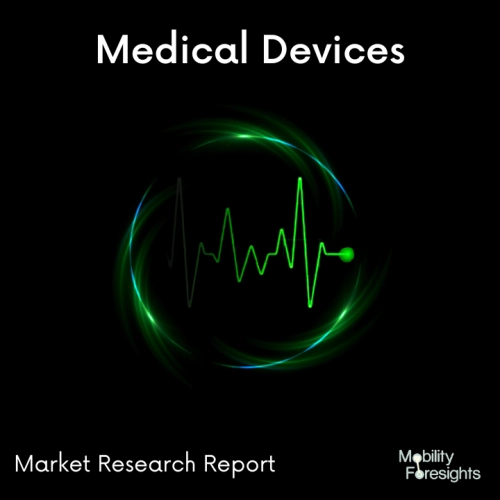
- Get in Touch with Us
Last Updated: Apr 25, 2025 | Study Period: 2024-2030
A extremely thin, practical coating is applied to a substrate using the physical vapour deposition technique known as sputter coating. A sputtering cathode is first electrically charged, which creates a plasma and causes material to eject off the target surface.
This entails material being ejected from a source called a "target" onto a "substrate" like a silicon wafer. Re-emission of the material that was previously deposited as a result of ion or atom bombardment is known as resputtering.
Typically up to tens of eV, sputtered atoms that are expelled from the target have a wide energy range (100,000 K). The sputtered ions can ballistically fly off the target in straight lines and crash energetically on the substrates or vacuum chamber (usually, only a small percentage of the ejected particles are ionised, on the order of 1%). (causing resputtering).
In contrast, at greater gas pressures, the ions move diffusively and collide with the gas atoms that serve as a moderator, eventually reaching the substrates or the wall of the vacuum chamber. Material is ejected in this process.
The process of "sputtering" is the erosion of the target material when a glow discharge is created between a cathode and anode utilising a suitable gas (usually Argon) and cathode target material (typically Gold).
An even layer of sputtered atoms will eventually deposit in all directions on the specimen's surface. For scanning electron microscopy, it will prevent charging, lessen heat damage, and enhance secondary electron emission.
Global sputter coating system market accounted for $XX Billion in 2023 and is anticipated to reach $XX Billion by 2030, registering a CAGR of XX% from 2024 to 2030.
The VacCoat Ltd. R&D team has created strategies for the design and production of a new product called DSCT-T that are based on science and engineering. The three coating techniques of sputtering, thermal evaporation of carbon, and thermal evaporation of metals are all possible with this flexible coating system that includes a turbomolecular vacuum pump.
With its compact form, the Desk Sputter Coater with Carbon/Thermal Evaporator conserves valuable laboratory space.
Sl no | Topic |
1 | Market Segmentation |
2 | Scope of the report |
3 | Abbreviations |
4 | Research Methodology |
5 | Executive Summary |
6 | Introduction |
7 | Insights from Industry stakeholders |
8 | Cost breakdown of Product by sub-components and average profit margin |
9 | Disruptive innovation in the Industry |
10 | Technology trends in the Industry |
11 | Consumer trends in the industry |
12 | Recent Production Milestones |
13 | Component Manufacturing in US, EU and China |
14 | COVID-19 impact on overall market |
15 | COVID-19 impact on Production of components |
16 | COVID-19 impact on Point of sale |
17 | Market Segmentation, Dynamics and Forecast by Geography, 2024-2030 |
18 | Market Segmentation, Dynamics and Forecast by Product Type, 2024-2030 |
19 | Market Segmentation, Dynamics and Forecast by Application, 2024-2030 |
20 | Market Segmentation, Dynamics and Forecast by End use, 2024-2030 |
21 | Product installation rate by OEM, 2024 |
22 | Incline/Decline in Average B-2-B selling price in past 5 years |
23 | Competition from substitute products |
24 | Gross margin and average profitability of suppliers |
25 | New product development in past 12 months |
26 | M&A in past 12 months |
27 | Growth strategy of leading players |
28 | Market share of vendors, 2024 |
29 | Company Profiles |
30 | Unmet needs and opportunity for new suppliers |
31 | Conclusion |
32 | Appendix |