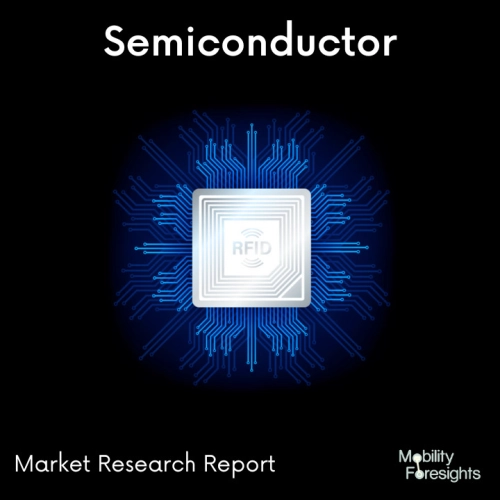
- Get in Touch with Us
Last Updated: Apr 25, 2025 | Study Period:
The Rigid-Flex PCB market is witnessing significant growth driven by the increasing demand for compact and lightweight electronic devices across various industries. Rigid-Flex PCBs offer unique design flexibility and reliability compared to traditional rigid or flexible PCBs, making them suitable for applications where space constraints and complex geometries are prevalent.
Industries such as aerospace, automotive, medical devices, consumer electronics, and telecommunications are increasingly adopting Rigid-Flex PCBs to address the need for miniaturization and enhanced performance in electronic assemblies. Additionally, the proliferation of IoT devices, wearables, and portable electronics is fueling the demand for Rigid-Flex PCBs, as they enable seamless integration of components and improve overall system reliability.
Technological advancements in materials, manufacturing processes, and design software are further driving market growth, allowing for the development of more complex and reliable Rigid-Flex PCB solutions. Moreover, stringent regulatory requirements and standards for electronic devices in terms of safety, reliability, and performance are also driving the adoption of Rigid-Flex PCBs, as they offer superior mechanical strength and durability compared to conventional PCBs.
Overall, the Rigid-Flex PCB market is poised for continued expansion as industries continue to prioritize innovation, miniaturization, and reliability in electronic product development.
The Rigid-Flex PCB (Printed Circuit Board) market represents a crucial segment within the electronics industry, playing a pivotal role in the design and production of modern electronic devices. Rigid-Flex PCBs offer a unique combination of flexibility and rigidity, allowing for complex three-dimensional configurations while maintaining structural integrity and reliability.
This innovative technology enables manufacturers to create compact and lightweight electronic products with enhanced durability and performance. With applications ranging from consumer electronics and automotive systems to aerospace and medical devices, the demand for Rigid-Flex PCBs continues to grow rapidly, driven by advancements in technology and increasing requirements for miniaturization and functionality. As industries strive for more efficient and versatile electronic solutions, the Rigid-Flex PCB market stands at the forefront of innovation, poised to reshape the future of electronic design and manufacturing.
The Rigid-Flex PCB market is estimated to be worth $ XX billion by 2030 and is expected to grow at a compound annual growth rate (CAGR) of YY%. Another report projects that the market will reach $XX billion by 2030, growing at a CAGR of YY% from 2024 to 2030.
Applications for rigid flex printed circuit boards are numerous and include anything from medical monitoring to surgical equipment, consumer electronics, industrial electronics, and more.
However, given that the healthcare sector is digitizing quickly and makes up 10% on average of a nation's GDP, PCB is employed in healthcare more frequently than it is in the pharmaceutical industry. The stiff flex PCBs are good in overcoming weight and space issues with spatial degrees of freedom in consumer devices.
The Rigid Flex PCB market will expand as a result of improvements in industrial electronics, particularly for applications in factory automation and building automation.Additionally, the Rigid Flex PCB market will expand due to developments in the healthcare and pharmaceuticals industries, which include a wide range of monitoring and surgical equipment along with numerous other wearable gadgets.
The demand for navigation systems, vehicle tracking systems, and information display systems in these vehicles will fuel market growth. Additionally, with the introduction of new technologies in vehicles and the mainstreaming of electric vehicles, the automotive sector is experiencing tremendous demand.
Copper foil, electrolytic solvents, and cobalt salts are some of the materials used to make PCBs, but as their manufacturing costs rise, businesses are being diverted from developing aggressive pricing strategies.
The North American market, particularly the USA, will be one of the prime markets for Rigid-Flex PCB Market due to the nature of industrial automation in the region, high consumer spending compared to other regions, and the growth of various industries, mainly AI, along with constant technological advancements. The GDP of the USA is one of the largest in the world, and it is home to various industries such as Pharmaceuticals, Aerospace, and Technology. The average consumer spending in the region was $72K in 2023, and this is set to increase over the forecast period. Industries are focused on industrial automation and increasing efficiency in the region. This will be facilitated by the growth in IoT and AI across the board. Due to tensions in geopolitics, much manufacturing is set to shift towards the USA and Mexico, away from China. This shift will include industries such as semiconductors and automotive.
