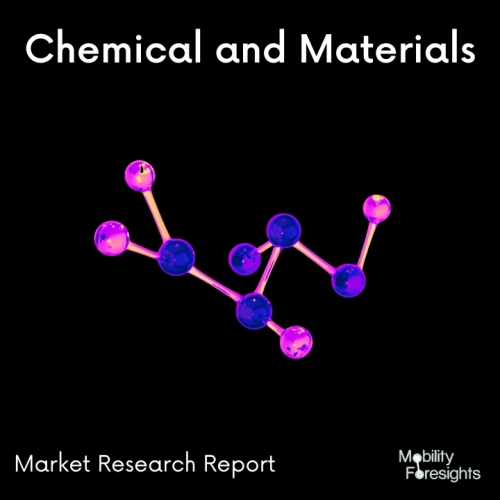
- Get in Touch with Us
Last Updated: Apr 25, 2025 | Study Period: 2023-2030
Systems or components known as filters are used to eliminate particles like dust, filth, electronic signals, etc. as they travel through filtering material or equipment. Filters can be used to remove particles from fluids, gases, electrical, and optical phenomena.
According to the production processes and dust qualities specific to the industry, numerous dust filtering equipment designs have arisen. However, a lot of these concepts were abandoned throughout their development because they flat-out didn't meet the ever-tightening pollution regulations and technological developments.
Today's most popular dust keeping devices, their benefits, and comparative drawbacks. The industrial n filters' main purpose is to prevent harmful contaminants from entering equipment.air and gas streams are cleaned by removing contaminants.Personnel and the workplace are both protected.removing and separating desired product from the air stream.
The South Africa industrial filters market accounted for $XX Billion in 2022 and is anticipated to reach $XX Billion by 2030, registering a CAGR of XX% from 2023 to 2030.
The innovative inPASS technology of South Africa is a part of Atlas Copco's next-generation air filters, which will greatly simplify maintenance and cut expenses. Customers now have the option to select from a variety of cutting-edge filter media to meet their individual air quality needs thanks to the new range.
A critical but occasionally disregarded part of a compressed air system is filtration. There is a presumption that all filters function equally and possess equivalent filtration qualities.
However, untreated or improperly treated compressed air may contain contaminants like dirt, water, and oil that endanger equipment, production methods, and finished goods. Due to this, Atlas Copco provides a broad selection of filters that can filter out even the smallest impurities, such as dust, water, and oil vapour.
The inPASS bypass is the most striking invention. Up until now, filter maintenance required either completely turning off the pressurised air system or installing three-valve bypasses all around the filters.
During maintenance, the inPASS re-routes the air via the filter head, enabling safe filter cartridge replacement without obstructing the airflow. This means that neither additional plumbing around the filters nor a suspension of production are required. The inPASS enables swift, seamless service as a result, saving customers money on both installation and operations costs.
Sl no | Topic |
1 | Market Segmentation |
2 | Scope of the report |
3 | Abbreviations |
4 | Research Methodology |
5 | Executive Summary |
6 | Introduction |
7 | Insights from Industry stakeholders |
8 | Cost breakdown of Product by sub-components and average profit margin |
9 | Disruptive innovation in the Industry |
10 | Technology trends in the Industry |
11 | Consumer trends in the industry |
12 | Recent Production Milestones |
13 | Component Manufacturing in US, EU and China |
14 | COVID-19 impact on overall market |
15 | COVID-19 impact on Production of components |
16 | COVID-19 impact on Point of sale |
17 | Market Segmentation, Dynamics and Forecast by Geography, 2023-2030 |
18 | Market Segmentation, Dynamics and Forecast by Product Type, 2023-2030 |
19 | Market Segmentation, Dynamics and Forecast by Application, 2023-2030 |
20 | Market Segmentation, Dynamics and Forecast by End use, 2023-2030 |
21 | Product installation rate by OEM, 2023 |
22 | Incline/Decline in Average B-2-B selling price in past 5 years |
23 | Competition from substitute products |
24 | Gross margin and average profitability of suppliers |
25 | New product development in past 12 months |
26 | M&A in past 12 months |
27 | Growth strategy of leading players |
28 | Market share of vendors, 2023 |
29 | Company Profiles |
30 | Unmet needs and opportunity for new suppliers |
31 | Conclusion |
32 | Appendix |