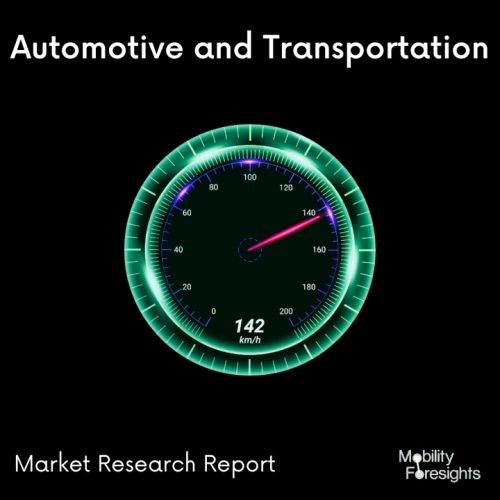
- Get in Touch with Us
Last Updated: Apr 25, 2025 | Study Period: 2024-2030
With the increased reliance on electric vehicles (EVs) becoming more and more popular, South Korea has taken steps to ensure their EV batteries are recycled in an environmentally-friendly manner. To ease the concerns of emissions from disposing of batteries and pollutants entering the environment, South Korea has put in place a series of regulations and implemented various initiatives to ensure their EV batteries are recycled properly.
To facilitate the recycling process, the government of South Korea has provided financial incentives for companies to invest in research and development regarding battery recycling and the proper methods for it. This has resulted in South Korea becoming the leader in battery recycling efficiency.
In addition, the government offers a rebate for companies that participate in recycling EV batteries, helping them to lower their overall costs and encouraging them to invest in environmentally-friendly disposal practices. Furthermore, their recycling centers provide access to the necessary facilities for proper recycling and disposal. Finally, the government of South Korea is committed to ensuring the reuse of materials from recycled EV batteries.
The government has also established a mandatory structure for effective recycling of EV batteries. This includes requiring a specific usage cycle for EV batteries, along with sizing restrictions for the battery cells. Additionally, the government ensures there is sufficient disposal and storage space that can be used by waste disposers and recyclers.
An electric car's batteries serve as a backup power source. The necessary electricity for vehicle propulsion is provided by the batteries in electric vehicles. It makes use of chemical energy that is kept in battery packs that may be recharged. After a particular amount of time, these batteries reach a point known as the end of life, at which point fresh batteries are used in their place.
The use of finite metal elements like cobalt, aluminium, and nickel is decreased by recycling the vital and recyclable components found in batteries. The market is anticipated to increase as a result of factors such as the rising demand for zero-emission cars, the tightening supply of some battery pack materials, and the expanding use of recycled items.
The South Korea EV Battery Recycling Market accounted for $XX Billion in 2022 and is anticipated to reach $XX Billion by 2030, registering a CAGR of XX% from 2024 to 2030.
As concerns over the disposal of battery trash grow, South Korean battery materials producer EcoPro plans to expand its closed-loop electric vehicle battery recycling market. A discarded product can be recycled into raw materials to make a new version of the same product, a process known as closed-loop recycling.
EcoPro's six subsidiaries, EcoPro CnG, EcoPro Innovation, EcoPro Materials, EcoPro AP, EcoPro BM, and EcoPro EM, participate in the extraction of minerals like lithium, nickel, cobalt, and manganese within the Eco-battery Pohang Campus battery recycling value chain in North Gyeongsang Province. For the collection of used batteries, EcoPro has already reached an agreement with the two facilities of LG Energy Solution in Ochang, Korea, and Poland.
EcoPro claims that its recycling technique allows for environmentally friendly processing that produces less chemical reactant and effluent, as well as a higher lithium recovery rate of over 98 percent when compared to competitors.As opposed to the majority of other businesses, which separate the three elements that leave lithium in the form of lithium solution by adding sodium carbonate to the waste solution that remains after recovering nickel, cobalt, and manganese to extract lithium carbonate, we use the chemical precipitation method.
From spent lithium-ion batteries, the business has three patents covering the extraction of lithium, nickel, cobalt, and manganese. Also, it possesses two patents: one for an environmentally friendly method of extracting lithium from hard rocks and the other for the establishment of a large-scale facility capable of producing 13,000 tonnes of lithium hydroxide annually.
Yulho and Aqua Metals will launch EV battery recycling facilities in South Korea. Aqua Metals received outstanding quality material samples from Yulho Materials, which had previously finished a pilot demonstration of their unique black mass method. Presently, Yulho is constructing a black mass plant with an annual capacity of 8,000 metric tonnes, with the intention of starting production later this year and eventually expanding to 24,000 tonnes of capacity.
In order to recover the metals and minerals contained in black mass without the use of intensive chemical processes that result in excessive carbon emissions or chemical waste, Aqua Metals currently operates a battery recycling facility in the United States. This facility makes use of the company's AquaRefining technology.
Sl no | Topic |
1 | Market Segmentation |
2 | Scope of the report |
3 | Abbreviations |
4 | Research Methodology |
5 | Executive Summary |
6 | Introduction |
7 | Insights from Industry stakeholders |
8 | Cost breakdown of Product by sub-components and average profit margin |
9 | Disruptive innovation in the Industry |
10 | Technology trends in the Industry |
11 | Consumer trends in the industry |
12 | Recent Production Milestones |
13 | Component Manufacturing in US, EU and China |
14 | COVID-19 impact on overall market |
15 | COVID-19 impact on Production of components |
16 | COVID-19 impact on Point of sale |
17 | Market Segmentation, Dynamics and Forecast by Geography, 2024-2030 |
18 | Market Segmentation, Dynamics and Forecast by Product Type, 2024-2030 |
19 | Market Segmentation, Dynamics and Forecast by Application, 2024-2030 |
20 | Market Segmentation, Dynamics and Forecast by End use, 2024-2030 |
21 | Product installation rate by OEM, 2023 |
22 | Incline/Decline in Average B-2-B selling price in past 5 years |
23 | Competition from substitute products |
24 | Gross margin and average profitability of suppliers |
25 | New product development in past 12 months |
26 | M&A in past 12 months |
27 | Growth strategy of leading players |
28 | Market share of vendors, 2023 |
29 | Company Profiles |
30 | Unmet needs and opportunity for new suppliers |
31 | Conclusion |
32 | Appendix |