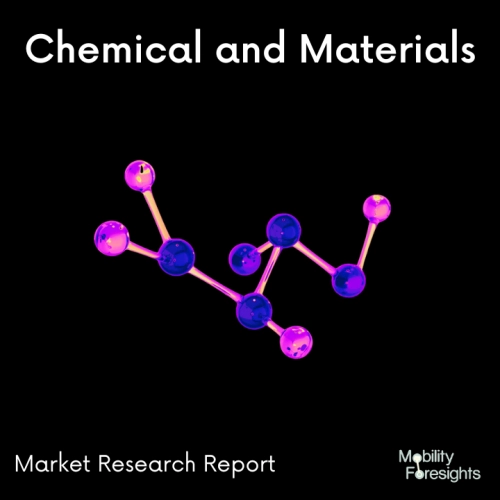
- Get in Touch with Us
Last Updated: Apr 25, 2025 | Study Period: 2024-2030
A potential class of structural materials are silumin alloys, which are silicon and aluminium alloys. They are utilised, for instance, in the production of internal combustion engine pistons. These alloys are light in weight, have a low thermal expansion coefficient, and exhibit great heat resistance. Silumin alloys are frequently used in the manufacture of machines.
Currently, Czechoslovakia produces nine different commercial grades of silumin. There aren't many facts in the literature about how Silumins' chemical makeup, structural makeup, and mechanical qualities relate to one another. Filler wire made of silicon aluminium is used while brazing and welding aluminium.
Silicon also offers fluidity features for uses that call for copper alloys. Brass may have its strength greatly increased by the addition of silicon.
Silicon may also make brasses very corrosion resistant.Silicon (Si) 4xxx - Silicon lowers the melting point of aluminium and increases fluidity. With aluminium, silicon alone results in an alloy that cannot be heated; but, when combined with magnesium, it yields an alloy that can be heated and precipitation hardened.
Aluminium-silicon alloys, also known as Silumin, are a class of lightweight, high-strength aluminium alloys that are based on the aluminium-silicon system. AlSi alloys are primarily composed of aluminium, with silicon serving as the quantitatively most significant alloying element.
The Global silumin alloy market accounted for $XX Billion in 2022 and is anticipated to reach $XX Billion by 2030, registering a CAGR of XX% from 2023 to 2030.
Aluminium-silicon alloys have established themselves as a preferred option for uses in the automotive and aerospace industries thanks to their fault-tolerant processability and reasonable static characteristics at relatively affordable costs. But when made by laser powder bed fusion, these alloys have special qualities (LPBF).
While finely dispersed silicon precipitates enable the creation of fine-grained microstructures with superior static characteristics than those of their cast equivalents, they also cause directional weak links through layered buildup.
As a result, the structure is simultaneously made stronger and more susceptible to shear and cracking. As a result, it is necessary to take these impacts into account when designing a part for LPBF manufacturing. Heat treatments can be added to the processing process to improve important qualities.
Sl no | Topic |
1 | Market Segmentation |
2 | Scope of the report |
3 | Abbreviations |
4 | Research Methodology |
5 | Executive Summary |
6 | Introduction |
7 | Insights from Industry stakeholders |
8 | Cost breakdown of Product by sub-components and average profit margin |
9 | Disruptive innovation in the Industry |
10 | Technology trends in the Industry |
11 | Consumer trends in the industry |
12 | Recent Production Milestones |
13 | Component Manufacturing in US, EU and China |
14 | COVID-19 impact on overall market |
15 | COVID-19 impact on Production of components |
16 | COVID-19 impact on Point of sale |
17 | Market Segmentation, Dynamics and Forecast by Geography, 2024-2030 |
18 | Market Segmentation, Dynamics and Forecast by Product Type, 2024-2030 |
19 | Market Segmentation, Dynamics and Forecast by Application, 2024-2030 |
20 | Market Segmentation, Dynamics and Forecast by End use, 2024-2030 |
21 | Product installation rate by OEM, 2023 |
22 | Incline/Decline in Average B-2-B selling price in past 5 years |
23 | Competition from substitute products |
24 | Gross margin and average profitability of suppliers |
25 | New product development in past 12 months |
26 | M&A in past 12 months |
27 | Growth strategy of leading players |
28 | Market share of vendors, 2023 |
29 | Company Profiles |
30 | Unmet needs and opportunity for new suppliers |
31 | Conclusion |
32 | Appendix |