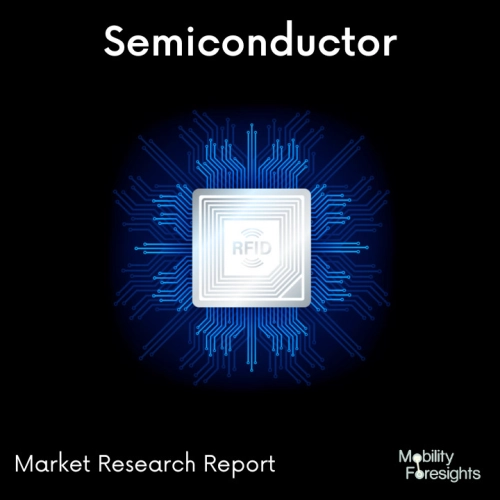
- Get in Touch with Us
Last Updated: Apr 25, 2025 | Study Period: 2024-2030
The electrical and mechanical connections between the driver electronics and the glass substrates of the liquid crystal display are often made using anisotropic conductive film (ACF), a lead-free and ecologically friendly adhesive interconnect technology.
Both the material and its paste equivalent, anisotropic conductive paste (ACP), are referred to as anisotropic conductive adhesives. (ACAs). More recently, flex-to-board or flex-to-flex connections for handheld electronic devices like mobile phones, MP3 players, or the assembly of CMOS camera modules have been made using ACAs.
The capacity to accurately adjust material volume, particle density, and particle distribution inside a sample are some of the ACF is still the most used form factor for ACAs.
This is especially true for the long-standing ACF stronghold of display interconnects, but ACF has also experienced significant expansion outside of the display industry into sectors that were previously controlled by surface-mount technology.
The main driving force behind this increase has been the capacity to interconnect components in a very small XYZ space, which has been made possible by the ability, under certain circumstances, to drastically reduce cost either by reducing component counts or total material required.
The Global singulated anisotropic conductive filmMarket accountedfor $XX Billion in 2023 and is anticipated to reach $XX Billion by 2030, registering a CAGR of XX% from 2024 to 2030.
For higher signal densities and smaller overall packages, ACF technology is utilized in chip-on-glass (COG), flex-on-glass (FOG), chip-on-board (COB), chip-on-flex (FOF), and related applications.
ACPs are typically exclusively utilized in FOF and FOB assemblies in handheld devices, or in chip-on-flex (COF) applications with low density and cost requirements, like for RFID antenna. Particularly COG connects to the display through gold bumps.
The assembling of chips onto RFID antenna substrates is a common use for ACPs in lower-end applications. Though at a far lesser level than ACFs, they are also utilized in some board or flexible assembly applications.
ACPs can't offer the same level of control over adhesive quantity and particle dispersion as ACFs, although generally being less expensive than ACFs.In order to mount the secondary substrate or device to the base substrate, the device or secondary substrate is then positioned over the base substrate and the two sides are squeezed together.
Often, only a tiny amount of heat usually just enough to make the anisotropic material slightly tacky is used during this mounting process. When conductive particles are present in a thermosetting resin, the particles become stuck between prominent spots, such as electrodes, between the substrate and the component, forming an electrical connection between the two. The thermosetting resin insulates additional particles.
In other instances, the mounting phase of the procedure is omitted, and the two sides move straight into the bonding phase.To the contrary, this would result in inefficiencies in the high volume manufacturingDue to their fine-pitch capability, straightforward manufacturing process, and affordability, anisotropic conductive films (ACFs) have been widely used as interconnection materials in semiconductor and display applications for chip-on-glass (COG), flex-on-glass (FOG), chip-on-flex (COF), and chip-on-board (COB).
In terms of materials and processing technologies, there have been numerous technological advancements. Solder ACFs, nanofiber, photo-activated ACFs, and 3D-TSV NCF materials will be highlighted in this session as recent advancements in ACF materials. New vertical ultrasonic bonding techniques and wafer level ACF processing methods will be highlighted as recent advancements in ACF processing.
One of the top producers of cutting-edge goods in a variety of industries, including electronics, is the renowned global company 3M. Singulated anisotropic conductive film (ACF), a key element in contemporary electronics assembly and connectivity technologies, was created and produced by 3M as part of their broad range of electronic solutions.
This state-of-the-art item makes it possible to make reliable and effective electrical connections between various parts, which has numerous advantages for sectors including consumer electronics, transportation, and telecommunications. Anisotropic conductive film is a special substance that permits electrical signal conduction in one direction while isolating them in the opposite direction.
ACF is the perfect interconnection method for components with closely spaced contacts or pads because of this feature. The technique of cutting a movie into discrete parts or units to enable precise and controlled bonding between components is known as singulating the movie.
