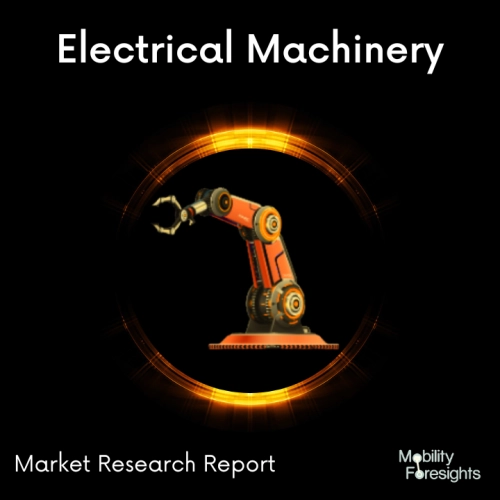
- Get in Touch with Us
Last Updated: Apr 25, 2025 | Study Period: 2023-2030
Rotary Variable Differential Transformer is the full form of the RVDT. Except for the design of the core, the RVDT design is identical to that of an LVDT.
Because the angular displacement will cause a linear change in mutual inductance between the primary and secondary windings of the transformer when it turns.
RVDTs make use of brushless, non-contacting equipment to guarantee position detecting with unlimited resolution, consistency, and longevity. Under the most strenuous working conditions, this performance ensures precise position sensing.
The linear o/p, which is proportional to the i/p angular displacement, can be obtained using this type of electromechanical transducer. The RVDT's primary function is to detect and convert angular displacement into an electrical signal.
RVDT and LVDT operate similarly, but RVDT uses a cam-type core for displacement measurement while LVDT uses a flexible iron core. Using the shaft, this core will move between the two transformer windings.
Companies must align their strategies in response to the robust shifts in the supply chain caused by the COVID pandemic and the growing push to switch to cleaner, more dependable, and sustainable energy sources.
In addition, the need for market participants in the Rotary Variable Differential Transformer industry to be more vigilant and forward-looking is pressing due to concerns regarding a slowdown in the global economy, the effects of the war in Ukraine, and the risks of stagflation with potential market scenarios.
It has been noted that COVID's impact on the economy and society is highly variable across markets and countries, so manufacturers of Rotary Variable Differential Transformers and other stakeholders are developing strategies tailored to each country.
The Global Rotary Variable Differential Transformer (RVDT) market accounted for $XX Billion in 2022 and is anticipated to reach $XX Billion by 2030, registering a CAGR of XX% from 2023 to 2030.
Zettlex - Zettlex IncOders exhibit similar high levels of reliability, robustness, and safety assurance in harsh environments due to their use of the same physical principles as RVDTs.
Zettlex inductive encoders, in contrast to RVDTs, do not require separate electronics for signal generation and processing, whereas RVDTs are typically constructed from wire windings arranged in a transformer.
As a result, sensor structures become lighter, smaller, and less expensive, offering significantly more design and integration flexibility.
In addition, Zettlex inductive encoders have been shown to reliably provide angular position and speed feedback in extreme environment applications, surpassing RVDTs of the same diameter. Zettlex inductive encoders are normally provided with a DC power source and create a flat out computerized signal.
Sl no | Topic |
1 | Market Segmentation |
2 | Scope of the report |
3 | Abbreviations |
4 | Research Methodology |
5 | Executive Summary |
6 | Introduction |
7 | Insights from Industry stakeholders |
8 | Cost breakdown of Product by sub-components and average profit margin |
9 | Disruptive innovation in the Industry |
10 | Technology trends in the Industry |
11 | Consumer trends in the industry |
12 | Recent Production Milestones |
13 | Component Manufacturing in US, EU and China |
14 | COVID-19 impact on overall market |
15 | COVID-19 impact on Production of components |
16 | COVID-19 impact on Point of sale |
17 | Market Segmentation, Dynamics and Forecast by Geography, 2023-2030 |
18 | Market Segmentation, Dynamics and Forecast by Product Type, 2023-2030 |
19 | Market Segmentation, Dynamics and Forecast by Application, 2023-2030 |
20 | Market Segmentation, Dynamics and Forecast by End use, 2023-2030 |
21 | Product installation rate by OEM, 2023 |
22 | Incline/Decline in Average B-2-B selling price in past 5 years |
23 | Competition from substitute products |
24 | Gross margin and average profitability of suppliers |
25 | New product development in past 12 months |
26 | M&A in past 12 months |
27 | Growth strategy of leading players |
28 | Market share of vendors, 2023 |
29 | Company Profiles |
30 | Unmet needs and opportunity for new suppliers |
31 | Conclusion |
32 | Appendix |