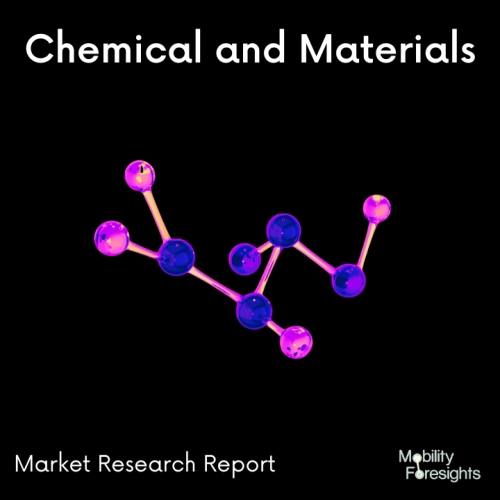
- Get in Touch with Us
Last Updated: Apr 25, 2025 | Study Period: 2024-2030
Any plastic polymer substance that becomes malleable or moldable at a specific elevated temperature and solidifies upon cooling is referred to as a thermoplastic, or thermosoft plastic. The majority of thermoplastics have large molecules. The intermolecular forces that hold the polymer chains together diminish quickly with rising temperature, resulting in a viscous liquid.
Thermoplastics may be reshaped in this state and are frequently utilised to make parts using a variety of polymer processing processes, including extrusion, calendering, injection moulding, and compression moulding. Thermoplastics are distinct from thermosetting polymers, which during the curing process generate irreversible chemical connections. Thermosets often break down and do not reform after cooling, yet they do not melt when heated.
The physical characteristics of a thermoplastic substantially alter without undergoing a phase change above its glass transition temperature and below its melting point. Certain thermoplastics retain some or all of their amorphous properties even after partially crystallising below the glass transition temperature.
When great optical clarity is required, amorphous and semi-amorphous polymers are utilised because light is strongly dispersed by crystallites that are bigger than its wavelength.
Since they lack a crystalline structure, amorphous and semi-amorphous plastics are less resistant to chemical assault and environmental stress cracking. Plasticizers can be added to reduce brittleness by making amorphous chain segments more mobile, which lowers the glass transition temperature more efficiently.
The Global Transparent Composite Thermoplastic market accounted for $XX Billion in 2023 and is anticipated to reach $XX Billion by 2030, registering a CAGR of XX% from 2024 to 2030.
T-Link is an innovative engineering Transparent Composite thermoplastic resin that L&L Products has launched as part of a new technology line. It is said to have exceptional adhesive qualities. According to L&L, the idea of T-Link was to give customers access to the resin's adhesive capabilities as well as its potential to be recycled, repaired, and formed. Reductions in process cycle times for high-performing, lighter-weight applications are the reported outcome.
T-Link is believed to conform to deep-drawn pieces because of its thermoplastic nature, enabling the fabrication of components with irregular shapes. L&L offers T-Link in pellet, film, yarn, powder, fibre veil, and unidirectional tape formats depending on the application requirements. has been used as a matrix resin alternative for a number of composite applications in the sporting goods, armour, and aerospace industries.
Sl no | Topic |
1 | Market Segmentation |
2 | Scope of the report |
3 | Abbreviations |
4 | Research Methodology |
5 | Executive Summary |
6 | Introduction |
7 | Insights from Industry stakeholders |
8 | Cost breakdown of Product by sub-components and average profit margin |
9 | Disruptive innovation in the Industry |
10 | Technology trends in the Industry |
11 | Consumer trends in the industry |
12 | Recent Production Milestones |
13 | Component Manufacturing in US, EU and China |
14 | COVID-19 impact on overall market |
15 | COVID-19 impact on Production of components |
16 | COVID-19 impact on Point of sale |
17 | Market Segmentation, Dynamics and Forecast by Geography, 2024-2030 |
18 | Market Segmentation, Dynamics and Forecast by Product Type, 2024-2030 |
19 | Market Segmentation, Dynamics and Forecast by Application, 2024-2030 |
20 | Market Segmentation, Dynamics and Forecast by End use, 2024-2030 |
21 | Product installation rate by OEM, 2023 |
22 | Incline/Decline in Average B-2-B selling price in past 5 years |
23 | Competition from substitute products |
24 | Gross margin and average profitability of suppliers |
25 | New product development in past 12 months |
26 | M&A in past 12 months |
27 | Growth strategy of leading players |
28 | Market share of vendors, 2023 |
29 | Company Profiles |
30 | Unmet needs and opportunity for new suppliers |
31 | Conclusion |
32 | Appendix |