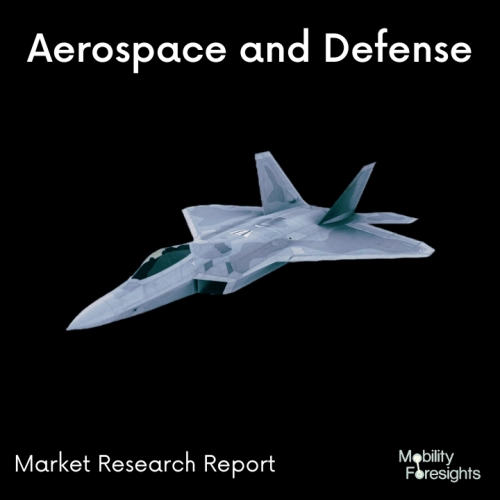
- Get in Touch with Us
Last Updated: Apr 27, 2025 | Study Period: 2024-2030
One of the planet's most elusive and challenging gases to contain is gaseous helium. It has various industrial uses and is essential as a process gas because it is the second-lightest gas after hydrogen.
In order to increase the natural gas's thermal energy, it is common practice to remove nitrogen, water vapour, carbon dioxide, helium, and other non-combustible elements as a byproduct of natural gas processing.
The liquid helium subsystem of the Ariane 5 and Ariane 6 launchers includes the helium filling valve (VRE). The VRE's primary purpose is to automatically open in order to allow the Helium tank to be refilled.
TheGlobal space propulsion helium filling valve market accounted for $XX Billion in 2023 and is anticipated to reach $XX Billion by 2030, registering a CAGR of XX% from 2024 to 2030.
Working with liquid helium requires the precise application of the proper housing material at temperatures of 4K or lower: In order to prevent cold leaks and obtain the necessary tightness for cryogenic use at the valve seat, STOHR oemploys solid stainless steel.
By minimising excessive mass, the appropriate valve body design also reduces the heat input while maintaining compliance with all standards and regulations.
Through a variety of design strategies, it is possible to minimise the heat absorption caused by the actuator as it descends into the medium via the valve spindle. The thermal energy transfer via thermal sliding contacts from the metal spindle to the outer tube of the valve
Sl no | Topic |
1 | Market Segmentation |
2 | Scope of the report |
3 | Abbreviations |
4 | Research Methodology |
5 | Executive Summary |
6 | Introduction |
7 | Insights from Industry stakeholders |
8 | Cost breakdown of Product by sub-components and average profit margin |
9 | Disruptive innovation in the Industry |
10 | Technology trends in the Industry |
11 | Consumer trends in the industry |
12 | Recent Production Milestones |
13 | Component Manufacturing in US, EU and China |
14 | COVID-19 impact on overall market |
15 | COVID-19 impact on Production of components |
16 | COVID-19 impact on Point of sale |
17 | Market Segmentation, Dynamics and Forecast by Geography, 2024-2030 |
18 | Market Segmentation, Dynamics and Forecast by Product Type, 2024-2030 |
19 | Market Segmentation, Dynamics and Forecast by Application,2024-2030 |
20 | Market Segmentation, Dynamics and Forecast by End use, 2024-2030 |
21 | Product installation rate by OEM, 2023 |
22 | Incline/Decline in Average B-2-B selling price in past 5 years |
23 | Competition from substitute products |
24 | Gross margin and average profitability of suppliers |
25 | New product development in past 12 months |
26 | M&A in past 12 months |
27 | Growth strategy of leading players |
28 | Market share of vendors, 2023 |
29 | Company Profiles |
30 | Unmet needs and opportunity for new suppliers |
31 | Conclusion |
32 | Appendix |