The European market, particularly Western Europe, is another prime market for Rigid-Flex PCB Market due to the strong economic conditions in the region, bolstered by robust systems that support sustained growth. This includes research and development of new technologies, constant innovation, and developments across various industries that promote regional growth. Investments are being made to develop and improve existing infrastructure, enabling various industries to thrive. In Western Europe, the margins for Rigid-Flex PCB Market are higher than in other parts of the world due to regional supply and demand dynamics. Average consumer spending in the region was lower than in the USA in 2023, but it is expected to increase over the forecast period.
Eastern Europe is anticipated to experience a higher growth rate compared to Western Europe, as significant shifts in manufacturing and development are taking place in countries like Poland and Hungary. However, the Russia-Ukraine war is currently disrupting growth in this region, with the lack of an immediate resolution negatively impacting growth and creating instability in neighboring areas. Despite these challenges, technological hubs are emerging in Eastern Europe, driven by lower labor costs and a strong supply of technological capabilities compared to Western Europe.
There is a significant boom in manufacturing within Europe, especially in the semiconductor industry, which is expected to influence other industries. Major improvements in the development of sectors such as renewable energy, industrial automation, automotive manufacturing, battery manufacturing and recycling, and AI are poised to promote the growth of Rigid-Flex PCB Market in the region.
Asia will continue to be the global manufacturing hub for (xx Market) over the forecast period with China dominating the manufacturing. However, there will be a shift in manufacturing towards other Asian countries such as India and Vietnam. The technological developments will come from China, Japan, South Korea, and India for the region. There is a trend to improve the efficiency as well as the quality of goods and services to keep up with the standards that are present internationally as well as win the fight in terms of pricing in this region. The demand in this region will also be driven by infrastructural developments that will take place over the forecast period to improve the output for various industries in different countries.
There will be higher growth in the Middle East as investments fall into place to improve their standing in various industries away from petroleum. Plans such as Saudi Arabia Vision 2030, Qatar Vision 2030, and Abu Dhabi 2030 will cause developments across multiple industries in the region. There is a focus on improving the manufacturing sector as well as the knowledge-based services to cater to the needs of the region and the rest of the world. Due to the shifting nature of fossil fuels, the region will be ready with multiple other revenue sources by the time comes, though fossil fuels are not going away any time soon.
Africa is expected to see the largest growth in (xx Market) over the forecast period, as the region prepares to advance across multiple fronts. This growth aligns with the surge of investments targeting key sectors such as agriculture, mining, financial services, manufacturing, logistics, automotive, and healthcare. These investments are poised to stimulate overall regional growth, creating ripple effects across other industries as consumer spending increases, access to products improves, and product offerings expand. This development is supported by both established companies and startups in the region, with assistance from various charitable organizations. Additionally, the presence of a young workforce will address various existing regional challenges. There has been an improvement in political stability, which has attracted and will continue to attract more foreign investments. Initiatives like the African Continental Free Trade Area (AfCFTA) are set to facilitate the easier movement of goods and services within the region, further enhancing the economic landscape.
Latin America and the Oceania region will showcase growth over the forecast period in (xx Market). In Latin America, the focus in the forecast period will be to improve their manufacturing capabilities which is supported by foreign investments in the region. This will be across industries mainly automotive and medical devices. There will also be an increase in mining activities over the forecast period in this region. The area is ripe for industrial automation to enable improvements in manufacturing across different industries and efficiency improvements. This will lead to growth of other industries in the region.
Margin Comparison (Highest to lowest) | Region | Remarks |
1 | Europe | The supply chain demands and the purchasing power in the region enable suppliers to extradite a larger margin from this region than other regions. This is for both locally manufactured as well as imported goods and services in the region. |
2 | North America | Due to the high spending power in this region, the margins are higher compared to the rest of the world, but they are lower than Europe as there is higher competition in this region. All the suppliers of goods and services target USA as a main market thereby decreasing their margins compared to Europe |
3 | Asia | Lower purchasing power, coupled with higher accessibility of services in this regions doesnât enable suppliers to charge a high margin making it lower than Europe and North America. The quality of goods and services are also affected due to this aspect in the region |
4 | Africa and ROW | The margins are the lowest in this region, except for Australia and New Zealand as the countries in this region donât have much spending power and a large portion of the products and services from this area is exported to other parts of the world |
USAâ $210 billion is allocated to federal R&D with main focus on health research, clean energy, semiconductor manufacturing, sustainable textiles, clean energy, and advanced manufacturing. Investments by private players are mainly focused on technological development including 5G infrastructure and AI in the region.
Europeâ EIC is investing â¬1 billion to innovative companies in sectors like AI, biotechnology, and semiconductors. There is also a focus on developing the ecosystem in the continent as well as improving the infrastructure for developing industries such as electric vehicles and sustainable materials. Private players are targeting data centers, AI, battery plants, and high end technological R&D investments.