Its proficiency in creating and producing singulated anisotropic conductive film adapted to certain industry requirements is one of 3M's noteworthy contributions to this field.
These films are frequently offered in rolls or sheets and come in a range of thicknesses and widths, ensuring compatibility with a wide range of assembly procedures and applications.
The singulated ACF from 3M has gained popularity among electronics makers thanks to a number of significant benefits. First off, because to its exceptional anisotropic conduction feature, the connections is made exactly where it is required, lowering the possibility of electrical short circuits and signal interference. This technique hence improves product dependability and reduces potential performance problems.
Additionally, even in applications that are susceptible to mechanical stress or temperature changes, 3M's singulated ACF offers a strong and mechanically durable connection. Because vehicle electronics components are subject to frequent vibration and changing temperatures, this reliability is essential.
The singulated ACF from 3M is compatible with a wide range of surfaces and materials, demonstrating its adaptability. The versatility of 3M's ACF gives manufacturers more design options for connecting flexible printed circuits (FPCs) to glass displays, LCD panels to driver boards, or even touch sensors to printed circuit boards (PCBs).
The capability of 3M's singulated ACF to enable high-density interconnections is a noteworthy additional benefit. The need for ACFs that can create connections between fine-pitched components has increased as the size of electronic devices continues to decrease. This challenge is met by the solution from 3M, which enables complex, compact designs without sacrificing performance.
The effective bonding method used with the singulated ACF further speeds up assembly and greatly simplifies manufacturing processes. Soldering is one of the more time-consuming, higher temperature, and potentially heat-damaging traditional procedures.
With its low-temperature bonding option, 3M's ACF speeds the assembly process, boosting output and bringing down costs. Industries are looking for environmentally acceptable options as environmental concerns increase.
The singulated ACF from 3M, which conforms with RoHS (Restriction of Hazardous compounds) laws and ensures that hazardous compounds are minimized, is a product that demonstrates the company's dedication to sustainability.
In addition to creating superior singulated ACF, 3M has become a market leader through offering first-rate customer service. The hallmarks of 3M's dedication to client satisfaction have been technical know-how, application guidance, and customized solutions.
The viability of anisotropic conductive film as a flip chip interconnect technology for MEMS devices. One modification of existing flip chip technologies with possible applicability to MEMS devices is the use of anisotropic conductive film (ACF) and stud bumping to build interconnects between die and substrates.
The most serious problems of ACF are its long-term mechanical stability and constant electrical performance.A manufacturing approach for employing ACF interconnections on MEMS devices was created during this work by examining important electrical factors, and a practical example was studied by packing a pressure sensor using ACF flip chip methods.
The results of process development and contact resistance tests employing glass substrates and Sony FP1526 anisotropic conductive film are explained and analyzed.
Using a digital wire bonder and a bench-top flip chip system, all essential processing stages, such as stud bumping, ACF application, and thermocompression bonding of the die and substrate, were completed.
After being encapsulated in perylene C and submerged in DI water for 72 hours, FP1526 produced an average contact resistance of 10.23 m, a stray capacitance value of 10 femtofarad, and less than 0.1% change in contact resistance.
Finally, the performance of an ACF-packaged MEMS piezoresistive pressure sensor was compared to that of a traditional wire-bonded device, and it demonstrated a considerable increase in temperature stability (0.34% variation in offset voltage) with no change in sensitivity.
Sl no | Topic |
1 | Market Segmentation |
2 | Scope of the report |
3 | Abbreviations |
4 | Research Methodology |
5 | Executive Summary |
6 | Introduction |
7 | Insights from Industry stakeholders |
8 | Cost breakdown of Product by sub-components and average profit margin |
9 | Disruptive innovation in the Industry |
10 | Technology trends in the Industry |
11 | Consumer trends in the industry |
12 | Recent Production Milestones |
13 | Component Manufacturing in US, EU and China |
14 | COVID-19 impact on overall market |
15 | COVID-19 impact on Production of components |
16 | COVID-19 impact on Point of sale |
17 | Market Segmentation, Dynamics and Forecast by Geography, 2024-2030 |
18 | Market Segmentation, Dynamics and Forecast by Product Type, 2024-2030 |
19 | Market Segmentation, Dynamics and Forecast by Application, 2024-2030 |
20 | Market Segmentation, Dynamics and Forecast by End use, 2024-2030 |
21 | Product installation rate by OEM, 2023 |
22 | Incline/Decline in Average B-2-B selling price in past 5 years |
23 | Competition from substitute products |
24 | Gross margin and average profitability of suppliers |
25 | New product development in past 12 months |
26 | M&A in past 12 months |
27 | Growth strategy of leading players |
28 | Market share of vendors, 2023 |
29 | Company Profiles |
30 | Unmet needs and opportunity for new suppliers |
31 | Conclusion |
32 | Appendix |