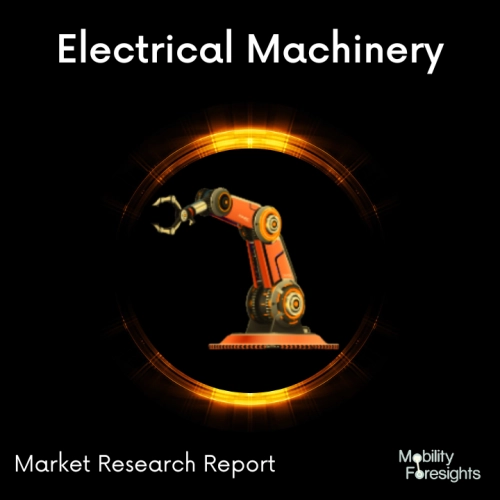
- Get in Touch with Us
Last Updated: Apr 25, 2025 | Study Period: 2024-2030
A mechanical device called a Rotary Tablet Press Machine, commonly referred to as a tablet pressing machine, is used to compress powder or granules into tablets and capsules.
A variety of materials, including medications, nutraceuticals, cleaning supplies, industrial pellets, and cosmetics, can be used to make tablets with the tablet pressing machine.
Granulated powder needs to be measured into a cavity created by two punches and a die, and then the powder needs to be compressed together by applying high force to the punches.
We shall concentrate on the rotary tablet press device used for the majority of high-speed tablet manufacturing. A mechanical device with many or many rotating tooling stations is called a rotary tablet press machine.
The Rotary Tablet Press Machine has the following benefits: High throughput can be achieved by utilizing many stations and with little labor.The output ranges from 9000 to millions of tablets per hour, which is sufficient for mass production. Rotary presses lower formulation waste, which lowers production costs.
The compression cavity is automatically controlled. Simplify the procedure.The machine controls the weight and hardness of the tablets while they are being compressed.
The Global Rotary Tablet Press Machine Market accounted for $XX Billion in 2023 and is anticipated to reach $XX Billion by 2030, registering a CAGR of XX% from 2024 to 2030.
To meet the need for manufacturing, Jspharma offers a wide variety of Rotary Tablet Press Machine in various types, series, and models. Basic models, upgraded basic models, and advanced high-speed models are the three primary series.
The distinction between them is found in pressing speed, degree of automation, and contact with the MES system.Speed: Single punch pressing machines and multiple station rotary press machines can produce 1,000 to 1,500,000 pieces per hour.
Basic control types include buttons and switch panels, upgrade types include touch screens built into the machine, and advanced control types include separate electric control cabinets and operation stations with more controlling points in PLC and the ability to communicate with the user's pharma management system.
Sl no | Topic |
1 | Market Segmentation |
2 | Scope of the report |
3 | Abbreviations |
4 | Research Methodology |
5 | Executive Summary |
6 | Introduction |
7 | Insights from Industry stakeholders |
8 | Cost breakdown of Product by sub-components and average profit margin |
9 | Disruptive innovation in the Industry |
10 | Technology trends in the Industry |
11 | Consumer trends in the industry |
12 | Recent Production Milestones |
13 | Component Manufacturing in US, EU and China |
14 | COVID-19 impact on overall market |
15 | COVID-19 impact on Production of components |
16 | COVID-19 impact on Point of sale |
17 | Market Segmentation, Dynamics and Forecast by Geography, 2024-2030 |
18 | Market Segmentation, Dynamics and Forecast by Product Type, 2024-2030 |
19 | Market Segmentation, Dynamics and Forecast by Application, 2024-2030 |
20 | Market Segmentation, Dynamics and Forecast by End use, 2024-2030 |
21 | Product installation rate by OEM, 2023 |
22 | Incline/Decline in Average B-2-B selling price in past 5 years |
23 | Competition from substitute products |
24 | Gross margin and average profitability of suppliers |
25 | New product development in past 12 months |
26 | M&A in past 12 months |
27 | Growth strategy of leading players |
28 | Market share of vendors, 2023 |
29 | Company Profiles |
30 | Unmet needs and opportunity for new suppliers |
31 | Conclusion |
32 | Appendix |