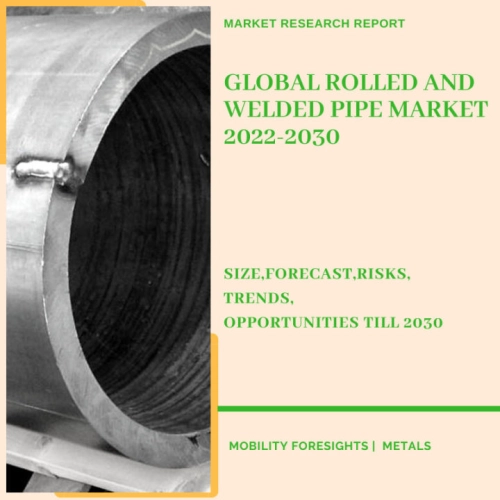
- Get in Touch with Us
Last Updated: Apr 25, 2025 | Study Period: 2022-2030
One of the first methods of producing steel pipe was rolling and welding. When the pipe wall thickness is more than what can be produced using the spiral weld and high-frequency electric resistance weld (ERW) pipe manufacturing methods, this manufacturing procedure is used.
By using a roller or plate bending machine to cold form a flat strip, sheet, or plate into a rounded or circular shape, a welded pipe is created.
The pipe is then joined using a high energy source, either with filler material or without. Without any size limitations, massive sizes of welded pipes can be made.Sections of plate are rolled into cans to create rolled and welded pipe. To create the final pipe, the individual cans are first joined together after the can's seam has been welded.
The global rolled and welded pipe market accounted for $XX Billion in 2021 and is anticipated to reach $XX Billion by 2030, registering a CAGR of XX% from 2022 to 2030.
High frequency straight seam welded pipe (ERW) is made from a hot-rolled coil plate that has been developed by a machine employing the skin effect and proximity effect of high frequency current to melt and heat the tube blank's edge and pressure welding while being squeezed by a roller. in order to produce.
In the 1950s, the process of high-frequency resistance welding was used to create welded pipes. Its production technique has advanced steadily over the past ten years, and the quality of the products has increased as well.
Hot-rolled steel strip for large and medium-calibre ERW steel have significantly increased appearance size, appearance quality, and physical and chemical qualities thanks to the employment of controlled rolling and controlled cooling technologies in the rolling process.
The production of large and medium-calibre ERW steel pipes that undergo welding heat treatment is automated, and the computer's automatic compensation system effectively regulates the heat input energy during the high-frequency welding process, preventing the welding heat input energy from falling below a certain level.
The subsequent cold welding, virtual welding, and overheating brought on by a high heat input energy. The quality of the weld and heat affected zone is effectively guaranteed through the regulation of the intermediate frequency heat treatment temperature, which enables the heat treatment process to obtain the best results in accordance with process requirements.
The ERW welded pipe industry in Japan has grown quickly. A 508 mm ERW welded pipe production facility is shared by Nippon Steel & Steel Corporation, Sumsei Metals, and Wakayama Ironworks. A 609 mm ERW welded pipe production line is shared by Kawasaki Chita Steel Works and Japan Steel Pipeline Keihan Steel Works.
Currently, the production of ERW welded pipes makes up between 70 and 75 percent of the total production of Japanese steel pipes, whereas the production of spiral seam submerged arc welded pipes is lower. Additionally, online or offline full-weld ultrasonic or eddy current exploration injuries have been made possible by advancements in detecting technologies.
The COVID-19 pandemic confronted the rolled and welded pipes industry with unheard-of difficulties, just like it did for most other industries. Players in the industry struggled to find raw materials, recruit personnel from sanatoriums, and provide finished goods, among other issues.
As a result, the market for rolled and welded pipes witnessed unforeseen outages, whipsaw pricing, and wrecked supply networks.
On the other hand, the pandemic increased market demand, which led to a number of urban issues such densification and insufficient water sanitation availability. However, with many countries' lockdown restrictions being relaxed, the market is quickly returning to normal.
