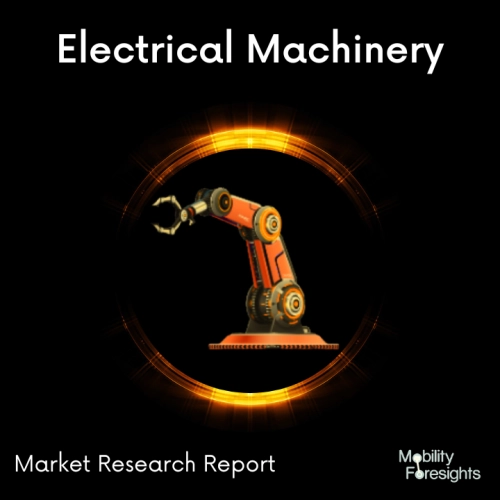
- Get in Touch with Us
Last Updated: Apr 26, 2025 | Study Period: 2024-2030
In order to smooth out surface flaws and eliminate surface roughness, a surface finishing process called roller burnishing is used. In contrast to abrasive surface finishing methods, material is shifted during roller burnishing rather than removed.
A hardened spherical or cylindrical roller serves as the tooling in most cases. While being rotated, the part has the tooling forced into its surface.
A roller burnishing tool and skiving knives are frequently used in tandem during deep hole machining. Prior to the burnishing rollers cold working the tube to produce a mirror surface finish, the skiving knives pass, scraping the inner layer of metal.
The Global Roller Burnishing Machine market accounted for $XX Billion in 2023 and is anticipated to reach $XX Billion by 2030, registering a CAGR of XX% from 2024 to 2030.
To enhance the quality of final surfaces, the roller-burnishing method has been widely utilised. However, this technique is rarely thought of for the treatment of tiny (submillimeter) surfaces. In this study, a brand-new ball-burnishing tool with a load cell incorporated and capable of gripping a 0.5 mm ball has been developed and made to work on a machining centre.
The tool was tested on specimens made of oxygen-free copper (OFC). By carrying out the experiments created using Taguchi's orthogonal array, it is possible to explore the impacts of various process parameters.
Two rounds of the experimental works were performed. To ascertain the amounts of unimportant components and the significance of certain elements, the first-round trials are used.
To ascertain the levels of the important components, the second set of trials is run. The cylindrical convex-plano lens model was then burnished using the best burnishing conditions for plane surfaces. Due to its chip-less and generally straightforward procedures, the burnishing process presents an appealing post-machining alternative.
Ball and roller burnishing are two examples of the various sorts of burnishing equipment that have been developed by researchers and made ready for use with traditional machine machines. Although the rubbing will produce heat and friction, it won't leave a trace on the plate. The stresses in the plate's surface will eventually surpass its yield strength, nevertheless, as the normal force rises.
Sl no | Topic |
1 | Market Segmentation |
2 | Scope of the report |
3 | Abbreviations |
4 | Research Methodology |
5 | Executive Summary |
6 | Introduction |
7 | Insights from Industry stakeholders |
8 | Cost breakdown of Product by sub-components and average profit margin |
9 | Disruptive innovation in the Industry |
10 | Technology trends in the Industry |
11 | Consumer trends in the industry |
12 | Recent Production Milestones |
13 | Component Manufacturing in US, EU and China |
14 | COVID-19 impact on overall market |
15 | COVID-19 impact on Production of components |
16 | COVID-19 impact on Point of sale |
17 | Market Segmentation, Dynamics and Forecast by Geography, 2024-2030 |
18 | Market Segmentation, Dynamics and Forecast by Product Type, 2024-2030 |
19 | Market Segmentation, Dynamics and Forecast by Application, 2024-2030 |
20 | Market Segmentation, Dynamics and Forecast by End use, 2024-2030 |
21 | Product installation rate by OEM, 2023 |
22 | Incline/Decline in Average B-2-B selling price in past 5 years |
23 | Competition from substitute products |
24 | Gross margin and average profitability of suppliers |
25 | New product development in past 12 months |
26 | M&A in past 12 months |
27 | Growth strategy of leading players |
28 | Market share of vendors, 2023 |
29 | Company Profiles |
30 | Unmet needs and opportunity for new suppliers |
31 | Conclusion |
32 | Appendix |