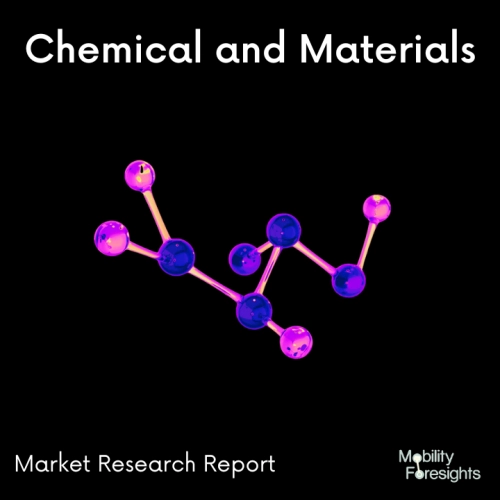
- Get in Touch with Us
Last Updated: Apr 25, 2025 | Study Period: 2023-2030
Reaction injection molding (RIM) is a relatively new way to produce structural plastic foams. In this process, highly reactive plastic liquids are mixed under high pressure and then injected into a mold to react, polymerize, and turn into foamed plastics.
Structural Reinforced RIM is the next step with respect to the traditional low pressure RTM. A complete composite part can be obtained in a time ranging from less than fiveminutes, depending on the reaction time of the chemical and on the various process parameters.
Structural Reinforced RIM consists in the injection of a multi-component mixed thermoset PU matrix into a closed mould in which a dry reinforcement preform has been previously placed, and where vacuum has been applied. After polymerization, the mould is opened and the finished part is extracted.
This process allows to obtain very resistant structural and semi-structural parts by combining reinforcement and matrix directly during injection phase. The high pressure impregnation allows to decrease raw material costs avoiding wastes.This process is suitable for 3D geometries and long fiber reinforcement.
The Global Structural Reinforced RIM market accounted for $XX Billion in 2022 and is anticipated to reach $XX Billion by 2030, registering a CAGR of XX% from 2023 to 2030.
Continuous Structural-reinforced RIM composites enable wheel blade for all-electric SUV.
Spoke-like blade inserts for automotive wheels, also known as wheelblades, have become a popular tool for design engineers looking to boost the aesthetics and aerodynamics of the wheel.
While carbon fiber is a popular material choice for these non-structural parts, many designers are looking to showcase the material in different ways besides the traditional woven look that is typically used for exterior components and accent areas.
Covestro (Leverkusen, Germany; Shanghai, China) recently announced that its Maezio continuous fiber-reinforced thermoplastic (CFRTP) composites are being used in the production of a composite wheeblade used on the aluminum wheels for the ES6 and ES8 all-electric SUVs manufactured by NIO (Shanghai, China).
The material gives OEMs and designers a new alternative to the traditional woven look of carbon fiber, offering a unique appearance with unidirectional carbon fiber optics and a variety of finishing options.
Sl no | Topic |
1 | Market Segmentation |
2 | Scope of the report |
3 | Abbreviations |
4 | Research Methodology |
5 | Executive Summary |
6 | Introduction |
7 | Insights from Industry stakeholders |
8 | Cost breakdown of Product by sub-components and average profit margin |
9 | Disruptive innovation in the Industry |
10 | Technology trends in the Industry |
11 | Consumer trends in the industry |
12 | Recent Production Milestones |
13 | Component Manufacturing in US, EU and China |
14 | COVID-19 impact on overall market |
15 | COVID-19 impact on Production of components |
16 | COVID-19 impact on Point of sale |
17 | Market Segmentation, Dynamics and Forecast by Geography, 2023-2030 |
18 | Market Segmentation, Dynamics and Forecast by Product Type, 2023-2030 |
19 | Market Segmentation, Dynamics and Forecast by Application, 2023-2030 |
20 | Market Segmentation, Dynamics and Forecast by End use, 2023-2030 |
21 | Product installation rate by OEM, 2023 |
22 | Incline/Decline in Average B-2-B selling price in past 5 years |
23 | Competition from substitute products |
24 | Gross margin and average profitability of suppliers |
25 | New product development in past 12 months |
26 | M&A in past 12 months |
27 | Growth strategy of leading players |
28 | Market share of vendors, 2023 |
29 | Company Profiles |
30 | Unmet needs and opportunity for new suppliers |
31 | Conclusion |
32 | Appendix |