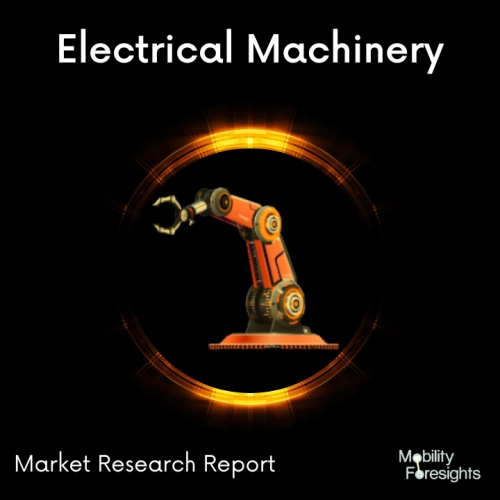
- Get in Touch with Us
Last Updated: Apr 25, 2025 | Study Period: 2023-2030
Thermal actuators use a mechanical force to push, pull, open, or move a load when the temperature changes. In hydraulic control systems, the actuator's job is to turn the hydraulic energy processed by the control elements and provided by the pump into meaningful work.
The wax undergoes a phase transition as a result of the temperature change, which happens across a constrained and adjustable temperature range, typically between 10-15°F but can be adjusted to suit a variety of applications.
The Global thermo-hydraulic actuator market accounted for $XX Billion in 2022 and is anticipated to reach $XX Billion by 2030, registering a CAGR of XX% from 2023 to 2030.
A thorough analysis of thermo-hydraulic actuators is required for the development of innovative regenerators for caloric cooling applications.
One of the most promising shapes for elastocaloric technology is similar to shell-and-tube heat exchangers because they have great thermal performance and may be used under compressive loading to overcome the short fatigue life of elastocaloric materials typically experienced in tension.
It has not yet been possible to characterise the thermo-hydraulic characteristics of shell-and-tube-like structures under the circumstances necessary for caloric cooling applications and the use of water as a heat transfer fluid.
The thermo-hydraulic performance was assessed using extensive oscillating-flow passive experimental characterization and numerical simulation.
The thermal efficiency, convective heat transfer, and friction losses of nine distinct regenerators were examined by altering the tube wall thickness, tube/rod diameter, spacing between the tubes/rods, and channel height (baffle distance).
They discovered new empirical correlations for the Nusselt number and friction factor and compared them to packed beds and parallel plate regenerators (as two most widely applied regenerator geometries in caloric cooling).
The shell-and-tube-like architecture can be used as a very effective (elasto)caloric regenerator, but to further boost convective heat transfer coefficients and NTU values, dense packing with a small(er) hydraulic diameter is needed.
The results should act as a guide for overall compression-loaded shell-and-tube-like elastocaloric regenerator optimization.
Sl no | Topic |
1 | Market Segmentation |
2 | Scope of the report |
3 | Abbreviations |
4 | Research Methodology |
5 | Executive Summary |
6 | Introduction |
7 | Insights from Industry stakeholders |
8 | Cost breakdown of Product by sub-components and average profit margin |
9 | Disruptive innovation in the Industry |
10 | Technology trends in the Industry |
11 | Consumer trends in the industry |
12 | Recent Production Milestones |
13 | Component Manufacturing in US, EU and China |
14 | COVID-19 impact on overall market |
15 | COVID-19 impact on Production of components |
16 | COVID-19 impact on Point of sale |
17 | Market Segmentation, Dynamics and Forecast by Geography, 2023-2030 |
18 | Market Segmentation, Dynamics and Forecast by Product Type, 2023-2030 |
19 | Market Segmentation, Dynamics and Forecast by Application, 2023-2030 |
20 | Market Segmentation, Dynamics and Forecast by End use, 2023-2030 |
21 | Product installation rate by OEM, 2023 |
22 | Incline/Decline in Average B-2-B selling price in past 5 years |
23 | Competition from substitute products |
24 | Gross margin and average profitability of suppliers |
25 | New product development in past 12 months |
26 | M&A in past 12 months |
27 | Growth strategy of leading players |
28 | Market share of vendors, 2023 |
29 | Company Profiles |
30 | Unmet needs and opportunity for new suppliers |
31 | Conclusion |
32 | Appendix |