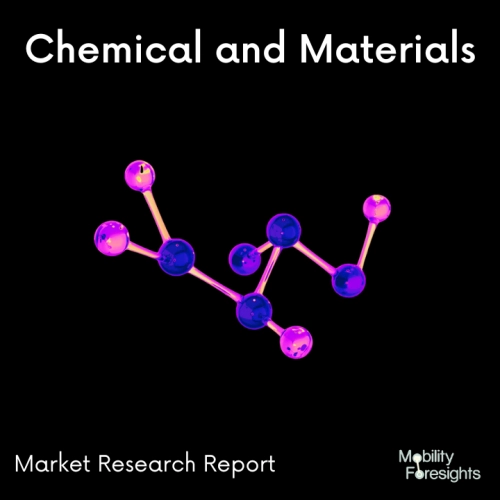
- Get in Touch with Us
Last Updated: Apr 25, 2025 | Study Period: 2023-2030
Metal matrix composites and homogenous titanium-tungsten alloys with excellent qualities. Additionally, the creation of such alloys and composites as well as the items made from such alloys and composites are revealed.
To improve tensile strength over pure titanium, the metal is frequently alloyed with other metallic components. Fe, Mn, and Cr were early commercial titanium alloying constituents that increased strength but significantly decreased ductility.
In order for the typical component to be formable (malleable) enough to get the necessary shape through metalworking and to have enough fracture resistance to deformation for use in the end-use application, good ductility is desired.
The Global Tungsten Titanium Alloy Market accounted for $XX Billion in 2022 and is anticipated to reach $XX Billion by 2030, registering a CAGR of XX% from 2023 to 2030.
Due to the alloy's outstanding heat dissipation capabilities and good surface adhesion, tungsten titanium alloy targets are frequently used as diffusion barriers and bonding layers in new semiconductor devices. The prepared product will perform more comprehensively as a result.
An alloy that combines the benefits of the transition metals tungsten and titanium is known as tungsten-titanium alloy.
It can successfully produce high-quality films because of its properties, which include increased density and purity, superior corrosion resistance, and a smaller volume expansion effect. These traits can effectively reduce the production of particles during the manufacturing process.
The process for making tungsten titanium alloy is as follows:Step 1: Under the protection of an inert environment, combine an equal amount of titanium and tungsten powder.
The tungsten powder's mass percentage is 10-65%.Step 2: The final combined material is pressed into a blank using a mechanical press or a cold isostatic press.Step 3: A vacuum sintering furnace is used to densify and sinter the resulting blank.
Step 4: A non-consumable vacuum electric arc furnace is used to melt the tungsten-titanium material that was sintered in step 3 after it has cooled.The benefits of using this tungsten-titanium alloy preparation procedure over other techniques are:. The operation is convenient and the production process is straightforward.
By combining tungsten and titanium powder as raw materials, pressing, sintering, and arc smelting processes can efficiently address the technical issues of traditional tungsten-titanium alloy's low preparation efficiency and the challenging management of material homogeneity and impurity content.
The tungsten mass percentage of the tungsten-titanium alloy material produced by this process ranges from 10 to 60%, making it appropriate for batch production.
Sl no | Topic |
1 | Market Segmentation |
2 | Scope of the report |
3 | Abbreviations |
4 | Research Methodology |
5 | Executive Summary |
6 | Introduction |
7 | Insights from Industry stakeholders |
8 | Cost breakdown of Product by sub-components and average profit margin |
9 | Disruptive innovation in the Industry |
10 | Technology trends in the Industry |
11 | Consumer trends in the industry |
12 | Recent Production Milestones |
13 | Component Manufacturing in US, EU and China |
14 | COVID-19 impact on overall market |
15 | COVID-19 impact on Production of components |
16 | COVID-19 impact on Point of sale |
17 | Market Segmentation, Dynamics and Forecast by Geography, 2023-2030 |
18 | Market Segmentation, Dynamics and Forecast by Product Type, 2023-2030 |
19 | Market Segmentation, Dynamics and Forecast by Application, 2023-2030 |
20 | Market Segmentation, Dynamics and Forecast by End use, 2023-2030 |
21 | Product installation rate by OEM, 2023 |
22 | Incline/Decline in Average B-2-B selling price in past 5 years |
23 | Competition from substitute products |
24 | Gross margin and average profitability of suppliers |
25 | New product development in past 12 months |
26 | M&A in past 12 months |
27 | Growth strategy of leading players |
28 | Market share of vendors, 2023 |
29 | Company Profiles |
30 | Unmet needs and opportunity for new suppliers |
31 | Conclusion |
32 | Appendix |