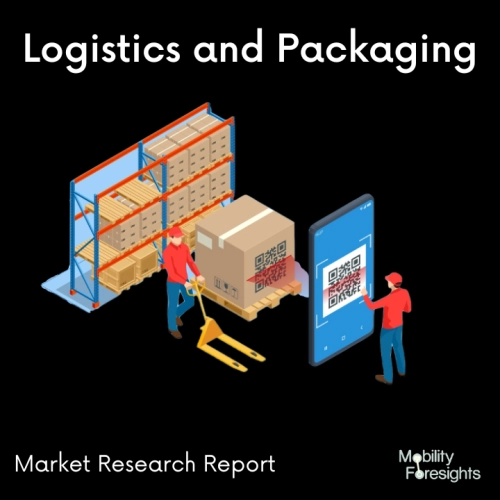
- Get in Touch with Us
Last Updated: Apr 25, 2025 | Study Period: 2024-2030
AGVs are much more conventional and have undergone years of development. AMRs may be better for lighter loads and quicker to install. AGVs are strong and take special care of the greater and greater development of burdens.
Despite their differences, both solutions accomplish the same objective: Make your warehouse process automated. As a result, when defining a project, you should choose a solution that works best for you. An AGV is the best option for a wider range of operations.
The adaptability of both systems is an essential factor to take into account. At ground level, both AGVs and AMRs can allow you to define your operations in a flexible way. However, if there are a lot of SKUs, an AMR usually works best. Since AMRs primarily reduce travel time and enable operators to concentrate on other tasks, the higher number of SKUs is required to account for noticeable output.
The Turkey Automated Guided Vehicle Market accounted for $XX Billion in 2023 and is anticipated to reach $XX Billion by 2030, registering a CAGR of XX% from 2024 to 2030.
At Shi sui Premium Outlets, an outlet mall in Chiba Prefecture, Mitsubishi Heavy Industries, Ltd. (MHI) and Mitsubishi Heavy Industries Machinery Systems, Ltd. today began Phase 2 of demonstration testing of an automated valet parking system. "Stan" is an acronym for the automated guided vehicle (AGV) robots used in the system. Stanley Robotics, a French venture-backed company, makes them.
The first application of this automated valet parking system in a commercial complex in Japan was Phase 1 of the demonstration testing. There were two main goals in the beginning: to check taking care of execution utilizing AGV robots, and to assess client fulfillment. The original system has been upgraded for Phase 2, and a brand-new smartphone app has been added.
Testing will focus on confirming the improved system's ability to automate the four aspects of valet parking: transportation to the parking space, parking, vehicle collection, delivery, and exit Similar to Phase 1, the demonstration testing will take place in a designated parking area at Shi sui Premium Outlets, a Chiba Prefecture outlet mall that Mitsubishi Estate-Simon Co., Ltd. and Mitsubishi Estate Group jointly developed and run. The use of vehicles will be made by mall employees.
Sending of the upgraded robotized valet stopping framework empowers huge decrease in holding up time at vehicle get, as the client can affirm the vehicle's availability and the blockage status by cell phone application.
Because the vehicle can be dropped off and picked up without having to interact with anyone, the risk of contracting COVID infection is reduced, which also improves user convenience and safety. By giving the user more time to enjoy the commercial complex's shopping and dining options, system deployment adds value for the business owner.
MHI Group will use the information from the demonstration testing to get automated valet parking systems early commercialized and used in hospitals, airports, commercial complexes, amusement parks, and other large facilities in Japan.
In order to achieve a carbon-neutral society, MHI Group is currently developing its solutions business through the development of smart social infrastructures as part of its growth strategy outlined in its Medium-Term Business Plan.
By starting to lead the packing giving AGV robot-based computerized valet stopping frameworks, MHI Gathering will add to the acknowledgment of a protected, helpful and reasonable society.
Sl no | Topic |
1 | Market Segmentation |
2 | Scope of the report |
3 | Abbreviations |
4 | Research Methodology |
5 | Executive Summary |
6 | Introduction |
7 | Insights from Industry stakeholders |
8 | Cost breakdown of Product by sub-components and average profit margin |
9 | Disruptive innovation in the Industry |
10 | Technology trends in the Industry |
11 | Consumer trends in the industry |
12 | Recent Production Milestones |
13 | Component Manufacturing in US, EU and China |
14 | COVID-19 impact on overall market |
15 | COVID-19 impact on Production of components |
16 | COVID-19 impact on Point of sale |
17 | Market Segmentation, Dynamics and Forecast by Geography, 2024-2030 |
18 | Market Segmentation, Dynamics and Forecast by Product Type, 2024-2030 |
19 | Market Segmentation, Dynamics and Forecast by Application, 2024-2030 |
20 | Market Segmentation, Dynamics and Forecast by End use, 2024-2030 |
21 | Product installation rate by OEM, 2023 |
22 | Incline/Decline in Average B-2-B selling price in past 5 years |
23 | Competition from substitute products |
24 | Gross margin and average profitability of suppliers |
25 | New product development in past 12 months |
26 | M&A in past 12 months |
27 | Growth strategy of leading players |
28 | Market share of vendors, 2023 |
29 | Company Profiles |
30 | Unmet needs and opportunity for new suppliers |
31 | Conclusion |
32 | Appendix |