheric distillation unit (ADU) in the refining process separates the lighter hydrocarbons from the heavier oils based on boiling point.
The process of vacuum distillation is used to reduce the pressure above a liquid to less than its vapour pressure. This permits the most volatile liquids to be boiled off and distilled selectively.
The Global Refinery Vacuum Distillation Units Market accounted for $XX Billion in 2023 and is anticipated to reach $XX Billion by 2030, registering a CAGR of XX% from 2024 to 2030.
Advances in Vacuum Unit Technology and Operations. Vacuum distillation has emerged as a crucial link in the chain that maximises crude oil upgrading. Vacuum petrol oil (VGO), lubricating oils and/or conversion feedstocks are frequently generated as distillates.
Vacuum distillation residue can be utilised as bitumen feedstock, as a fuel component, or as a feedstock for further upgrading. Recent decades have seen significant advancements in vacuum distillation technology, including the vacuum unit. Maximising the recovery of valuable distillates and lowering the units' energy usage have been the major goals. For instance, depending on feed quality, the direct fuel intake of modern, efficient hoover units is 1.0%.
To get the highest distillate production, the temperature and pressure in the flash zone where the heated feed is injected into the vacuum column should be as high as they can be. There are limits to the flash temperature. Without the use of 'lifting' steam, the older type high vacuum systems could not reach the necessary low hydrocarbon partial pressure in the flash zone.
The steam behaves similarly to the crude distillation units' stripping steam. "Wet" units are what this kind of unit is known as.The deep vacuum flashers, which don't need steam, are one of the most recent advancements in vacuum distillation. These "dry" units run at extremely low pressure dips over the internals of the column and flash zone pressures.
Low pressure drop spray sections have taken the place of the traditional reflux sections with fractionation trays because of this. In comparison to "wet" units, dry high-vacuum machines consume substantially less steam. Instead of being net steam consumers, they are now net steam producers.