Submerged Arc Welding Technology.Submerged arc welding (SAW) is a high-deposition-rate arc welding technology that uses a continuous melting wire or strip electrode. The procedure, which lends itself well to automation, is largely utilised for welding lengthy seams to an exceptionally high quality level.
SAW systems from AWS Schäfer are offered in longitudinal and circumferential seam welding systems, plate welding systems, and automatic welding machine supports, depending on the application.
The systems may accommodate up to seven welding heads. The systems are outfitted with the most recent energy-saving inverter welding power source technology to improve efficiency. Individual preferences can be used to pick power source manufacturers.
We connect all prominent manufacturers into our own process management system, AWS ONE Master management, using standard interfaces.
The programme has a user-friendly interface that makes controlling the entire process easier. A touch panel is used to set up and control all welding heads.
All traceability requirements are met by the tracking welding data monitoring system, which may be incorporated into the quality management system.
With the most recent welding powder supply systems, you may be certain of long-term sustainability in the field of filler materials. Powder quality and efficiency are ensured by heated powder systems with powder recovery and powder preparation.
AWS Schäfer's submerged arc plate welding equipment may be utilised to produce steel plate sizes that are difficult to fabricate due to technological or logistical constraints. Welded plates are used in the fabrication of development lengths of large diameter pipe sections for offshore foundations, as well as the production of composite panels in shipbuilding.
When a pipe or vessel needs to be welded longitudinally and circumferentially from the inside as well as the exterior, Column & Boom Submerged Arc Welding Machines are always employed.
With the most recent generation of Column & Boom Submerged Arc Welding Machines, you may execute 1-wire, tandem, or 3-wire submerged arc welding with utmost stability, little judder, and minimal vibration. A second GMAW welding torch might be placed in front of the submerged arc welding head thanks to the modular system's flexibility.
Because of the distinctive roller guide system, system motions are wear-free, and the need for time-consuming and expensive replacement of worn-out spindles or racks is a thing of the past. Under the most challenging operating circumstances in three-shift operation, this robust and strong design ensures a constantly steady production process and extended service life.
The AWS ONE Master Control welding and system control is the key component of the submerged arc welding systems. All of the system's control peripherals and functionalities are integrated into one unified operating system via carefully synchronised hardware and software components.
The communication with the welding power sources can be done using any standard interface, such as Profibus, Profinet, CanOpen, or DeviceNet.
The control system offers simultaneous process observation and customization of all welding parameters with integration of up to seven welding wires.
Weld quality is recorded using the welding data recording system "Welding Data Analyzer" that is continuously running in the background.
The recordings are visually inspected and utilised to verify the documented procedure.Whether the system is a new one or an existing submerged arc welding system, the control system may be adjusted to the customer's specifications and tailored to specific needs.
Sl no | Topic |
1 | Market Segmentation |
2 | Scope of the report |
3 | Abbreviations |
4 | Research Methodology |
5 | Executive Summary |
6 | Introduction |
7 | Insights from Industry stakeholders |
8 | Cost breakdown of Product by sub-components and average profit margin |
9 | Disruptive innovation in the Industry |
10 | Technology trends in the Industry |
11 | Consumer trends in the industry |
12 | Recent Production Milestones |
13 | Component Manufacturing in US, EU and China |
14 | COVID-19 impact on overall market |
15 | COVID-19 impact on Production of components |
16 | COVID-19 impact on Point of sale |
17 | Market Segmentation, Dynamics and Forecast by Geography, 2022-2030 |
18 | Market Segmentation, Dynamics and Forecast by Product Type, 2022-2030 |
19 | Market Segmentation, Dynamics and Forecast by Application, 2022-2030 |
20 | Market Segmentation, Dynamics and Forecast by End use, 2022-2030 |
21 | Product installation rate by OEM, 2022 |
22 | Incline/Decline in Average B-2-B selling price in past 5 years |
23 | Competition from substitute products |
24 | Gross margin and average profitability of suppliers |
25 | New product development in past 12 months |
26 | M&A in past 12 months |
27 | Growth strategy of leading players |
28 | Market share of vendors, 2022 |
29 | Company Profiles |
30 | Unmet needs and opportunity for new suppliers |
31 | Conclusion |
32 | Appendix |