Asiaâ There are investments to tackle a range of scientific and technological advancements in this region mainly coming in from China, India, South Korea, and Japan. This will include artificial intelligence, 5G, cloud computing, pharmaceutical, local manufacturing, and financial technologies. Many countries are aiming to be digital hubs including Saudi Arabia.
Africaâ Investments in the region are focused on improving the technological capabilities in the region along with socio-economic development and growth. Private participants of investments in this region is venture capital dominated who are targeting the various growth elements of the region as social stability improves. The major industries are fintech, easier lending, and manufacturing.
Latin Americaâ The focus in the region is for fintech, e-commerce, and mobility sectors. There are also investments in improving manufacturing in the region. Local investments is focused on improving the healthcare, and transportation infrastructure in the region. The region is attracting foreign investments to improve their ability to utilize the natural resources present in the region.
Rest of the Worldâ The investments in this region are focused on clean energy, green metals, and sustainable materials. Funds in Australia are focused on solar energy and battery technologies, along with high end futuristic areas such as quantum computing. The main countries of private investment in ROW will be Australia, Canada, and New Zealand.
In the ever-evolving landscape of printed circuit boards (PCBs), the rigid-flex PCB market is witnessing a significant trend towards miniaturization and increased functionality. With advancements in electronic devices demanding smaller and more lightweight components, rigid-flex PCBs offer a compelling solution by combining the benefits of both rigid and flexible substrates. This trend is particularly evident in industries such as consumer electronics, automotive, aerospace, and medical devices, where space constraints and performance requirements are driving the need for innovative PCB designs.
Moreover, the adoption of advanced materials and manufacturing processes is further shaping the trajectory of the rigid-flex PCB market. Manufacturers are exploring new materials with enhanced thermal conductivity, flexibility, and reliability to meet the demanding specifications of modern electronic applications. Additionally, advancements in manufacturing techniques such as additive manufacturing and laser processing are enabling the production of intricate and highly customized rigid-flex PCB designs.
Furthermore, the growing demand for smart and connected devices is fueling the expansion of the rigid-flex PCB market. As the Internet of Things (IoT) ecosystem continues to grow, there is a heightened need for PCBs that can accommodate complex sensor arrays, wireless connectivity modules, and other components in a compact and durable form factor. Rigid-flex PCBs offer the flexibility and durability required to withstand the rigors of IoT applications while enabling seamless integration into various devices and systems.
Overall, the trend towards miniaturization, enhanced functionality, and advanced manufacturing processes is driving the growth of the rigid-flex PCB market. As technology continues to evolve, rigid-flex PCBs are expected to play a crucial role in enabling the development of next-generation electronic devices across a wide range of industries.
In the dynamic landscape of the Rigid-Flex PCB market, recent advancements in product development are reshaping the industry with innovative solutions that cater to the evolving needs of various sectors. One notable new development is the introduction of enhanced materials and manufacturing techniques that enable the production of Rigid-Flex PCBs with increased flexibility, durability, and reliability.
These advancements allow for the creation of intricate designs and compact form factors, making Rigid-Flex PCBs suitable for a wide range of applications, including consumer electronics, automotive, aerospace, and medical devices. Additionally, manufacturers are focusing on incorporating advanced features such as high-speed transmission, impedance control, and thermal management into Rigid-Flex PCBs, further expanding their capabilities and versatility.
Furthermore, the integration of emerging technologies such as Internet of Things (IoT), 5G connectivity, and artificial intelligence (AI) is driving demand for Rigid-Flex PCBs with specialized functionalities, opening up new opportunities for innovation and growth in the market. Overall, these new developments underscore a shift towards more advanced and flexible Rigid-Flex PCB solutions that meet the demands of modern electronic devices and applications.
SL NO | TOC |
1 | Market Segmentation |
2 | Scope of the report |
3 | Research Methodology |
4 | Executive Summary |
5 | Introduction |
6 | 5 Key Predictions for Rigid-Flex PCB Market |
7 | Insights from Industry stakeholders |
8 | Cost breakdown of Product by sub-components and average profit margin |
9 | Average B-2-B selling price in past 5 years |
10 | New product development in past 12 months |
11 | Expansion and Applications of the Rigid-Flex PCB |
12 | Importance of Technological innovation |
13 | Impact Thermal Storage Systems and Smart Grid Integration |
14 | Market Size, Dynamics and Forecast by Application , 2024-2030 |
15 | Market Size, Dynamics and Forecast by End-use industry, 2024-2030 |
16 | Market Size, Dynamics and Forecast by Type, 2024-2030 |
17 | Market Size, Dynamics and Forecast by Geography, 2024-2030 |
18 | Market Size, Dynamics and Forecast by Technology, 2024-2030 |
19 | Competitive Landscape |
20 | Gross margin and average profitability of suppliers |
21 | M&A in past 12 months |
22 | Growth strategy of leading players |
23 | Market share of vendors, |
24 | Company Profiles |
25 | Unmet needs and opportunity for new suppliers |
26 | Conclusion |