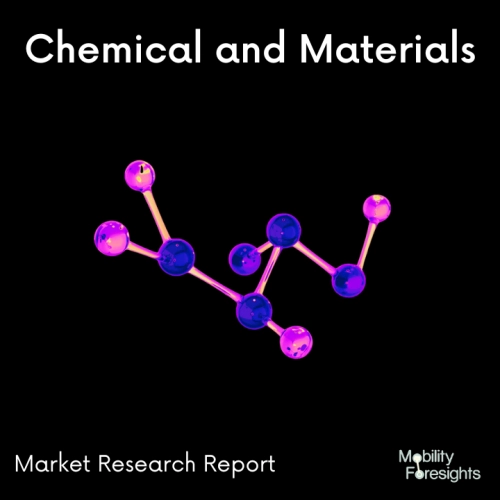
- Get in Touch with Us
Last Updated: Apr 25, 2025 | Study Period: 2023-2030
The transfer molding process is a simplified version of injection molding. It provides many of the benefits of both injection and compression press molding.
Transfer molding presses allows the molding of intricate parts while providing highly accurate dimensional control for low to medium production volume requirements. The cycle times are generally longer than injection molding, however they can be very cost competitive.
A transfer molding press can also reduce cure time by heating the material before it reaches the mold. The material can be and is forced into a closed mold by means of a hydraulically operated plunger, or by using the compressive force of the press in combination with a tooling with an internal transfer pot.
The transfer molding press was developed to facilitate the molding of intricate products with small deep holes or numerous metal inserts. It is ideal for insert molding because the tool is closed prior to the material being transfer, which limits the amount of shift with the insert parts.
Transfer Molding (RTM) is a low pressure (typically under one hundred psi), closed molding process, which offers a dimensionally accurate, and high quality surface finish composite molding, using liquid thermoset polymers reinforced with various forms of fiber reinforcements.
The Global Transfer Molding Press market accounted for $XX Billion in 2022 and is anticipated to reach $XX Billion by 2030, registering a CAGR of XX% from 2023 to 2030.
Etirol Tech elastomer technologies Transfer Molding Services.
At Elastomer Technologies Inc. (ETI) know that reducing the amount of time from the beginning to the end of the manufacturing process allows greater process efficiency which improves cost, throughput and delivery and provides stress relief for the customers.
For some projects, transfer molding and/or compression molding offers a reliable and cost-effective way to reduce the cycle times and reduce overall project costs.
To begin, workers place a piece of uncured pre-catalyzed rubber into a pot on top of a mold. When the mold closes under pressure from a molding press this material in forced through a small hole into the moldâs cavity, which is shaped in the form of the desired end product.
The molding press holds the mold closed while the rubber cures. This process time varies in relation to how quickly the material in the mold curesâoften, only a few minutes.
Once the part is cured workers open the mold, and the plunger used to inject the material, remove the transfer pad material and release the fashioned, solidified part from the mold cavity. They often trim any flash, and other excess material from the end piece at the molding press during the next molding cycle.
Sl no | Topic |
1 | Market Segmentation |
2 | Scope of the report |
3 | Abbreviations |
4 | Research Methodology |
5 | Executive Summary |
6 | Introduction |
7 | Insights from Industry stakeholders |
8 | Cost breakdown of Product by sub-components and average profit margin |
9 | Disruptive innovation in the Industry |
10 | Technology trends in the Industry |
11 | Consumer trends in the industry |
12 | Recent Production Milestones |
13 | Component Manufacturing in US, EU and China |
14 | COVID-19 impact on overall market |
15 | COVID-19 impact on Production of components |
16 | COVID-19 impact on Point of sale |
17 | Market Segmentation, Dynamics and Forecast by Geography, 2023-2030 |
18 | Market Segmentation, Dynamics and Forecast by Product Type, 2023-2030 |
19 | Market Segmentation, Dynamics and Forecast by Application, 2023-2030 |
20 | Market Segmentation, Dynamics and Forecast by End use, 2023-2030 |
21 | Product installation rate by OEM, 2023 |
22 | Incline/Decline in Average B-2-B selling price in past 5 years |
23 | Competition from substitute products |
24 | Gross margin and average profitability of suppliers |
25 | New product development in past 12 months |
26 | M&A in past 12 months |
27 | Growth strategy of leading players |
28 | Market share of vendors, 2023 |
29 | Company Profiles |
30 | Unmet needs and opportunity for new suppliers |
31 | Conclusion |
32 | Appendix |