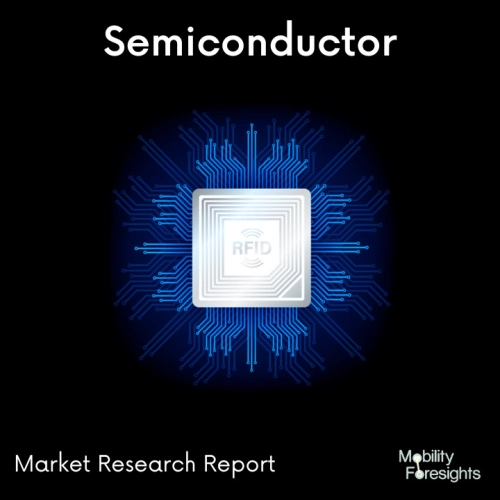
- Get in Touch with Us
Last Updated: Apr 25, 2025 | Study Period: 2024-2030
A thermoresistive sensor is an electronic device used to measure temperature. It works by measuring the electrical resistance of a material as its temperature changes. By connecting two electrodes to the material, an electrical current is passed through it and the resistance is measured.
This resistance is then used to calculate the temperature of the material. Thermoresistive sensors are widely used in a variety of applications including automotive, industrial, medical, and consumer electronics.
The most commonly used thermoresistive sensors are thermistors. Thermistors are made of a semiconductor material that changes its resistance with temperature. The resistance of a thermistor increases when the temperature increases and decreases when the temperature decreases.
This makes them ideal for measuring temperature over a wide range. They are also relatively inexpensive and have a fast response time, making them a popular choice for many applications.
Thermoresistive sensors can also be used to measure temperature over a small range. These are called RTDs, or Resistance Temperature Detectors. RTDs are made of a metal material that changes its resistance with temperature. They are typically more expensive than thermistors but they offer more accuracy and a wider temperature range.
Thermoresistive sensors are becoming increasingly popular due to their accuracy, reliability, and cost-effectiveness. They are used in a variety of applications including automotive, industrial, medical, and consumer electronics. They are a great way to quickly and accurately measure temperature over a wide range.
The Global Thermoresistive sensor market accounted for $XX Billion in 2023 and is anticipated to reach $XX Billion by 2030, registering a CAGR of XX% from 2024 to 2030.
The temperature sensor elements from TE Connectivity's RTD (Resistance Temperature Detector) are made to give accurate, reliable monitoring in applications where temperatures are extremely high or low.
Because of their well-proven design, simplicity of use, dependable performance, and prompt availability, these components offer excellent value. In harsh conditions, temperature readings can be taken precisely.
Our RTD temperature sensor elements are simple to utilise in a variety of sectors and applications, whether you're working on a new engineering design or optimising an old one. We easily make these parts available in most form factors, and the linear output requires minimal technical effort. The resistance rises as the sensor's temperature rises.
An RTD is a non-active gadget. By itself, it is unable to generate an output. By running a tiny electrical current through the sensor to produce a voltage, external electronic equipment can measure the resistance of the sensor.
Generally, the measuring current is 1 mA or less, with a maximum of 5 mA to avoid the risk of overheating. Tolerances and standardised curves are followed in the construction of RTDs.
'DIN' is the most widely used standard curve. The platinum, 100 ohm sensor's resistance vs. temperature properties, standardised tolerances, and measurable temperature range are all described by the curve. Multiple lead wire layouts are available for RTD sensors. The single element, three lead arrangement is the most widely used configuration.
Resistance must be measured in order to determine temperature using a resistance temperature detector. Resistance is always measured using unbalanced Wheatstone bridges.
To get an accurate reading while measuring the resistance of the sensing element, all external variables need to be reduced or taken into account. The readout is the total of the resistances of the lead wires and the sensing element since the resistance is connected in series with the sensor.
When the lead wires have a low resistance and the sensing element has a high resistance, two-lead RTDs are feasible. Nonetheless, it needs to be adjusted for when the lead wire resistance is rather high. A three-lead arrangement can be used to accomplish compensation.
Sl no | Topic |
1 | Market Segmentation |
2 | Scope of the report |
3 | Abbreviations |
4 | Research Methodology |
5 | Executive Summary |
6 | Introdauction |
7 | Insights from Industry stakeholders |
8 | Cost breakdown of Product by sub-components and average profit margin |
9 | Disruptive innovation in theIndustry |
10 | Technology trends in the Industry |
11 | Consumer trends in the industry |
12 | Recent Production Milestones |
13 | Component Manufacturing in US, EU and China |
14 | COVID-19 impact on overall market |
15 | COVID-19 impact on Production of components |
16 | COVID-19 impact on Point of sale |
17 | Market Segmentation, Dynamics and Forecast by Geography, 2024-2030 |
18 | Market Segmentation, Dynamics and Forecast by Product Type, 2024-2030 |
19 | Market Segmentation, Dynamics and Forecast by Application, 2024-2030 |
20 | Market Segmentation, Dynamics and Forecast by End use, 2024-2030 |
21 | Product installation rate by OEM, 2023 |
22 | Incline/Decline in Average B-2-B selling price in past 5 years |
23 | Competition from substitute products |
24 | Gross margin and average profitability of suppliers |
25 | New product development in past 12 months |
26 | M&A in past 12 months |
27 | Growth strategy of leading players |
28 | Market share of vendors, 2023 |
29 | Company Profiles |
30 | Unmet needs and opportunity for new suppliers |
31 | Conclusion |
32 | Appendix |